Effects of ABM WMS Implementation
Once implemented, it provides a combination of the right methodology for building business processes and universal automation.


What is the difference between a license buyout and a SaaS format?
License
SaaS
For whom
Features
• Open source code
• The system must be adapted to business processes
• Typical processes
• Fast scalability and high speed of implementation
Server equipment, administration
Technical Support, Software Upgrade, The training in the Academy Ocean system
Implementation period
Price
Whatever the size or industry, we can help
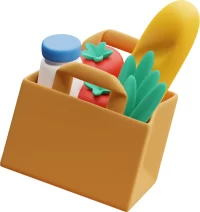
Food & Beverages
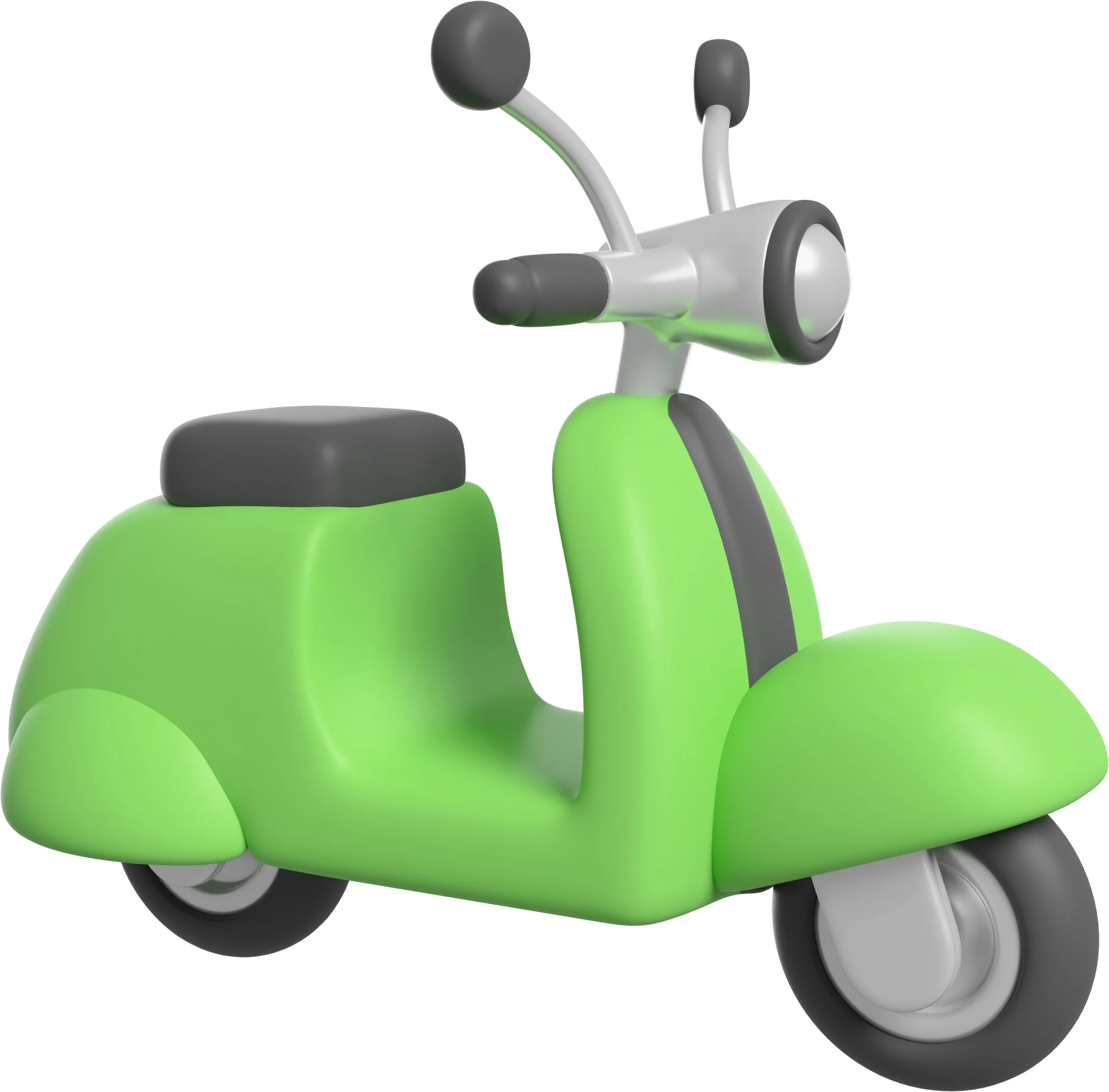
Dark Store
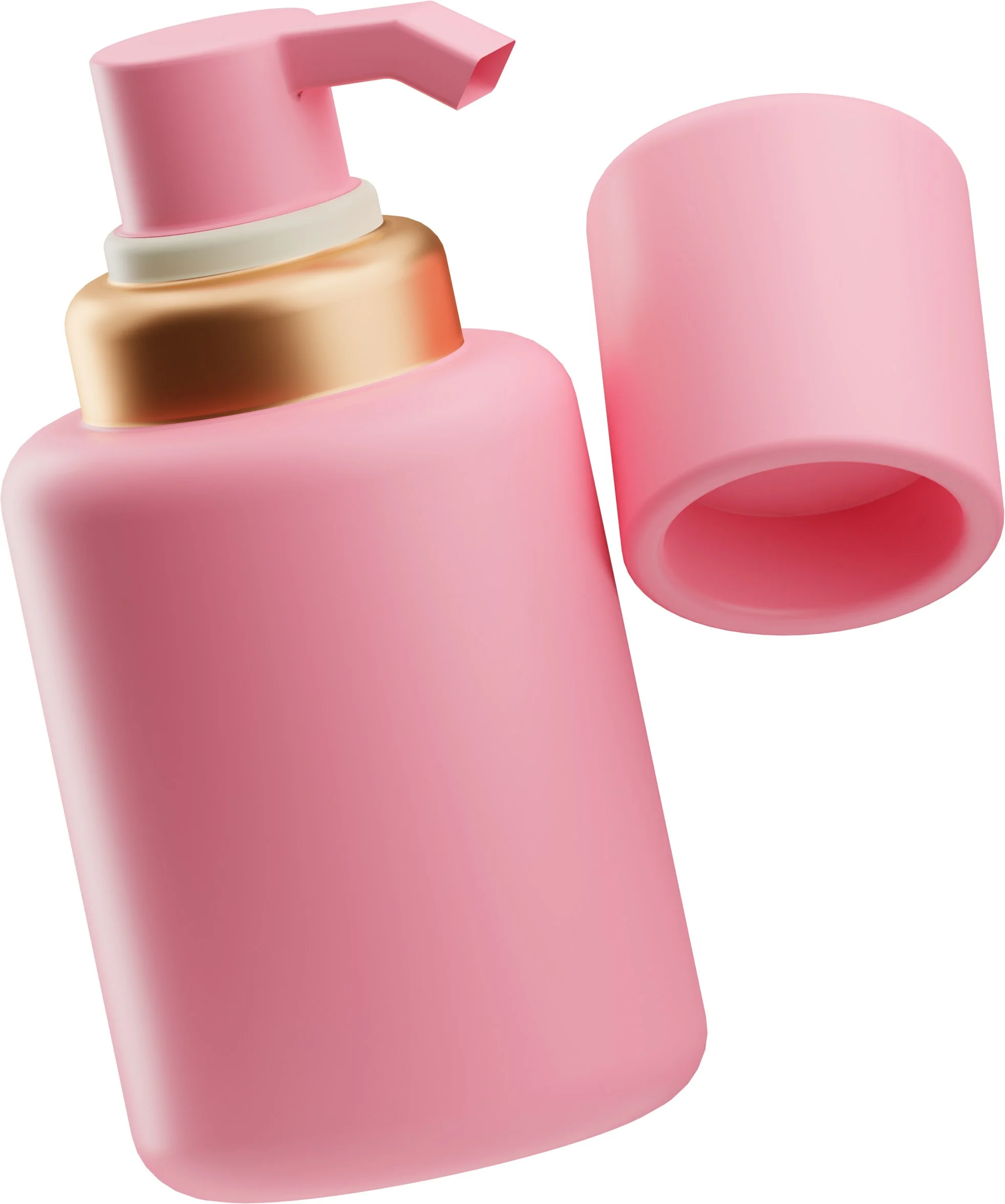
Drogerie
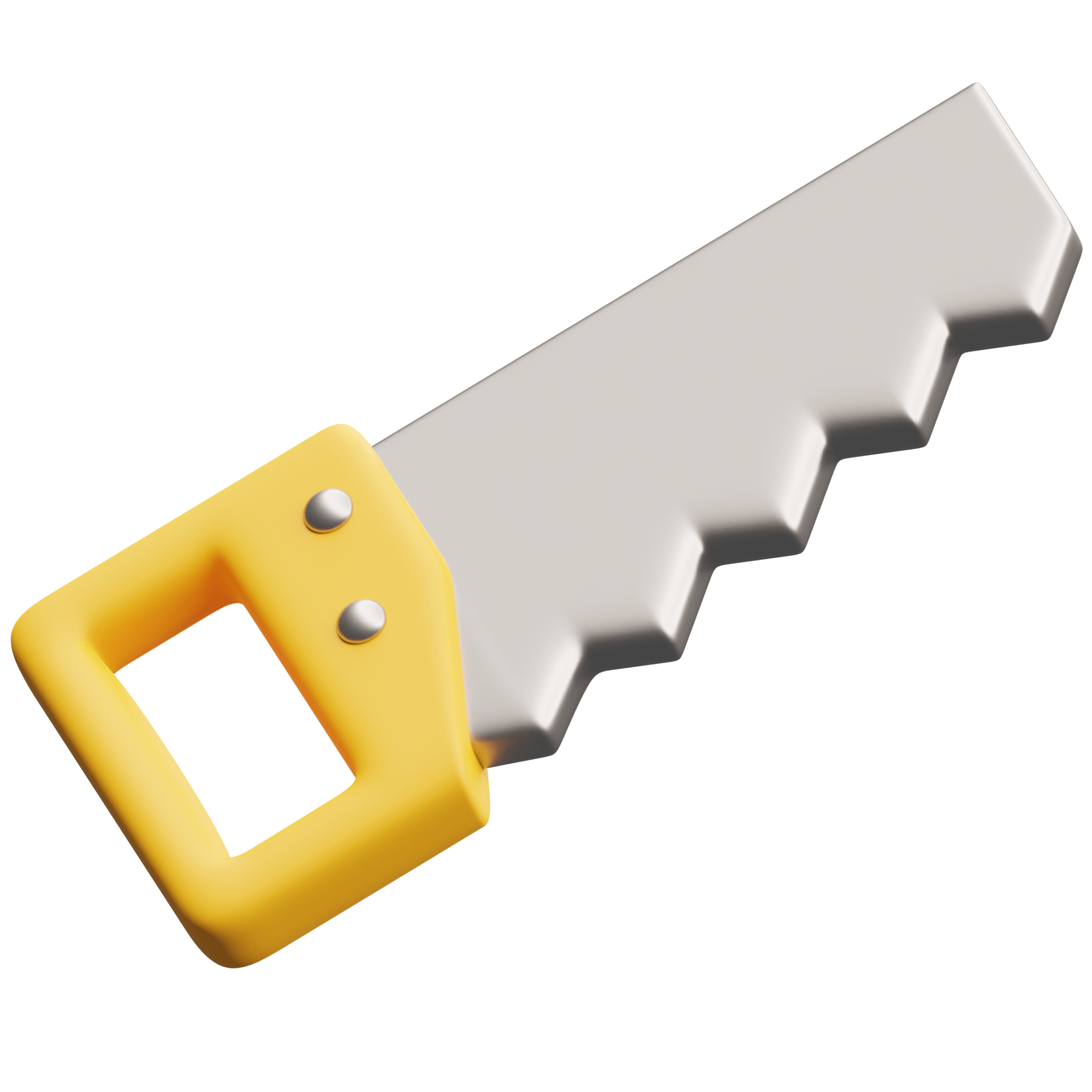
DIY
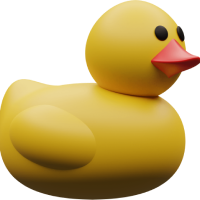
Toy stores
