TMS – Implementation Effects
Results of automating logistics processes with TMS and implementing end-to-end analytics with the ability to track all indicators in real time

We assist companies of various sizes and formats in optimizing transport logistics:
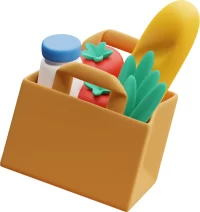
Food & Beverages
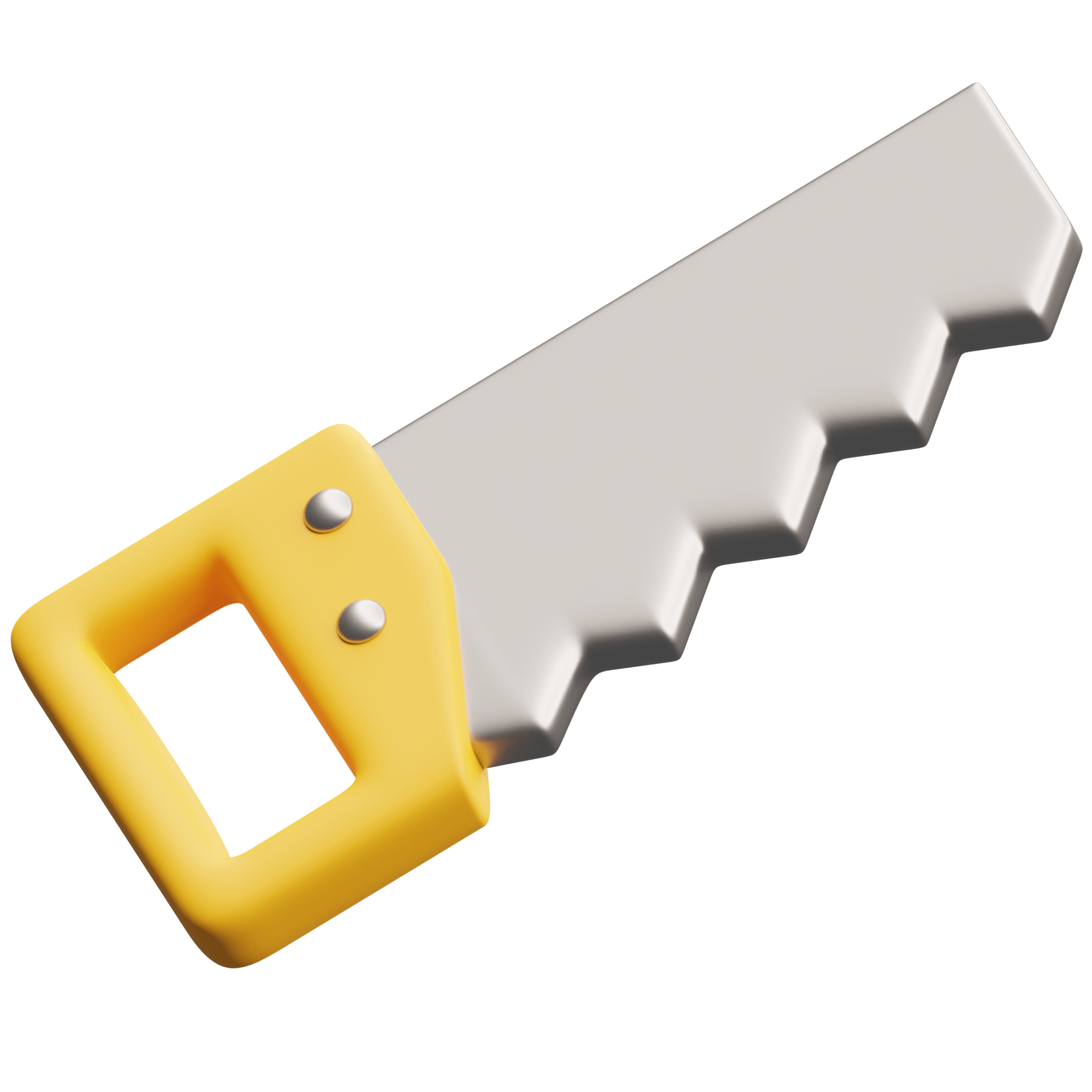
