Project prerequisites
Manual routing was used. Optimization of existing routes or construction of new routes took 7 to 30 days of logistician's work.
There was no possibility to analyze correctness of time windows of delivery to TT (quantity, quality of deviations in retrospect).
It was not possible to take into account the shipment history (time of movement along the route, time for unloading at the TT) for operational adjustment of routes.
The analytics on route reanatability were prepared manually after the reporting period was closed. Accordingly, it was impossible to react and make adjustments to the logistics process in a timely manner, which led to overspending.

Manual entry of data into the database, as a result of possible errors of logisticians, incorrect data of TT placement, under-delivery.

Lack of ability to quickly adapt drivers, as a result, when changing the TT, route or driver - under-deliveries, delays.
Lack of online ability to track driver's TT attendance, delays, tardiness, deviations from the route.
Project goals
Stages of work
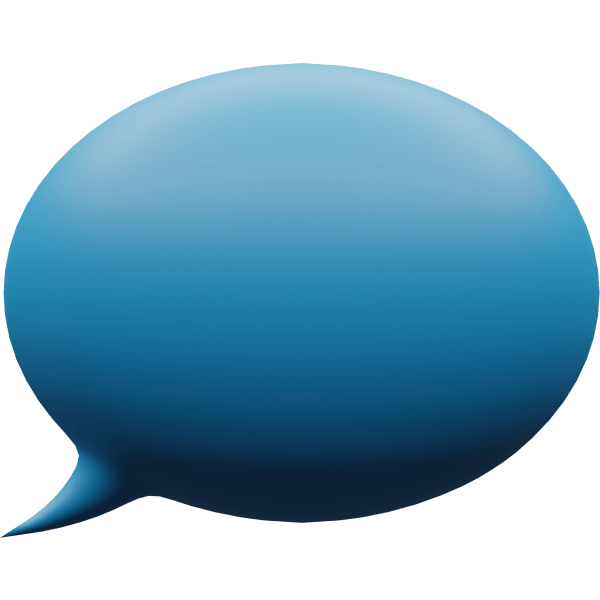
Preparatory stage
Based on the results of the questionnaire survey of the heads of transportation and warehouse, commercial and IT departments, as well as the company's management, all business processes affecting the implementation of TMS were analyzed and recommendations for their improvement were given. The goals of TMS implementation and the changes required to achieve the results were defined. Work plan, deadlines, responsible persons, implementation control, list of risks for the project and specific steps to minimize them were agreed upon.
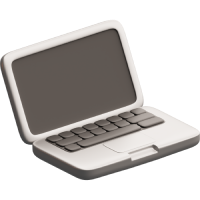
System setup
We implemented data exchanges between the accounting system and TMS (ordering, vehicle availability, route plans), the movement control system and TMS (route fulfillment control). We also developed a separate analytical block for quick access to all possible indicators (overruns, costs, quality of service, etc.).