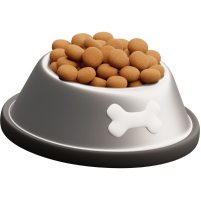
Pet stores
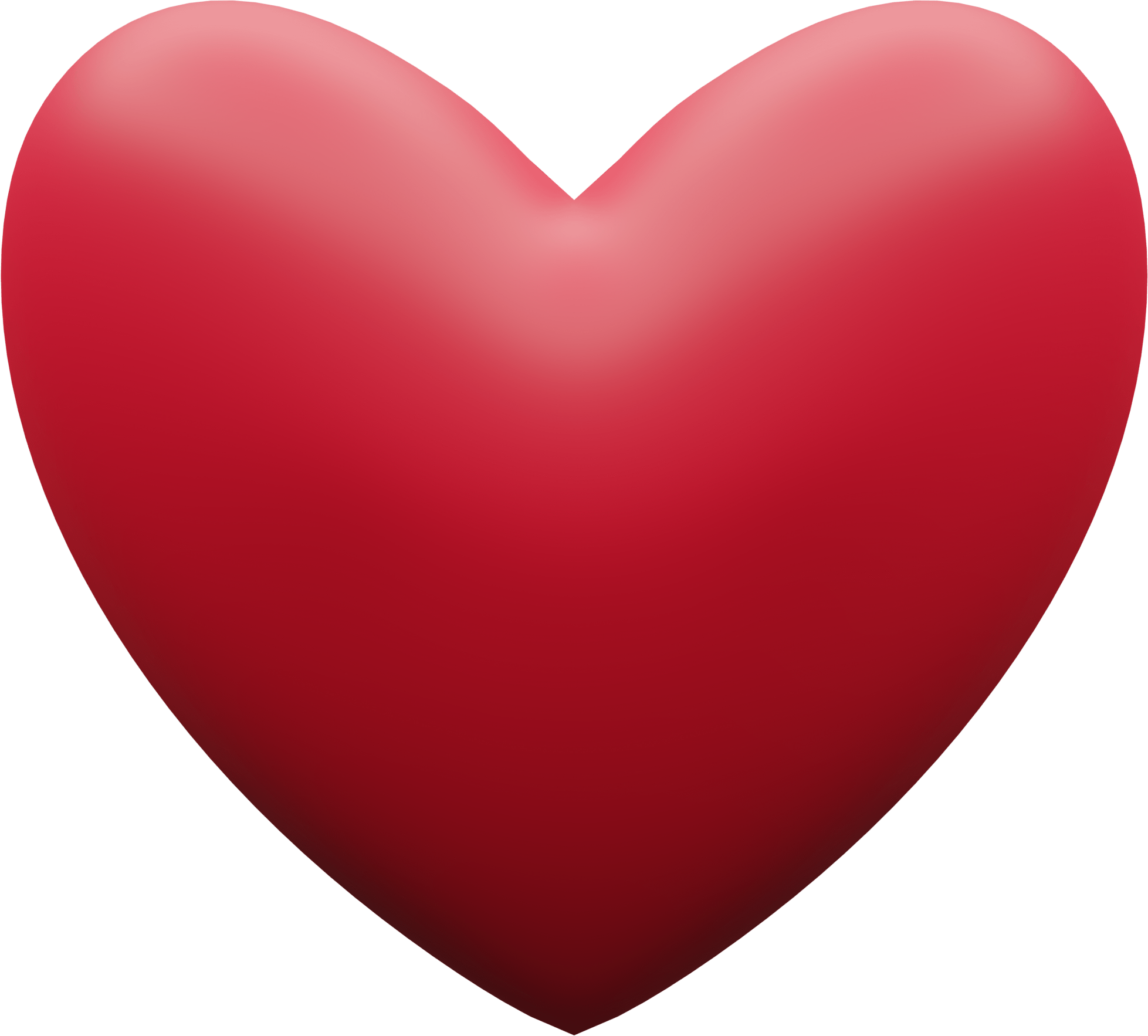
Pharmacies
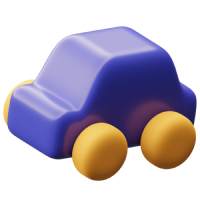
Car parts
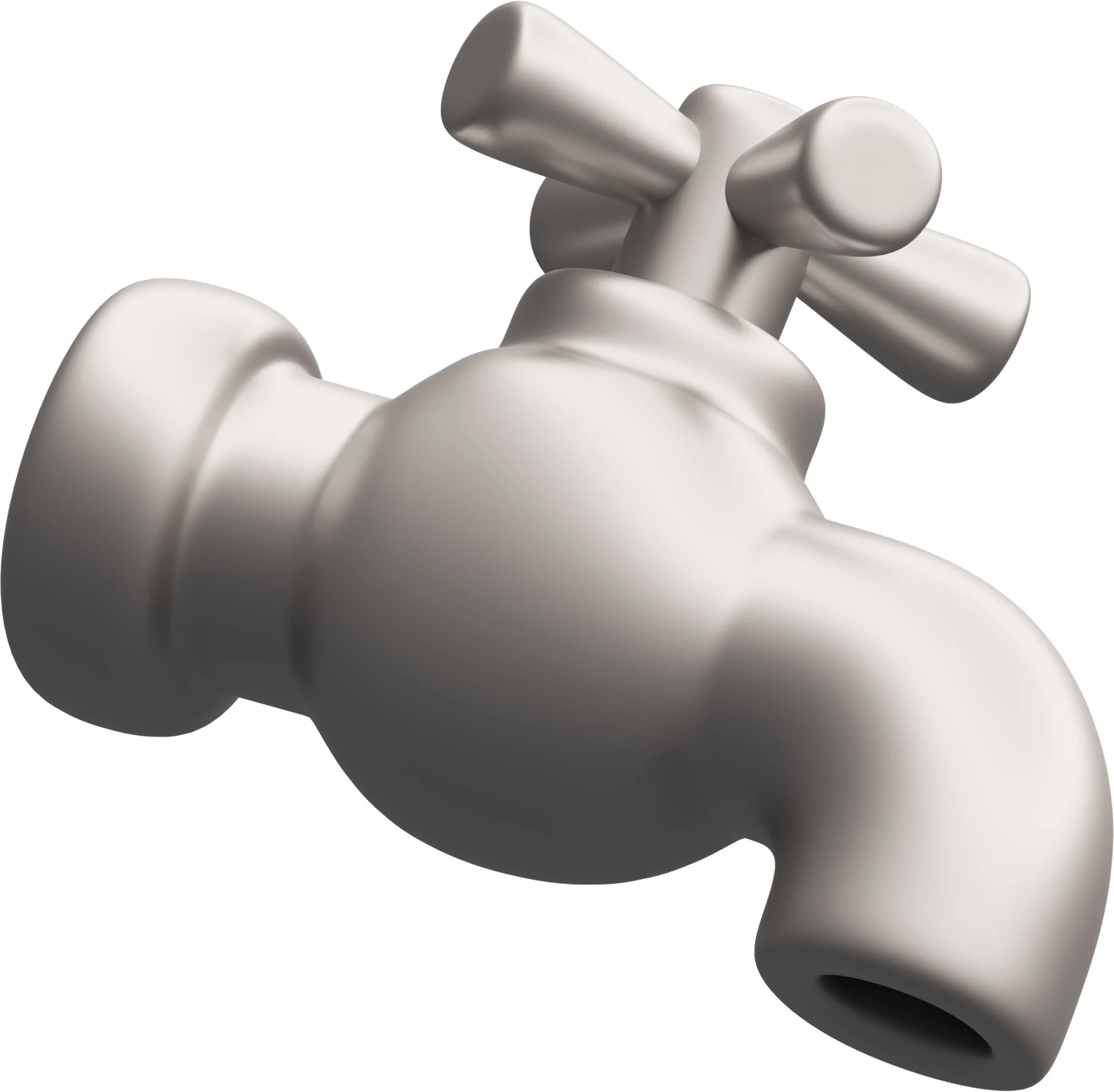
Plumbing
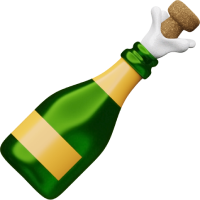
Alkomarkets
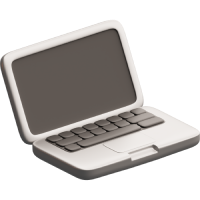
e-Commerce
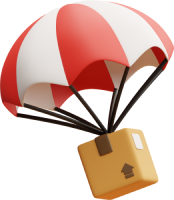
3PL operators
Warehouse management system functions
Selection and shipment