DIY
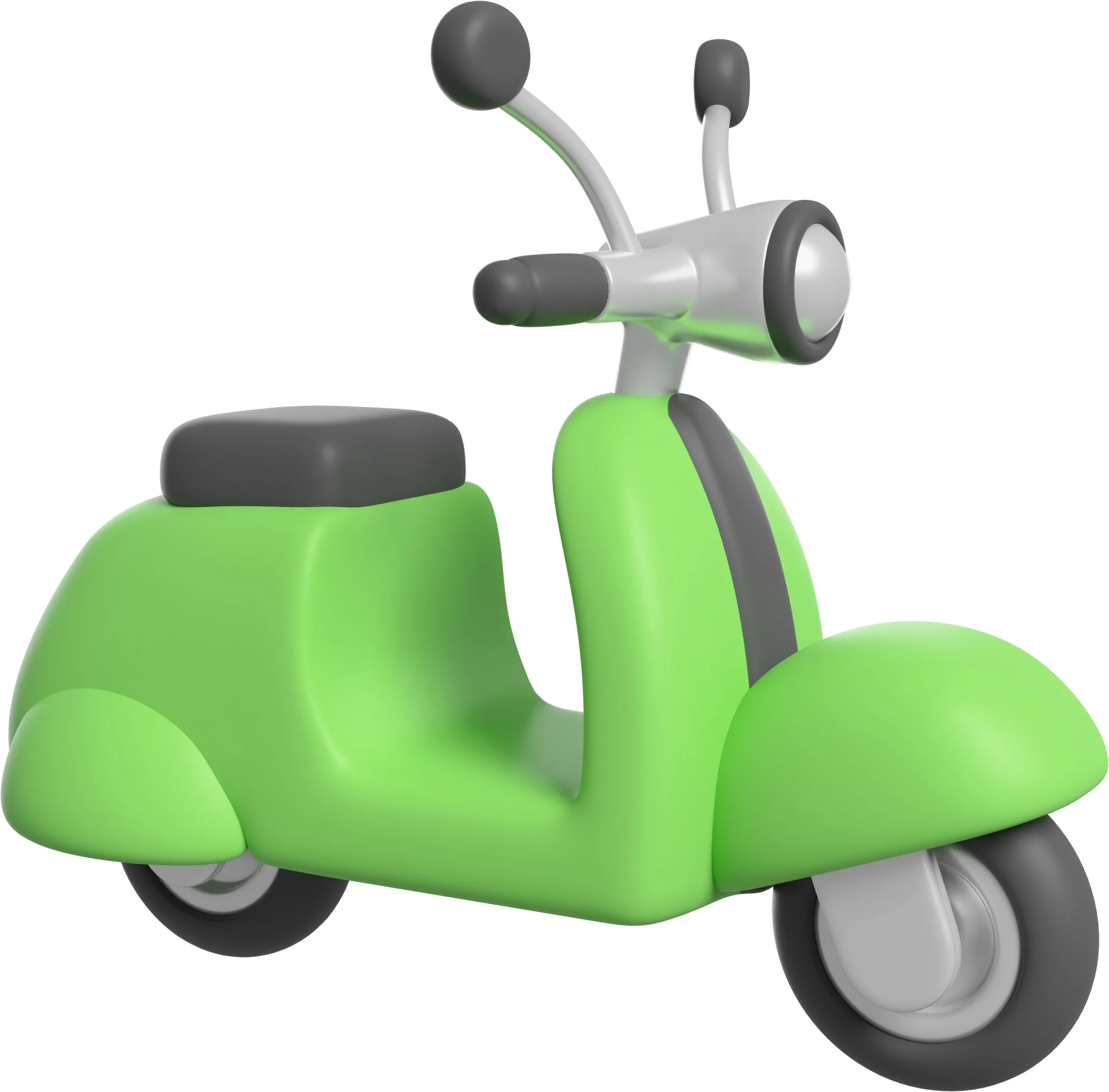
Dark Store
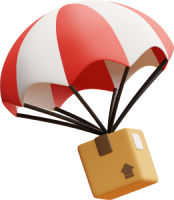
3PL operators
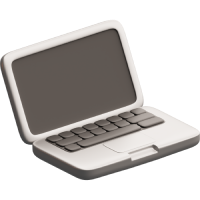
E-commerce
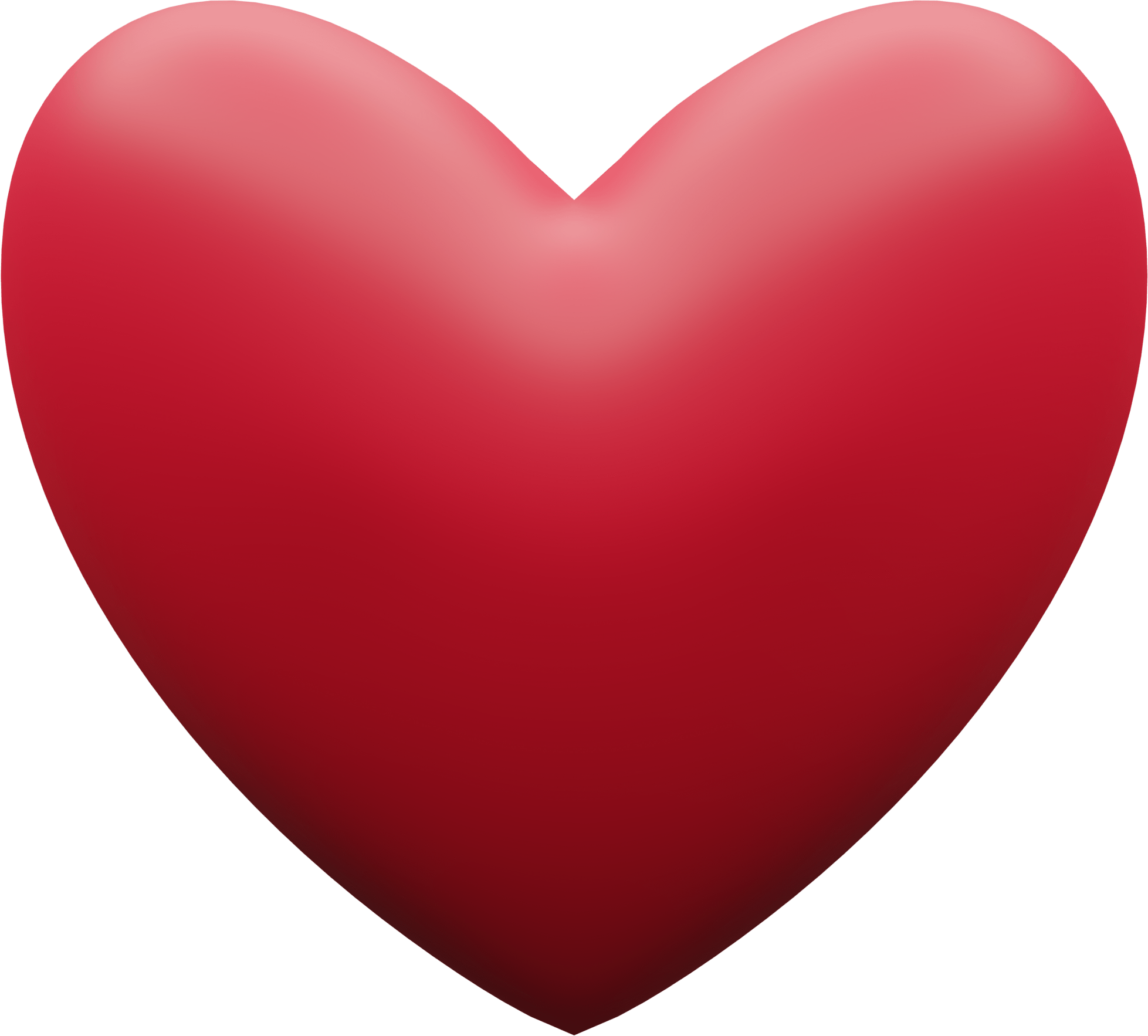
Pharmacies
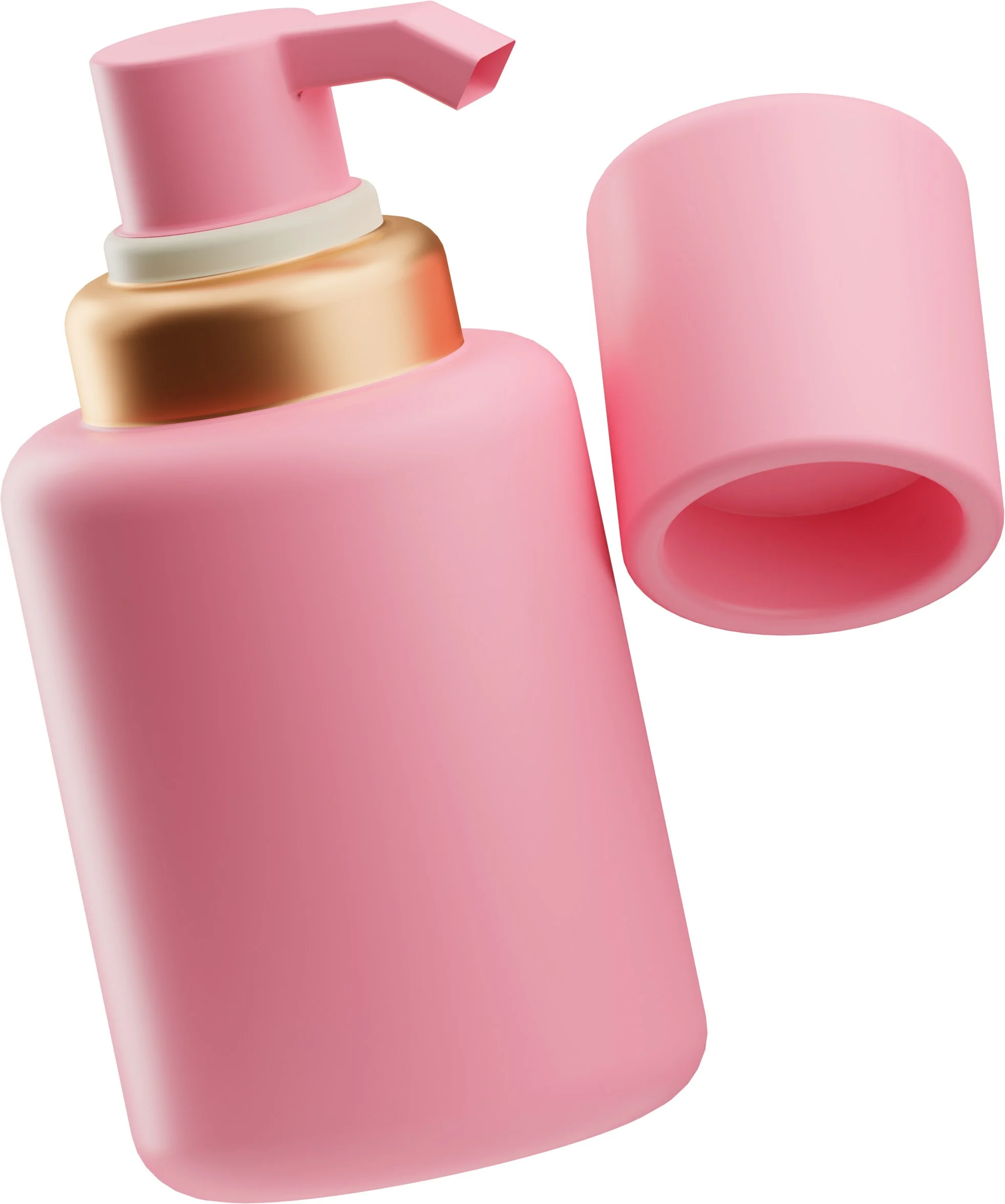
Drogerie
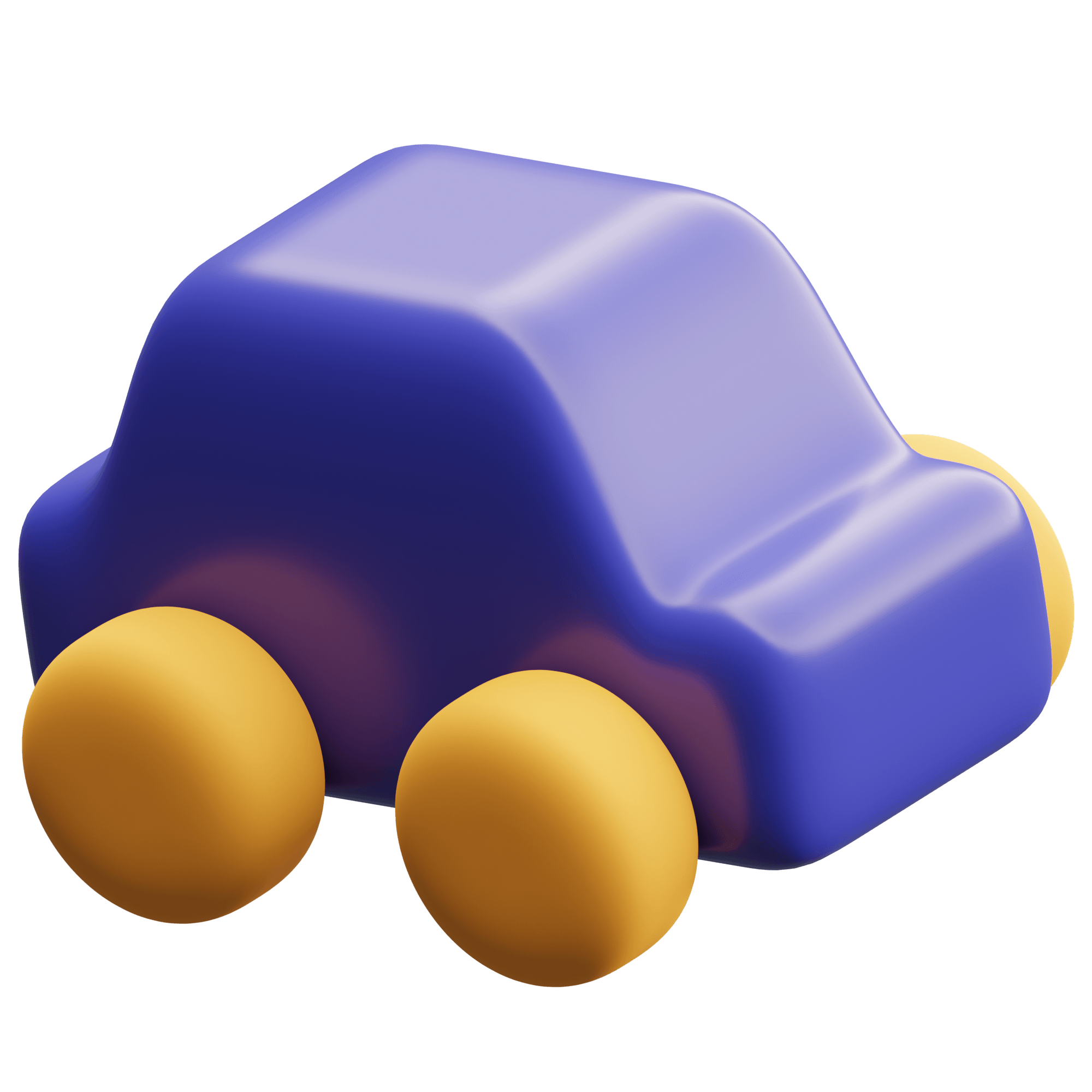
Auto parts and accessories

Technology and electronics