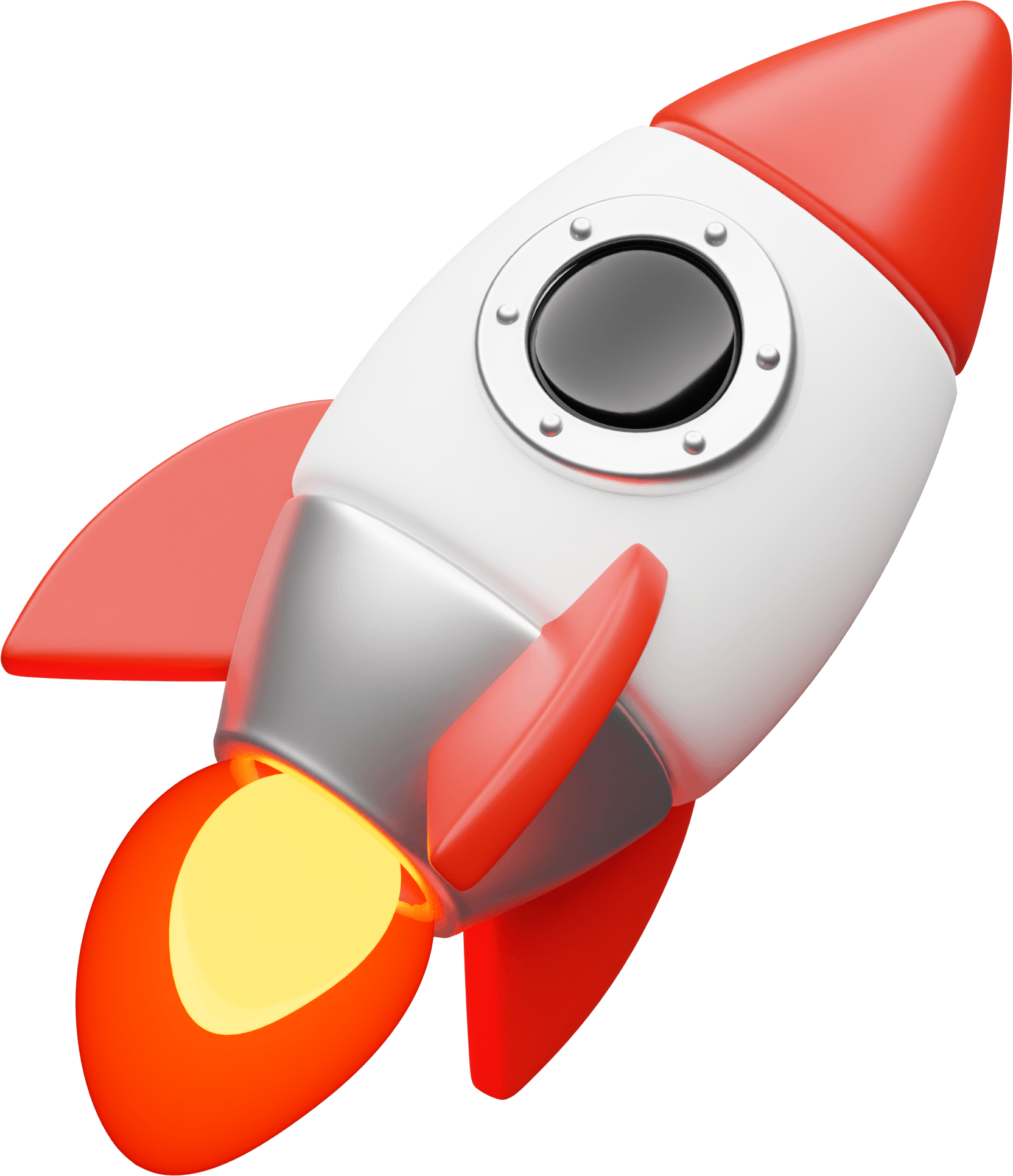
The launch of the first factory
We reproduced routes in TMS for the previous period to set up primary indicators. We conducted staff training and provided support in initial planning. We performed plan-versus-actual analysis of route execution and adjusted indicators accordingly.
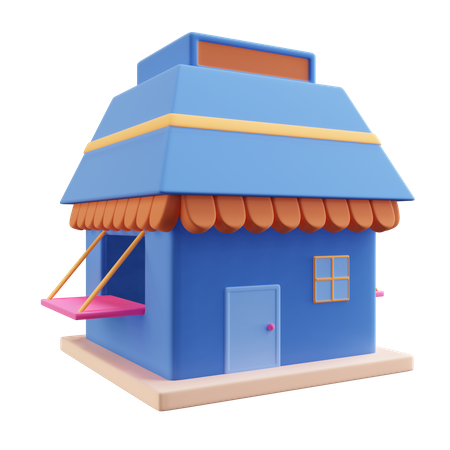
Scaling up
Scaling up TMS to include 2 additional plants (Lviv and Vinnytsia) and cross-docks.