Receiving and storage
Online monitoring of the warehouse situation
Working with DCT
Other program features
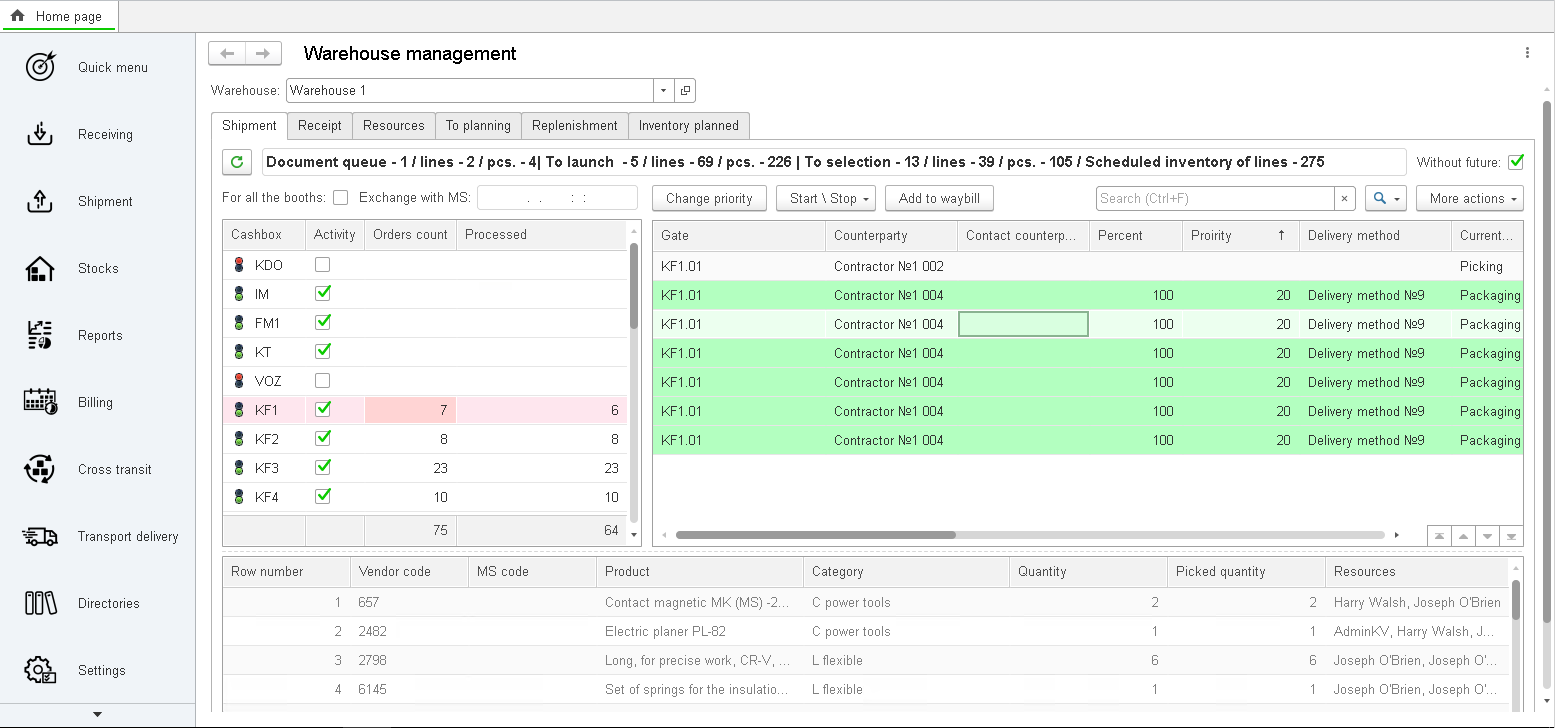
-
Types of selection
Individual, group selection, cluster, zone and wave selection
-
Work with batch accounting
Accounting for batches, expiration dates. Selection by FIFO/LIFO/FEFO. Additional characteristics (for example, color, size, week of production, country, etc.)