Home goods
TMS: features and capabilities
Route Planning
Maps
Operational control of delivery
Control
Delivery Quality
Profitability
Ratings
Mobile Application
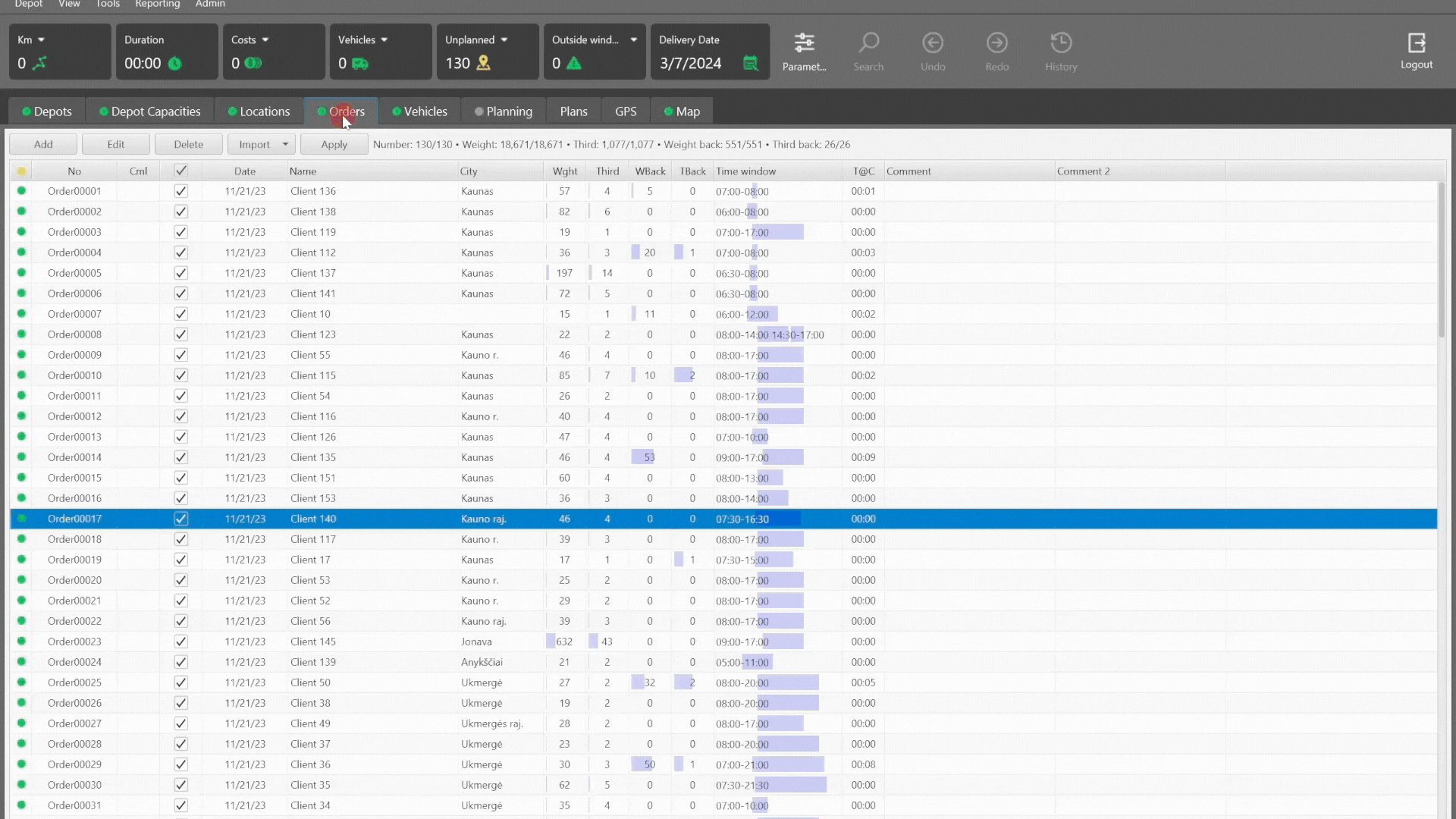
-
Route Planning
Fully automated route planning, including 15 types of possible constraints. Routes for thousands of orders in just a few minutes.
-
Utilizing Depot Capabilities
Plan a number of simultaneous vehicle loadings based on specified warehouse operation parameters.
-
Comprehensive Route Information
Start and end points of the route, carrier travel time, and time spent unloading Vehicle load information by weight and volume, both actual and percentage.
-
Sequential Routing for Each Vehicle
Automatic calculation of unloading time at each point based on order parameters.
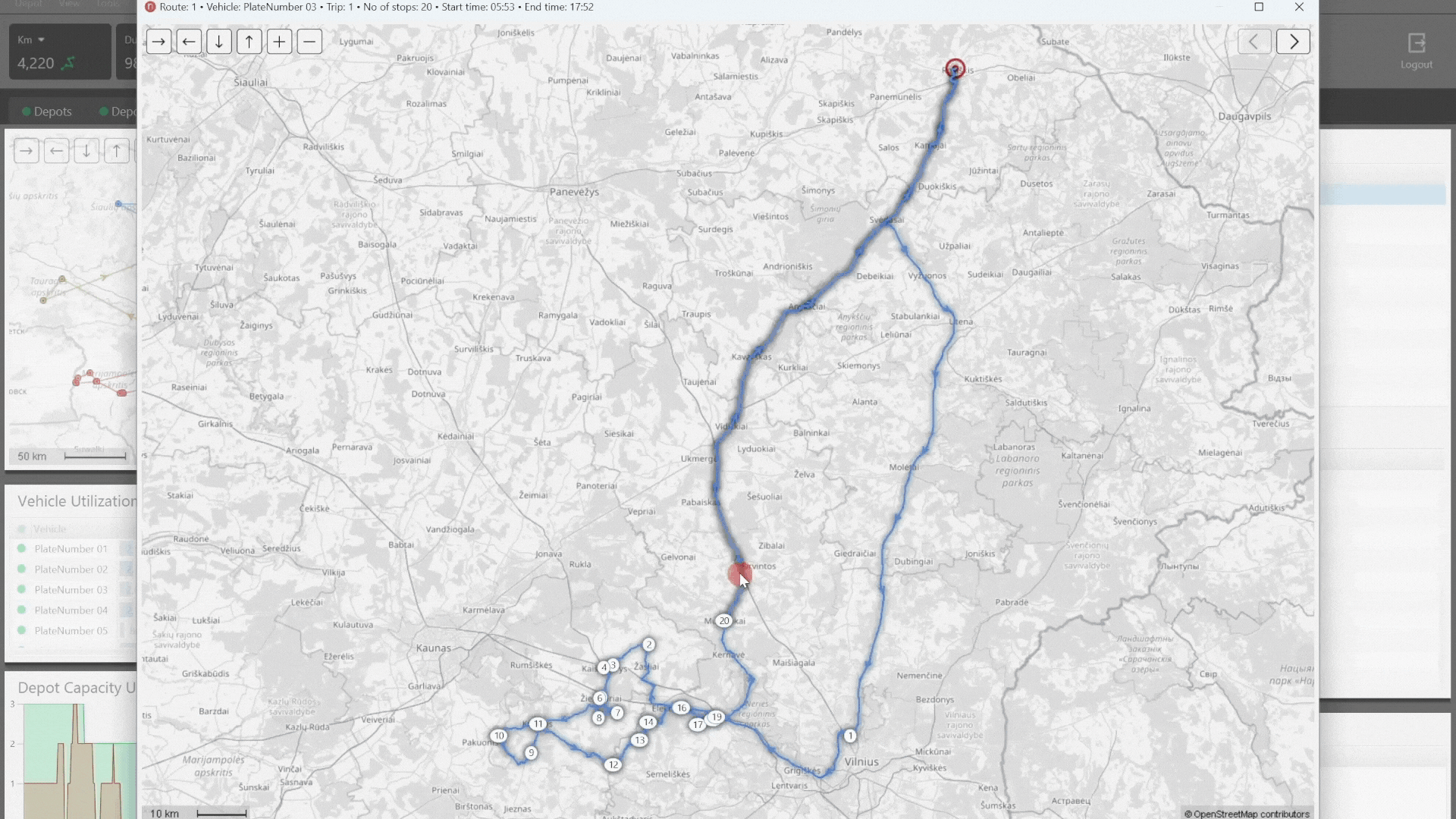
-
Specialized cards for freight transport
OpenStreetMap maps are ideally suited for planning truck routes: they show road conditions, restrictions (road closures, maneuvering bans, restrictions for heavy vehicles, etc.), and speed limits.
-
Corrections
Additional restrictions can be added to the map, both temporary and permanent, to close areas or roads if necessary.
-
Constant map updates
The maps are updated weekly and store data for the previous six months, thus showing the most reliable information.
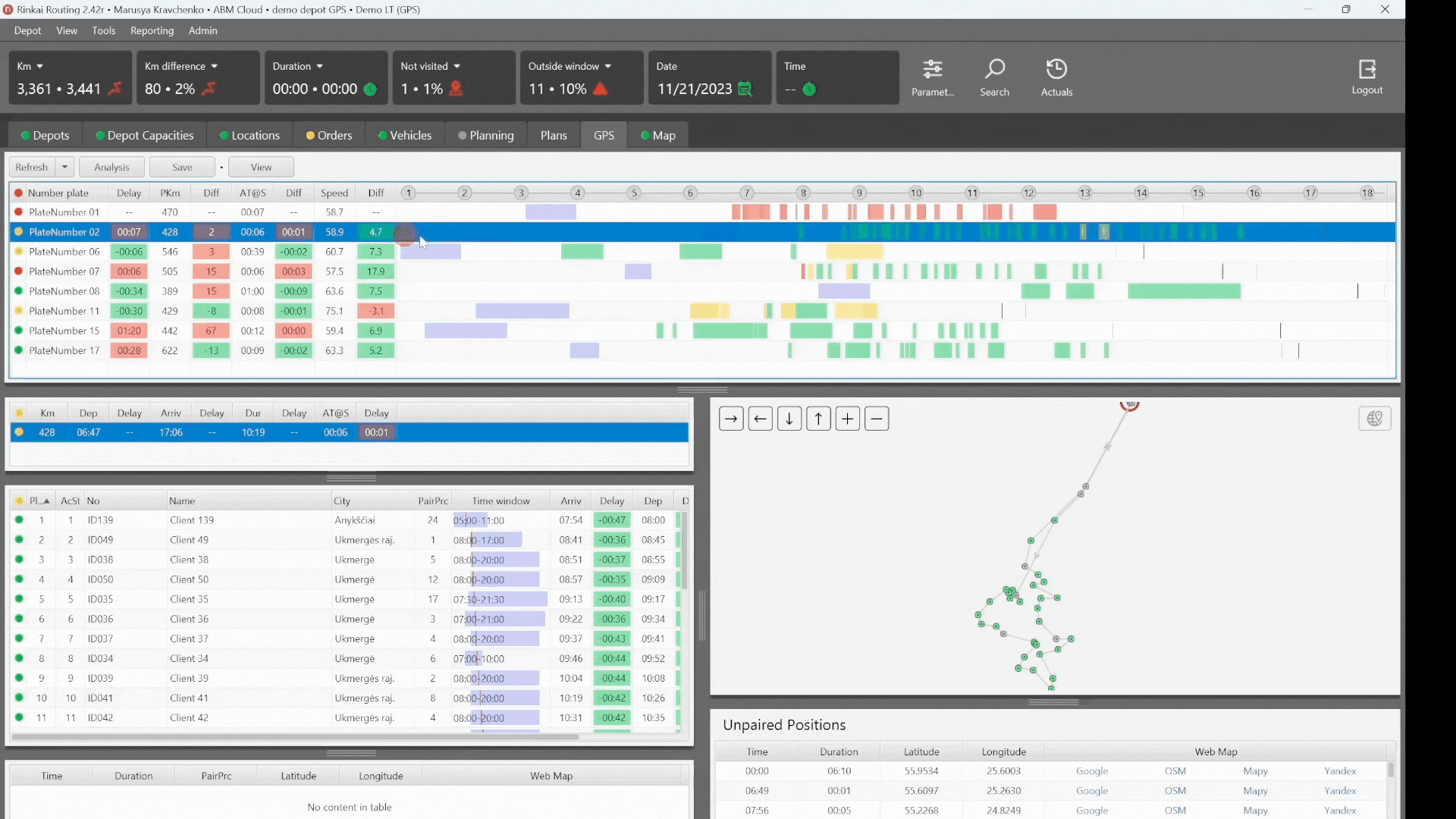
-
Analysis of Route Performance using GPS Data
Complete analysis of executed routes with a display of planned versus actual performance indicators.