-
Control over shipment
Planning of loading time intervals, loading from the vehicle, order of loading orders
-
Additional functions
Printing labels/loads, automatic launch of orders, replenishment, processing of VIP orders, automatic assignment of tasks to pickers, notification of the availability of tasks
-
Handling of problem situations
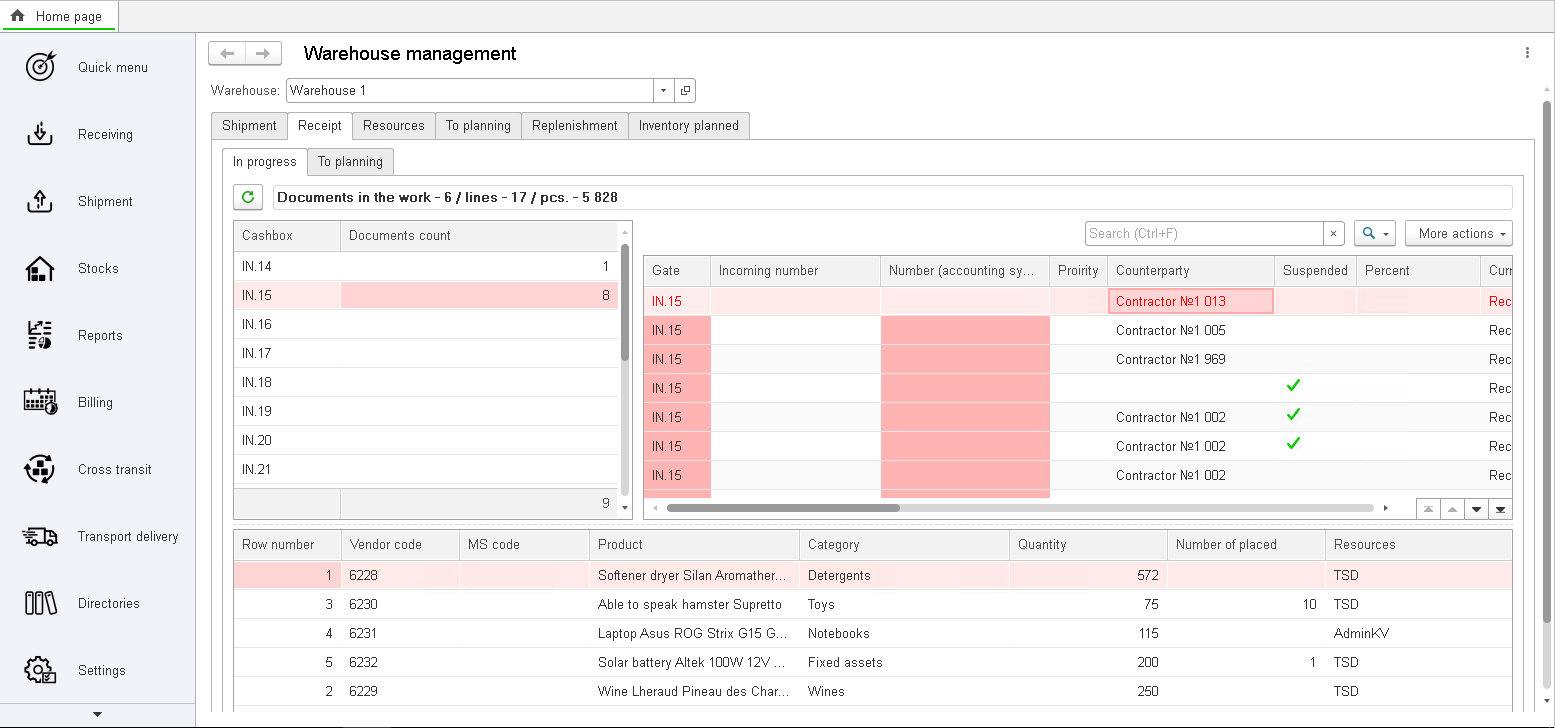
-
Online quantity and quality control
Acceptance of goods via DCT or PC, selection of batches, expiration dates and characteristics/properties of goods, batch statuses, weight control
-
Repacking, labeling and palletizing
Specifying the packaging of goods, sending for labeling and repackaging, accepting goods into containers, accepting oversized cargo
-
Cross-docking
Classic cross-docking, pick-by-line with static and dynamic cell binding, combined (pick-by-line + picking from the warehouse)
-
Organization of any technologies and types of storage
Packed racks, integration with conveyors, integration with scales at the receiving end
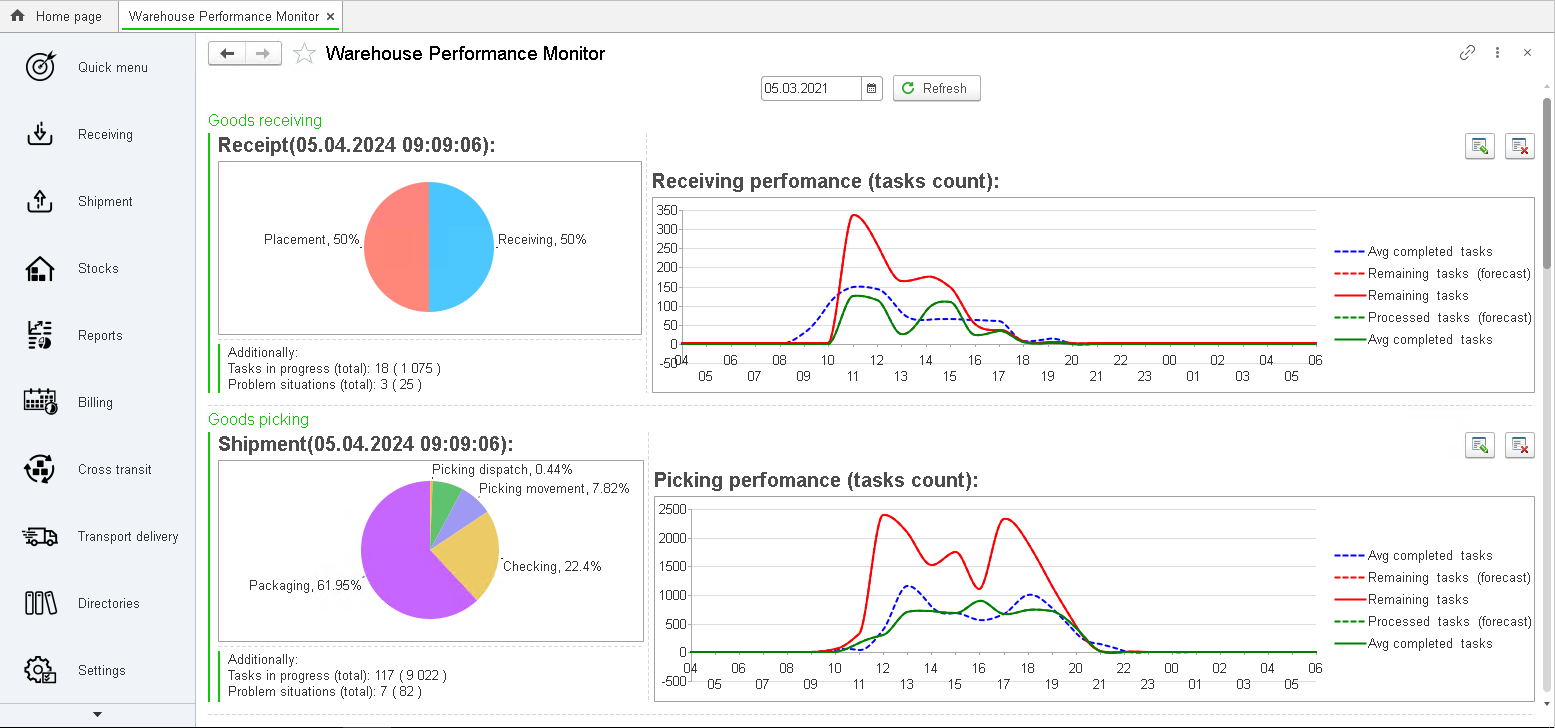
-
Customizable basic reports with the ability to build by various parameters
Stock balances, active warehouse tasks, document processing reports, inventory results
-
Online performance analytics
ABC – analysis, warehouse utilization analysis, cargo flow analysis, operations billing, control of goods without movement
-
Monitoring
For managing warehouses, route sheets, documents and processes (receipt, shipment, replenishment, movement, inventory, return)
-
Dashboards for top managers
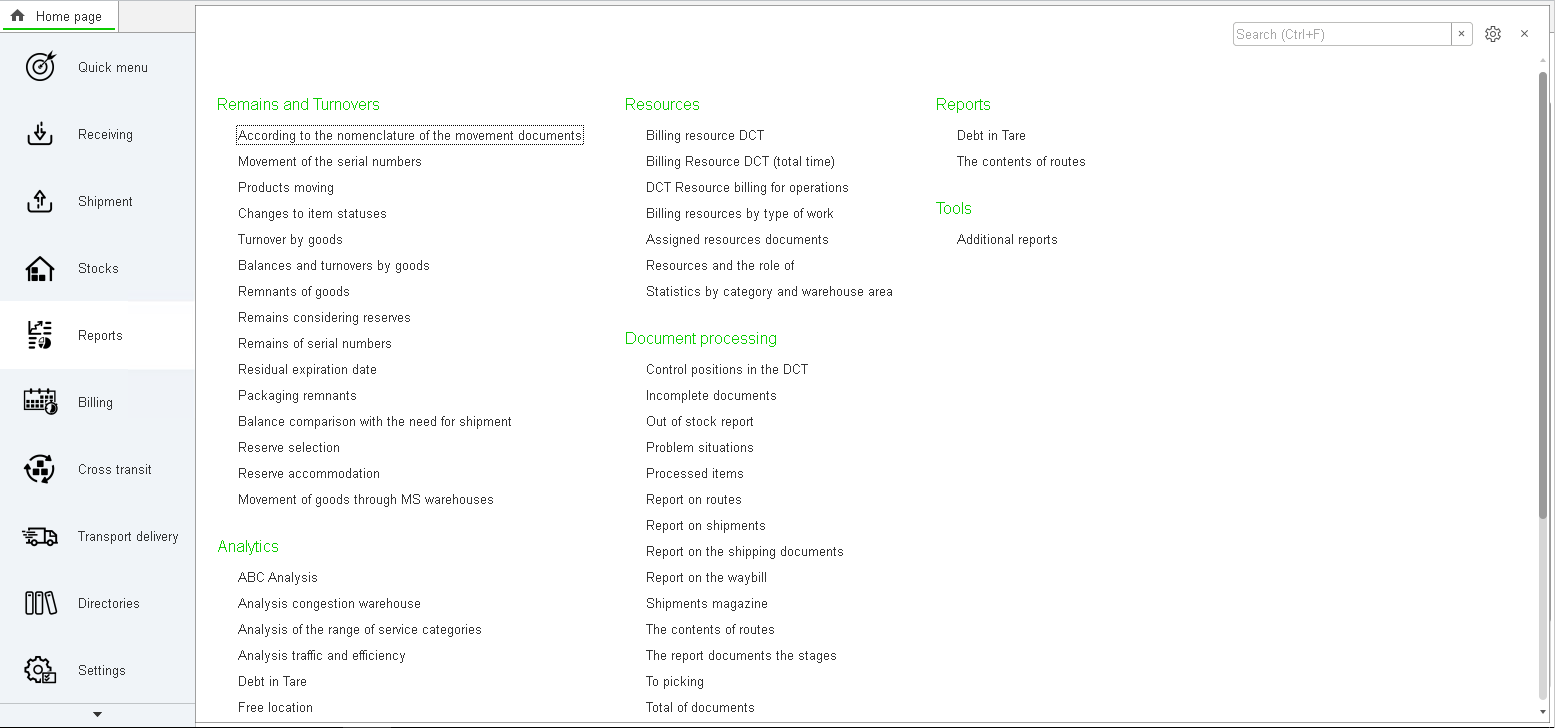
-
Management of resources and access rights (roles)
Monitoring of resources, billing of operations, processing for quick change of resource roles
-
Container casing
Acceptance and shipment of containers, inventory, debt control
-
Additional work
Assistance with selection, cleaning, pallet loading/unloading, packing, etc.