-
Route Analysis for a Specific Vehicle
For each vehicle, the planned and actual route execution is displayed. For example,you can see the time window ( shown in purple) and the driver's arrival time at the point ( shown in red) in the diagram. The exact arrival, departure times, and deviation from the planned time are also shown.
-
Viewing the Route on the Map
Comparison between the planned route for the vehicle and the actual route taken by the driver.
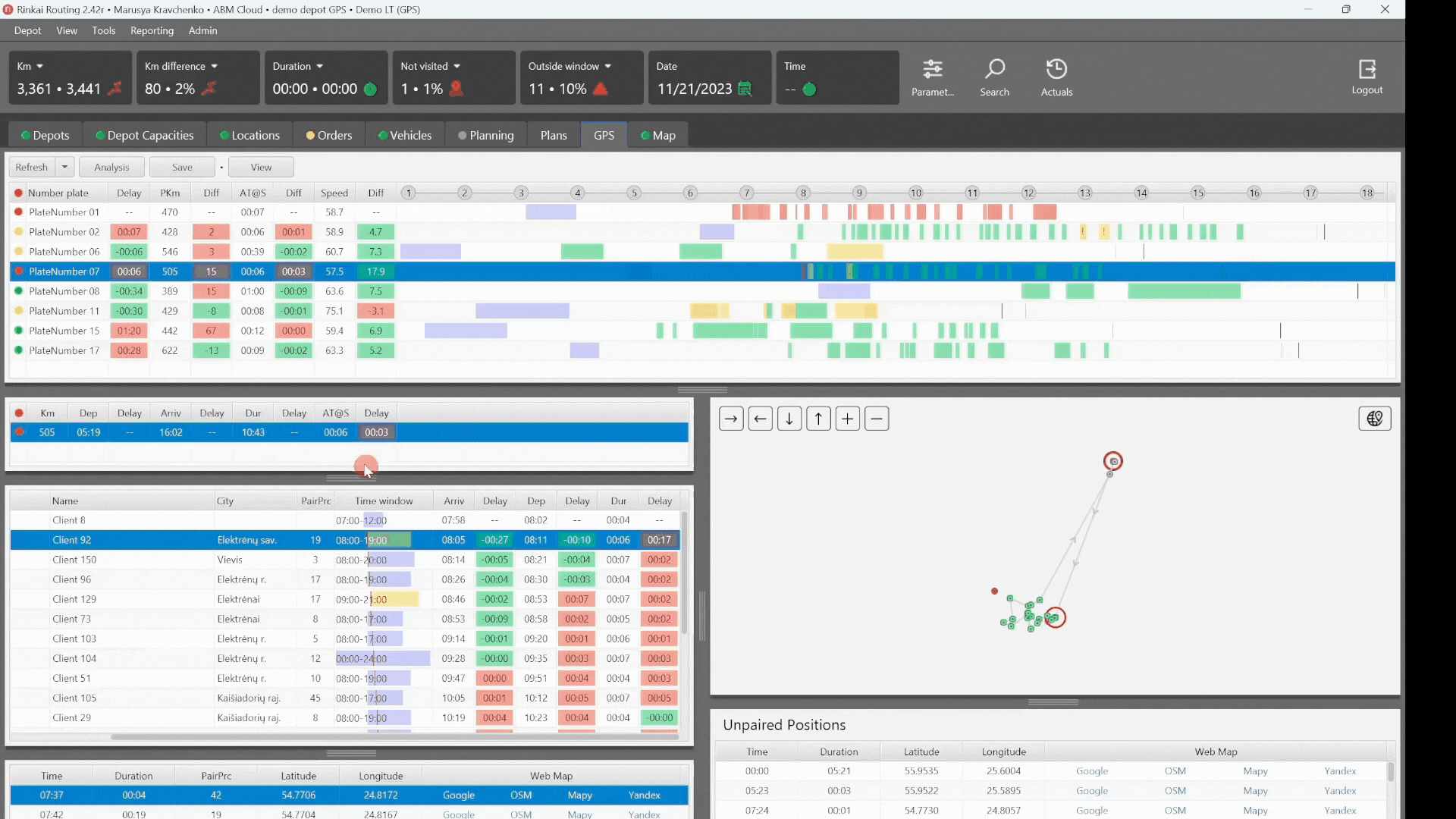
-
Route Performance Analysis
Detailed breakdown of the planned versus actual performance in terms of vehicles and clients, including mileage, average time at points, their visitation frequency, arrival outside the time window, saved or exceeded time at each point. In the «Servicing» section, comments from drivers and photos are also available for review.
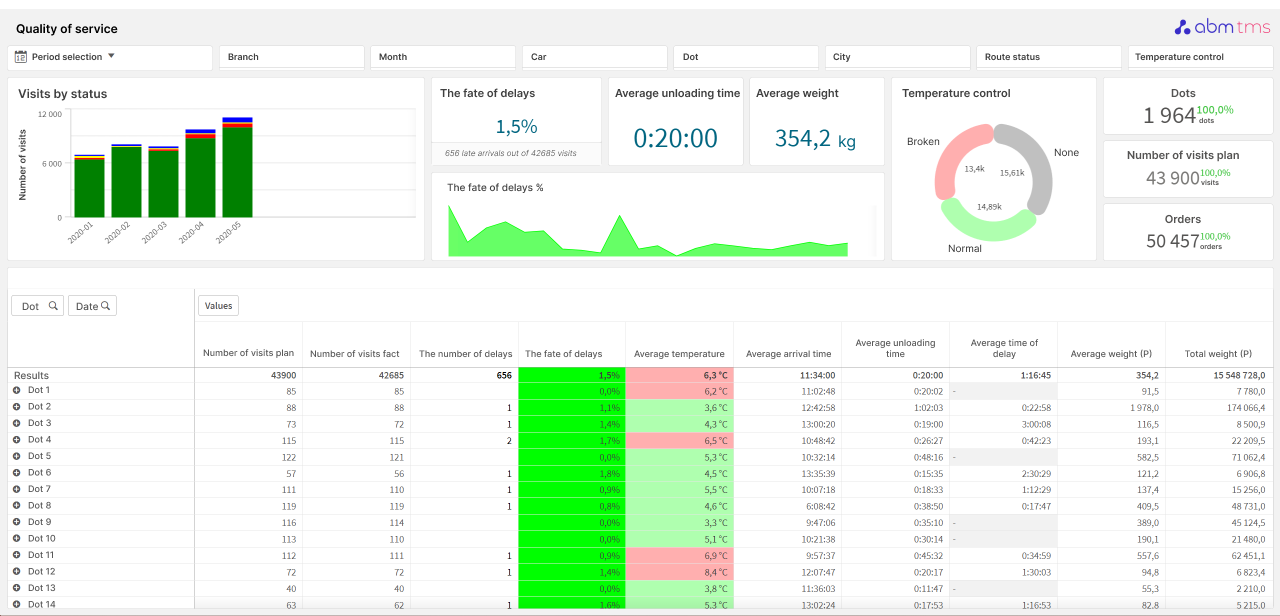
-
Delay Control
Indicators allow tracking the monthly adherence to order timings. Green indicates on-time arrival, red represents non-visitation, yellow denotes delays, and blue indicates early arrivals.
-
Temperature Mode
Complete control over adhering to the temperature regime, especially crucial for delivering "fresh" category products. Green indicates normalcy, red represents a violation, and gray indicates the absence of data.
-
Visit Statistics
There is an option to analyze specific points as well as the entire network. The metrics include planned versus actual visit counts, the absolute number of delays, the percentage of delays among all deliveries, average arrival times, unloading times, delays, and overall and average delivery weight.
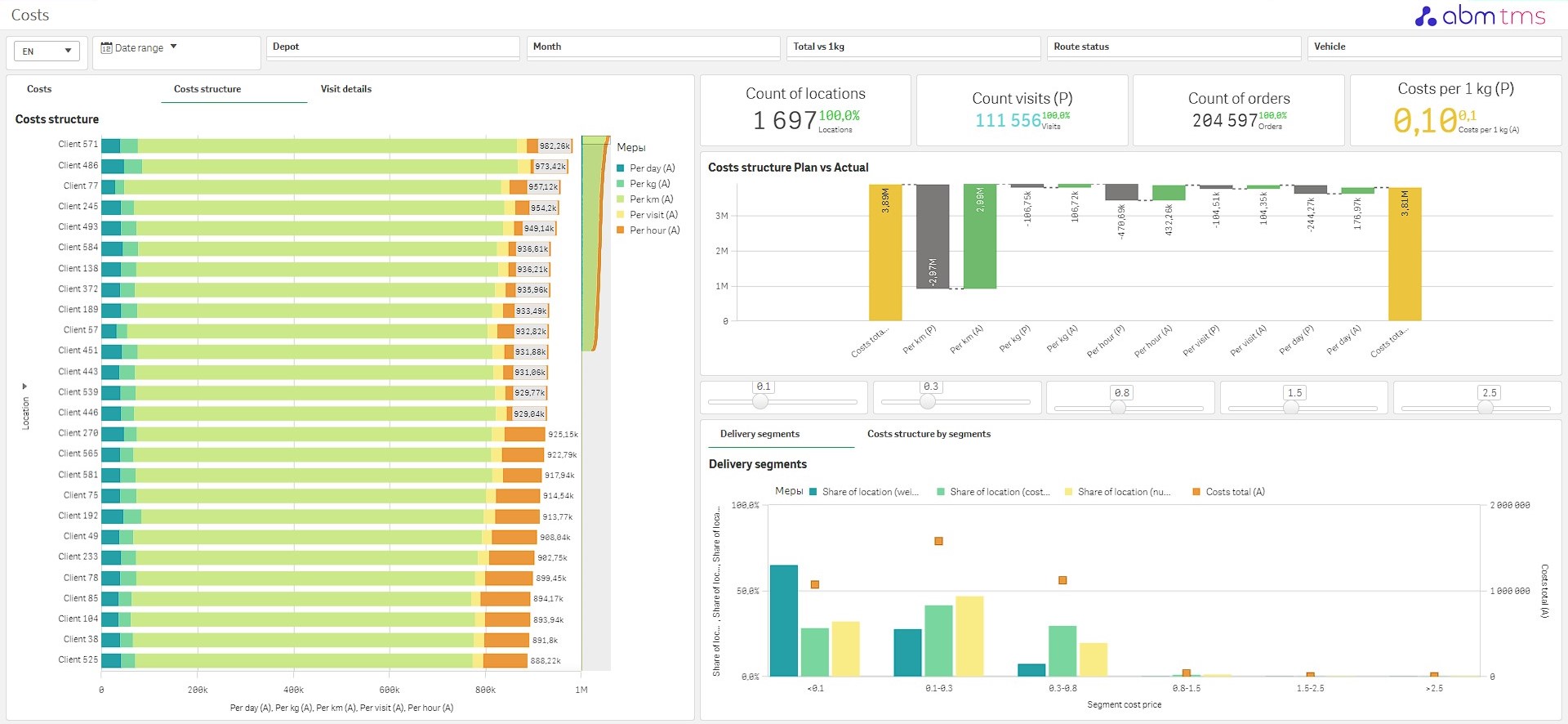
-
Cost Structure
Comparison of planned versus actual overall costs and costs per 1 kg of product.
-
Plan versus actual breakdown by cost types.
Comparison of planned and actual values for all components influencing the cost of delivery (visit bonuses, daily rates, costs per 1 kg, vehicle mileage).
-
Segments of Delivery Cost
The chart divides the total weight of deliveries into segments based on the cost of delivery per 1 kg, showing the quantity of points corresponding to each segment of deliveries.
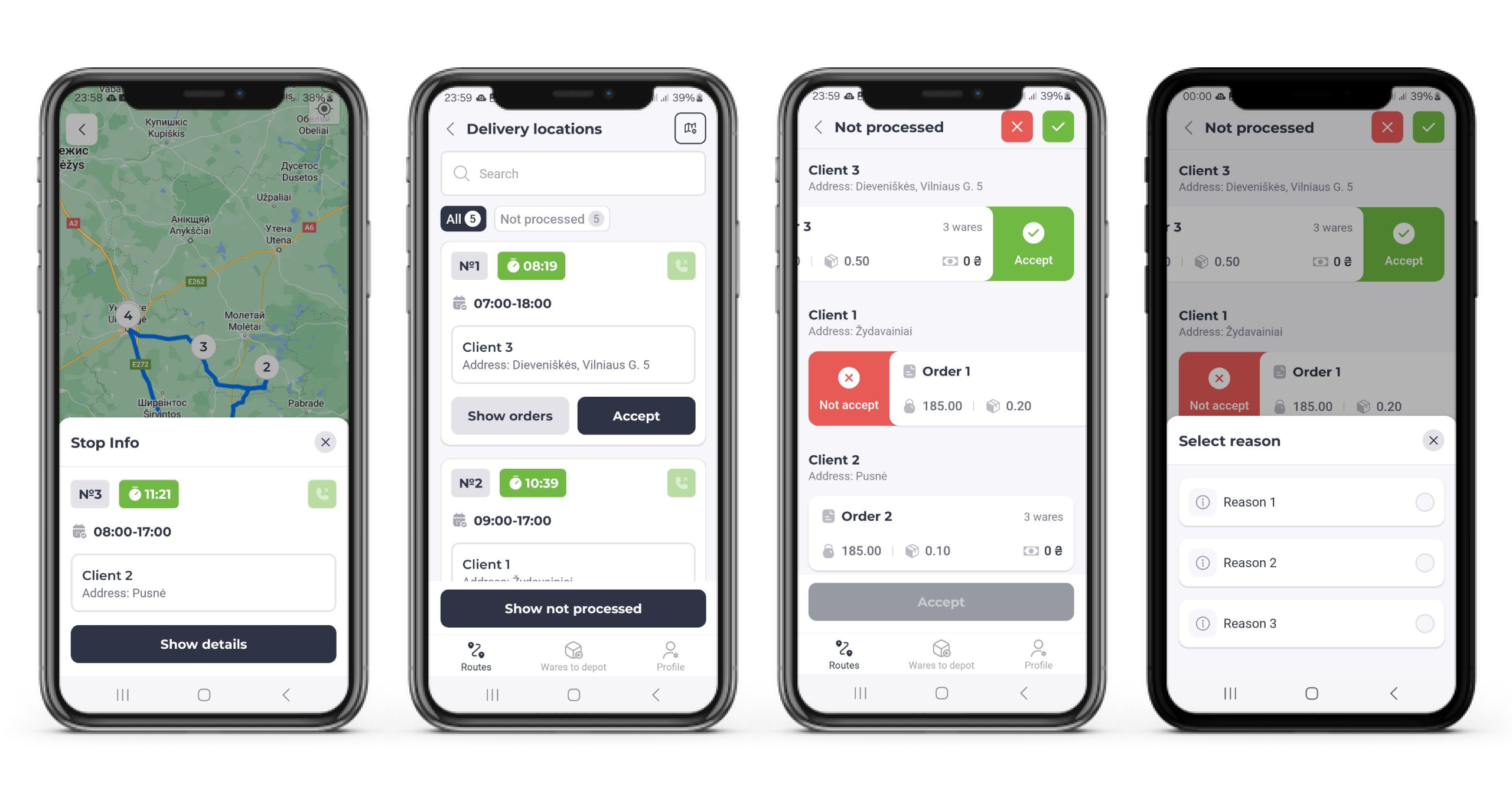
-
Convenient Delivery Management: From Receipt to Dispatch
Confirmations of order loading directly at the depot and route navigation for the driver. The logistics manager can monitor the progress of order fulfillment using the order tracker feature and the administrative panel, ensuring high-quality customer service.