-
Integration with equipment
System integration with scales, conveyor lines, sorters, elevators, industrial robots, etc.
-
3PL
Safekeeping services (for operations, storage, etc.), tariff scale and registration of services
Stages of WMS system implementation
• Preparation and approval of the design project. Approval of "as is" and "to be" blocks
• Adaptation of WMS according to the approved terms of reference (duration of the stage depends on the client’s requirements)
• Development of testing scenarios
• Complex testing
• Deployment of WMS on the client’s base
• Loading of initial data (balances, constants, service directories)
• Training at the client’s warehouse
• Reconciliation of balances with ERP system
• System commissioning
• standard during business hours
• extended 24/7
• Customer Success
01 Analysis and preparation of the design project
02 Start-up and adjustment works
03 Training
04 Project launch
05 Support
Average stage durationㅤ ㅤㅤ ㅤ ㅤㅤ20-30 days
• Preparation and approval of the design project. Approval of "as is" and "to be" blocks
Average stage durationㅤㅤㅤ ㅤㅤㅤ ㅤ 25-45 days
• Adaptation of WMS according to the approved terms of reference (duration of the stage depends on the client’s requirements)
• Development of testing scenarios
• Complex testing
• Deployment of WMS on the client’s base
• Loading of initial data (balances, constants, service directories)
Average stage duration ㅤㅤ ㅤㅤㅤ ㅤㅤ5-10 days
• Training at the client’s warehouse
Average stage duration ㅤㅤ ㅤㅤㅤ ㅤㅤ5-15 days
• Reconciliation of balances with ERP system
• System commissioning
Average stage duration ㅤㅤㅤ ㅤㅤ ㅤㅤ7-14 days
Further support
• standard during business hours
• extended 24/7
• Customer Success
ABM WMS Pricing
Warehouse size, number of cells, and technological zones
These are important for determining the scope of work for process automation and system configuration.
Number of SKUs in the catalog
This includes the total number, inventory, and active SKUs, which influence the structure and functionality of the system.
Type and quantity of equipment
This includes data collection terminals (DCTs), barcode printers, conveyor lines, scales, sorters, cubiscans, and others.
Document flow in the warehouse
The number of documents and operations, considering seasonality, which affects the configuration of processing workflows.
Number of users and operational mode
Planning for staff training, the number of workstations licenses, and the level of support.
Additional specific process settings
Custom configurations tailored to your business needs, which can influence the overall WMS price. If you want to buy a WMS system, it’s essential to consider these factors for an accurate cost assessment.
Our goal is the result of your business
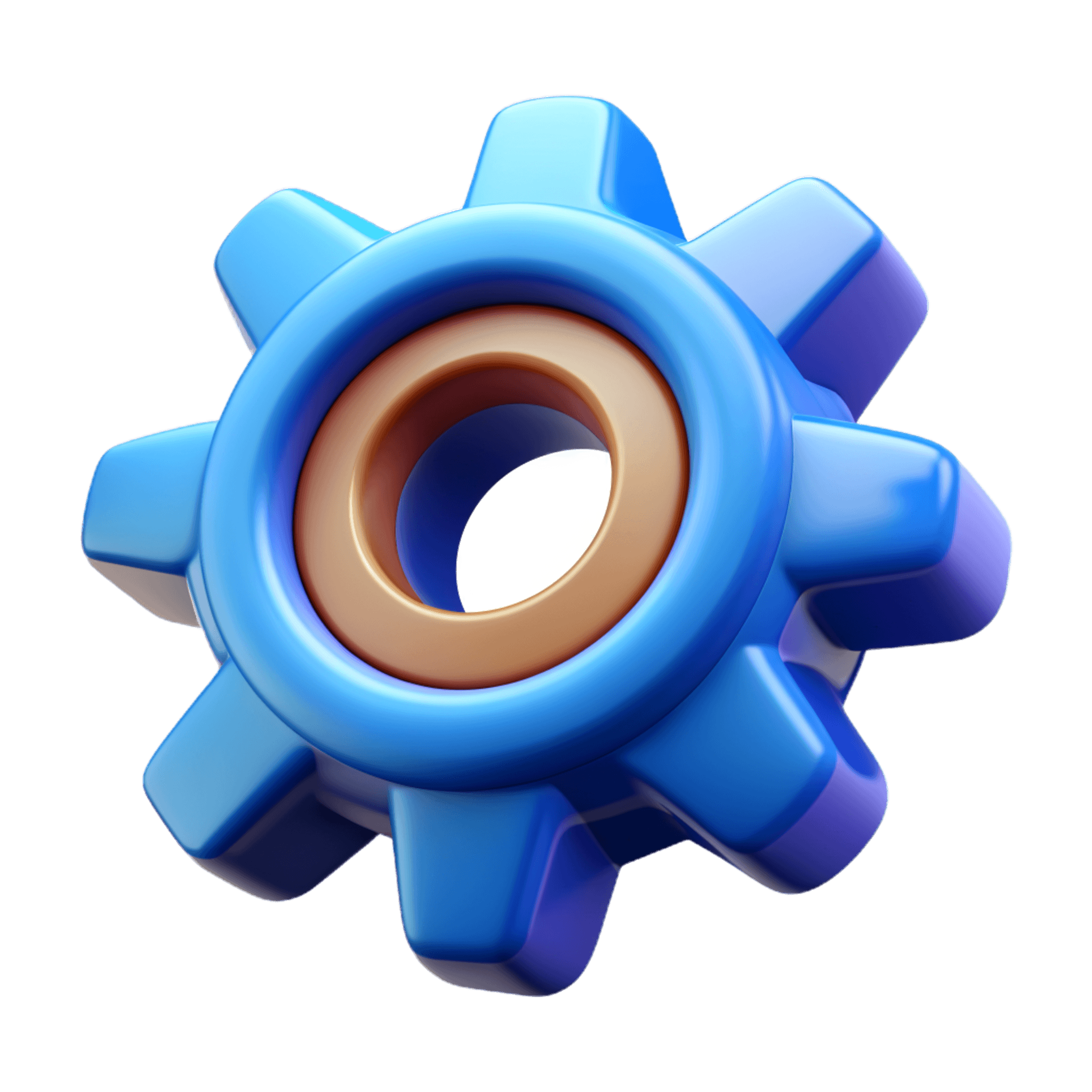
Integration
ABM WMS integrates with accounting systems, supply chain management solutions, robotics, conveyor systems, elevators, etc.
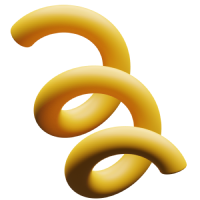
Flexibility and scalability
ABM WMS implementation helps businesses to quickly adapt to changes in market demand and scale business processes, in case of changes or business expansion

Loyalty
The use of the system ensures improved quality and speed of order fulfillment, which contributes to better relations with customers and suppliers
We appreciate you contacting us. One of our specialists will get back in touch with you soon. Have a great day!
FAQ
What is the cost of implementing a WMS system?
In general, there is no fixed cost for implementation projects. It varies depending on the scale of the business and its type in general, the company’s industry, functionality requirements, volume of operations and necessary integrations, number of threads, users, system load, need for customization, and other factors.
The cost itself consists of three main blocks:
- software
- implementation work, including the formation of a design project, adaptation of the system to the business, training, and launch;
- post-implementation support.
In addition, additional costs associated with automation should be taken into account, such as seamless Wi-Fi, the cost of preparing exchanges from the ERP side, data collection terminals and label printers.
How is the project implementation time determined?
The project implementation time is determined individually for each customer and depends on the number of processes to be implemented and the complexity of these processes.
A vendor can provide a preliminary estimate of the project duration after filling out questionnaires on the facility and discussing the processes during meetings.
The exact timeframe is provided based on the results of the survey and the formation of the implementation design project (as a rule, this is included in the first stage of implementation work), after assessing all the customer’s business units and the scope of work.
On average, a WMS implementation project lasts 3-4 months.
What is the documentation of the work?
Documents that are generated within the project:
- project charter;
- protocols on the results of work for the week;
- recommendations for equipment;
- recommendations for servers;
- API.
Protocol on the completion of work. We write instructions for the finalized functionality and give recommendations for equipment and servers.
How is support provided after implementation?
At the end of the implementation, the implementation team, which was directly involved in the launch and was at the site for 2 weeks, provides full support.
After this period, if a support agreement is concluded, the implementation team introduces the client to the technical support department.
Each client has their own account where they can leave requests with questions/tasks.
- As part of the support:
we provide consultations on how to work with the system, set up and launch additional functionality, perform program modifications of any complexity, etc; - upon request, access to the WMS training platform (for different roles) can be provided through the account;
- The customer has access to system releases as they are implemented.
Integration with systems
ABM WMS integrates with virtually all ERP systems, including SAP, 1C, BAS ERP, Oracle, Odoo, s Visma, Oracle, Microsoft Dynamics NAV and AX, and others. Thus, data on products, orders, order status, inventory, etc. can be shared across different systems.
In addition, if necessary, the system can be integrated with both an online store order acceptance system and various types of OMS (Order Management System).
It is also possible to integrate WMS with TMS (Transport Management System).
What else will be needed besides the system itself, and what equipment can it be integrated with?
The main equipment that ensures that warehouse employees perform operations is:
- data collection terminals (DCS) or 2D barcode scanners,
- label printers,
- conventional printers (when the selection of goods and materials is carried out according to a list, without the use of DCS),
- water measuring equipment.
WMS IT infrastructure equipment:
- database server and applications,
- operator workstations (PCs),
- network infrastructure and Wi-Fi devices.
As for integration, it can take place both directly with water measuring equipment, cubicles, applicators, and with shuttles, with conveyor lines with logic of various types, and even robots.
How does warehouse automation work begin?
Our work begins with analyzing the customer’s questionnaire, the specifics of the warehouse processes, and its topology. Next, we meet the customer’s project team, define roles in the project, the main project communication channels, and areas of responsibility.
The next step is a warehouse survey with the digitization of current processes, communication with users of the WMS system, and performers of each task in the warehouse. The next steps are to prepare and build the most effective business processes in the warehouse (as agreed with the Customer), taking into account the expansion of opportunities through the WMS system, preparation of analytics, and the start of implementation work.