-
Maximum Delivery Control
The order progress tracking feature keeps you informed about the status of each order, allowing you to stay updated on its current stage.. Additionally, drivers can make calls to customers directly through the application and record conversations for future use. Necessary changes to orders can also be made directly in the mobile application.
-
Efficient Management of the Goods Receipt and Transfer Process
API integration with MOS/WMS enables automatic data exchange with warehouse management systems, ensuring efficient coordination between different processes and speeding up warehouse operations.
We appreciate you contacting us. One of our specialists will get back in touch with you soon. Have a great day!
Rinkai TMS algorithms in optimizing last mile delivery
Plan your route and deliver orders with the lowest possible transport costs
How does it work:
Imagine a very simple scenario in which you plan your route so that the difference in efficiency does not exceed 5% in comparison with the system route.
- Try to deliver all orders of different weights as cheaply as possible
- You have 5 cars with different carrying capacity and different mileage
- Click to include your order in the itinerary of your chosen vehicle
- When you plan your orders, you can compare them with the route that the system builds. You will see a financial comparison in the piggy bank
Implementation Process
• Identify the parameters that need to be considered when planning routes.
• Drawing up a project with a work schedule.
• Setting up automatic data exchange between the customer's accounting system, WMS, and transport management system.
Integration with a GPS data provider.
• Development of supporting documentation.
• Training management to work with the analytical tools.
• Launching the system, building and analyzing the first routes.
• Adjustment and analysis of the first routes.
01 Diagnosis
02 Process Optimization
03 Automation
Diagnosis
• Identify the parameters that need to be considered when planning routes.
• Drawing up a project with a work schedule.
Process Optimization
• Setting up automatic data exchange between the customer's accounting system, WMS, and transport management system.
Integration with a GPS data provider.
• Development of supporting documentation.
Automation
• Training management to work with the analytical tools.
• Launching the system, building and analyzing the first routes.
• Adjustment and analysis of the first routes.
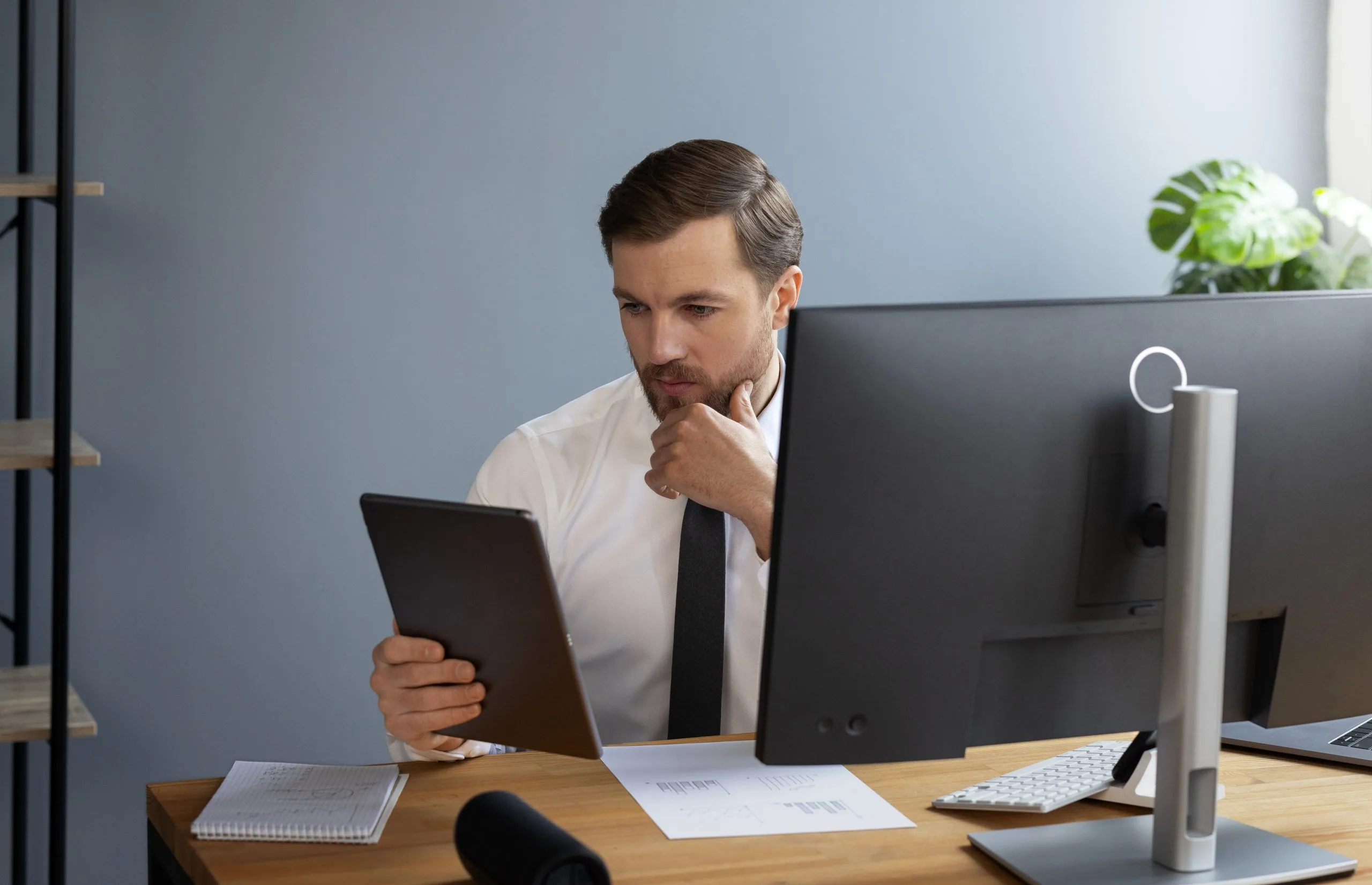
Cloud-based TMS system for transportation management
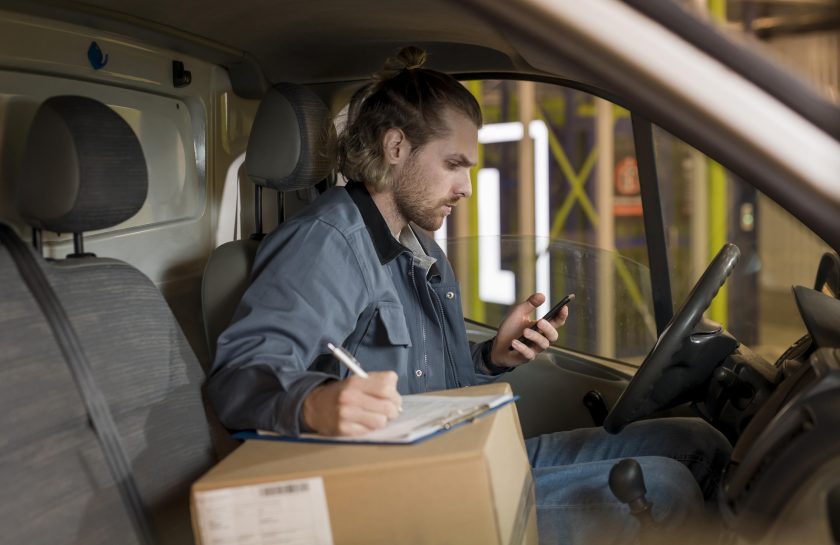
Planning Route optimization for 3pl companies
3PL operators process thousands of orders from various client companies every day. Scheduling these orders manually can increase costs and delay deliveries. The best way to improve logistics efficiency is to optimize routes. Optimization with a TMS allows you to build the fastest, shortest, and most cost-effective routes for delivery.
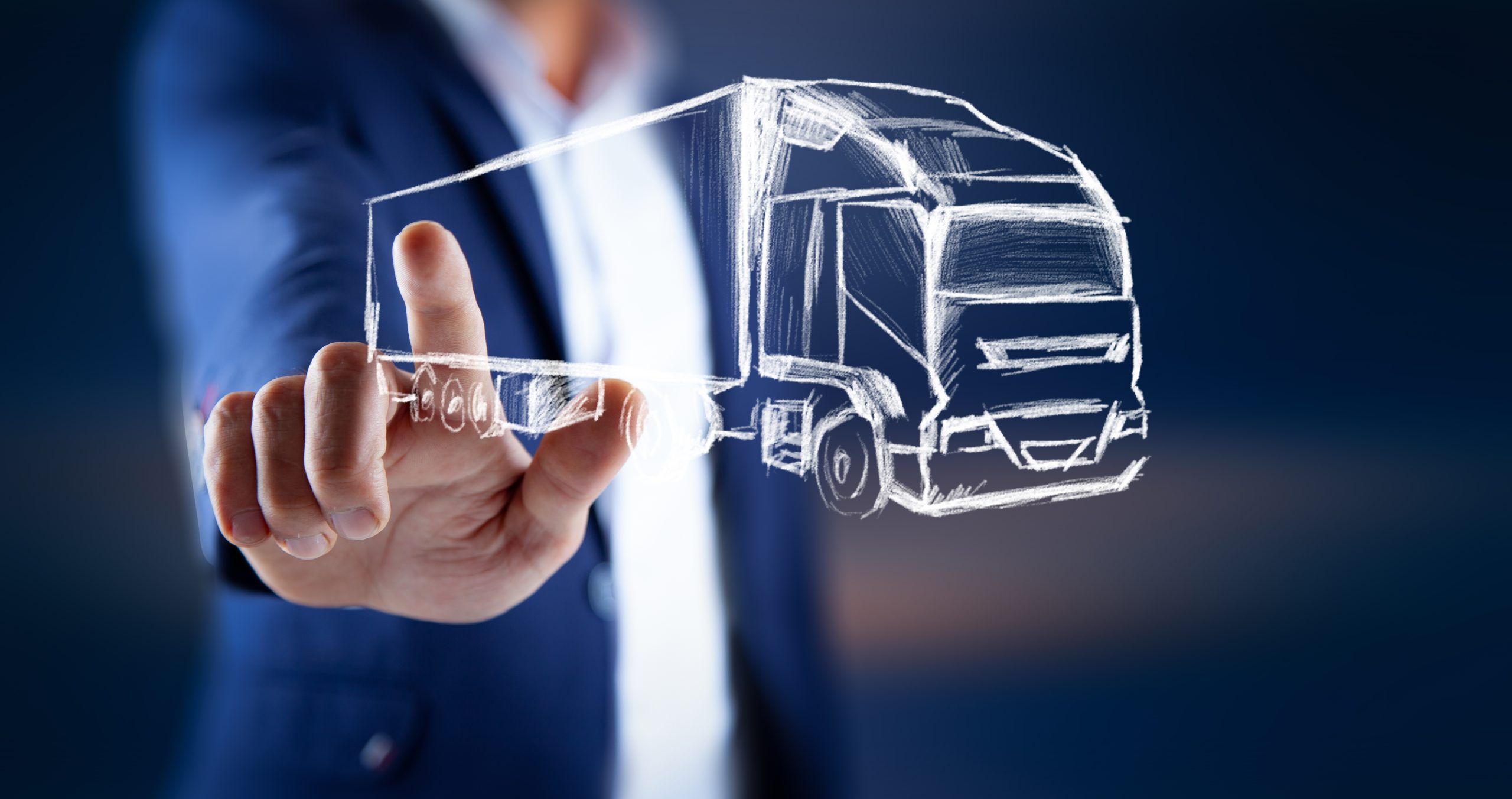
ABM Rinkai TMS delivery route program
FAQ
Will the system help if I have a leased (or mixed) fleet?
Yes, this is one of the best scenarios for using the system because Rinkai selects the most efficient (cost-effective) transport resources to handle all orders. Additionally, ABM TMS allows you to model the financial outcomes of using alternative pricing models involving a leased fleet. Moreover, you will be able to assess what type of vehicles you need and in what proportion.
How reliable is the data protection?
Data protection and liability for unauthorized access are part of our contractual obligations. The only exceptions may be the coordinates/addresses of delivery points and transportation rates. We use modern data centers equipped with a range of software and hardware systems to ensure data security and resilience. Furthermore, our system is regularly tested by experts to safeguard against cyber-attacks.
Can the system be customized for specific client needs?
Yes, it can. The cost of customizations depends on the technical requirements (TR), the number of clients interested in these updates, and the Rinkai system’s development strategy and plans.
What systems does Rinkai integrate with?
Rinkai integrates with any accounting system, SAP, 1C, Navigon, and custom-built systems. Additionally, it integrates with any tracking systems that support APIs or offer database access.
Are there limits on the number of users or warehouses?
No, there aren’t any. Rinkai allows for an unlimited number of users and warehouses, based on client needs. You can also manage access rights by users and work with one or multiple warehouses.
How long does it take to implement the system?
It depends on the quality of the input data and your readiness. The typical implementation timeline ranges from 3 weeks to 3 months.
What maps does the Rinkai system use?
Rinkai is based on OpenStreetMap.
What parameters are considered during planning?
The planning algorithm considers over 15 types of constraints when creating route plans, such as: geographical location of delivery points and warehouses; traffic direction and speed on specific road segments; time windows and other restrictions for orders, delivery points, and warehouses; cost and capabilities of transport vehicles (load capacity, volume, type, availability, speed, etc.); settings in the control panel, including allowances for exceeding certain parameters.
Can client and transport priorities be taken into account?
Yes, for transport vehicles, you can add them in stages during planning, based on priority. The same can be done for orders.
Is there a free trial version or period?
No, there isn’t a free trial period because the system needs to be properly configured to meet user needs before starting work. That’s why we have a separate implementation process. However, you can use the “Comparative Simulation” service. Provide your order data, and our expert will build routes in ABM TMS. Afterward, you can compare your routes with those generated by Rinkai, see the difference, and determine the potential savings in money and resources. You’ll also gain access to the routes in the system and can try working with them on your own.
Is technical support provided?
Yes, and we have a dedicated Customer Success department that not only provides technical support but also conducts a monthly audit of system usage. This means that each month, you’ll receive a report on how effectively you’re using the system and get recommendations on how to further improve your work with Rinkai.
Why choose ABM Rinkai TMS
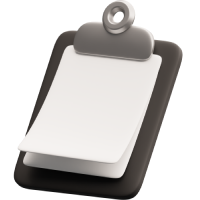
Customer Success
Monthly reports are sent to show how your employees are utilizing our system and provide insights into areas for improvement to enhance efficiency.
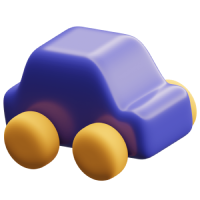
Best Routing Algorithm:
ABM Rinkai TMS utilizes automatic planning and optimization of «last mile» routes that consider time windows, tariffs, road networks, and the number of ramps.
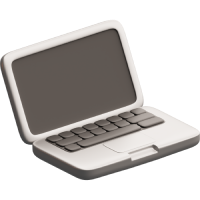
Development and Enhancement:
On average, we perform three system updates per week, introducing new features and improving the overall system functionality.
We appreciate you contacting us. One of our specialists will get back in touch with you soon. Have a great day!