Project progress
Creating user accounts and granting system access with various permissions.
Generating routes for the previous period to accurately adjust the system: temporal characteristics of unloading one kilogram of product, speed characteristics of trade points, and drivers.
Each trade point has individual characteristics that affect unloading speed; each vehicle also has additional characteristics for loading and travel speed.
Training all users, particularly logistics/dispatchers, on system operation, plan-versus-actual analysis, and reporting.
Providing assistance and support in building the initial routes.
Launching approximately 80 vehicles at a single plant in Lviv with static routing, with the option for partial and full transition to dynamic route planning.
Consultations on system operation, debugging of business processes.
Handover of the project to technical support.
The implementation of ABM Rinkai TMS for Khlibprom

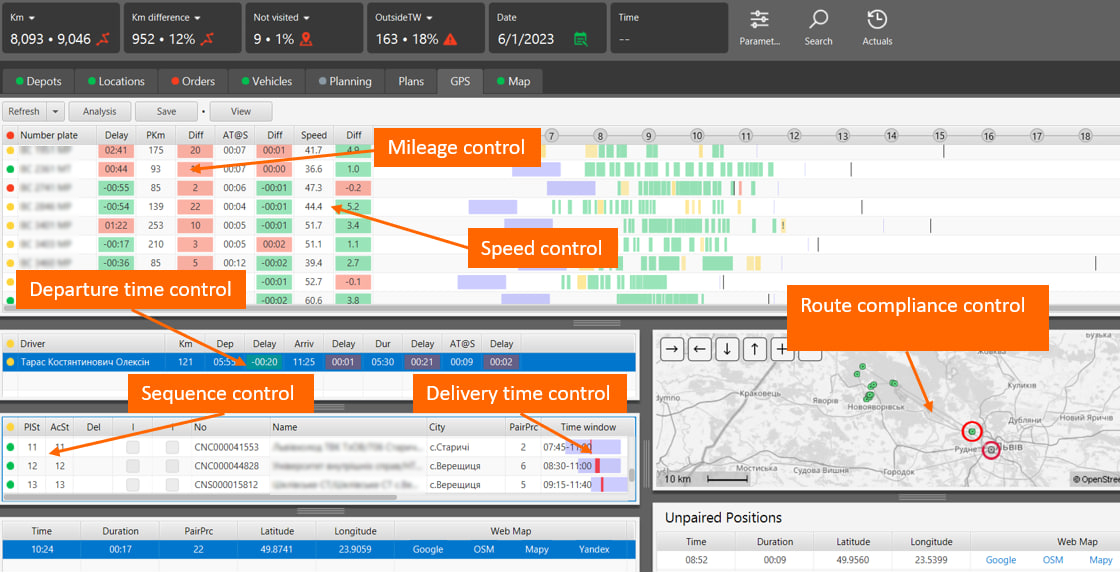
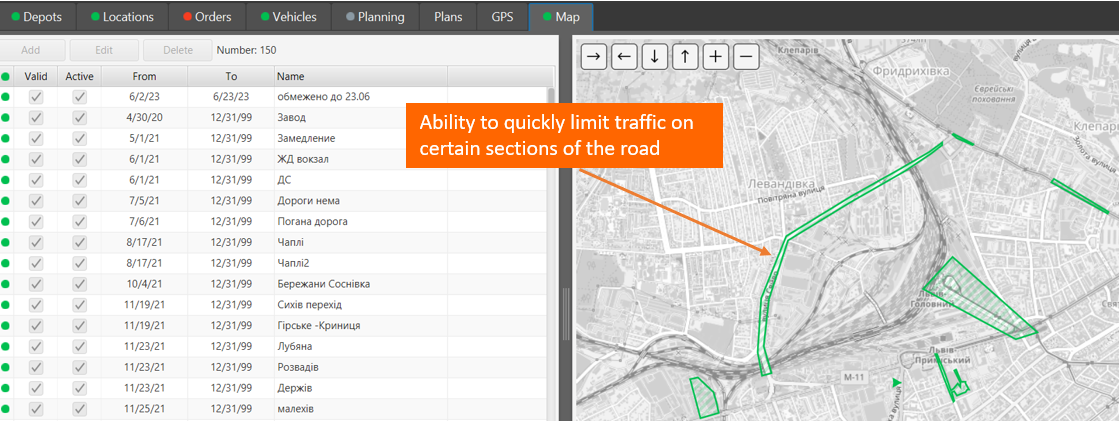
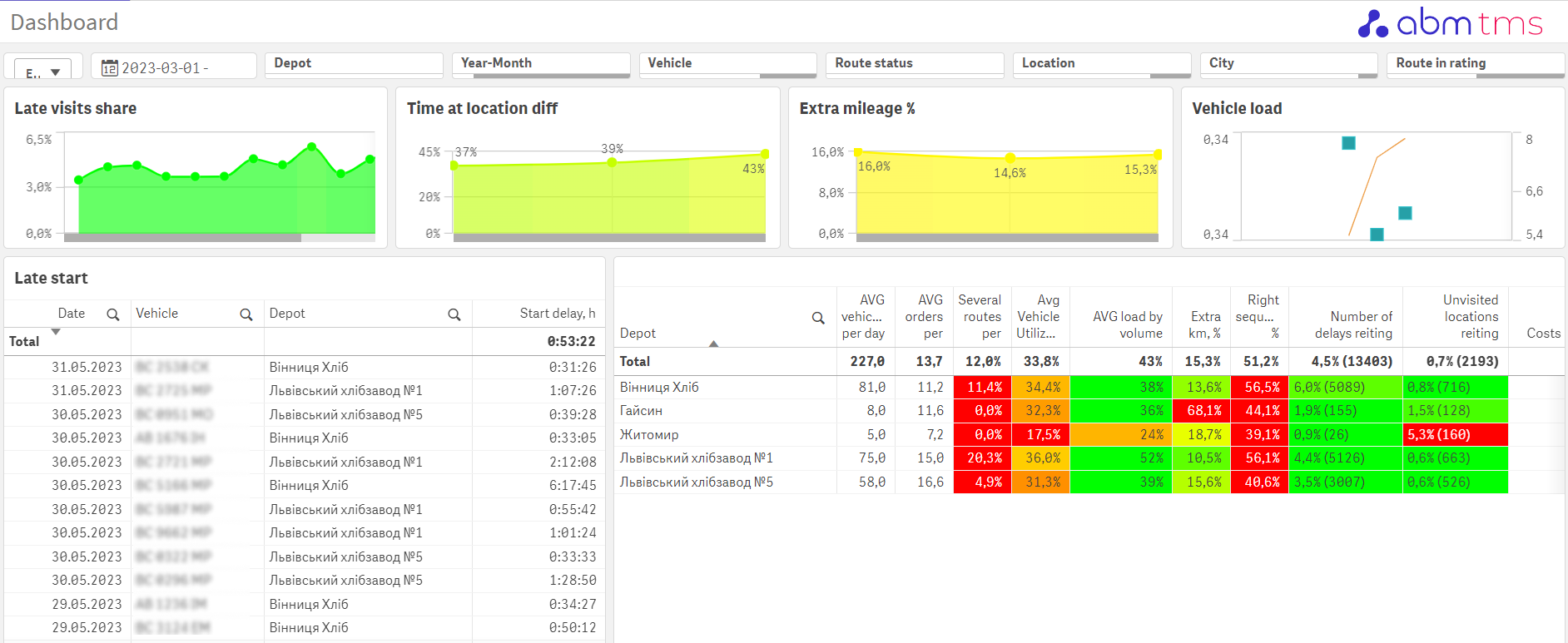
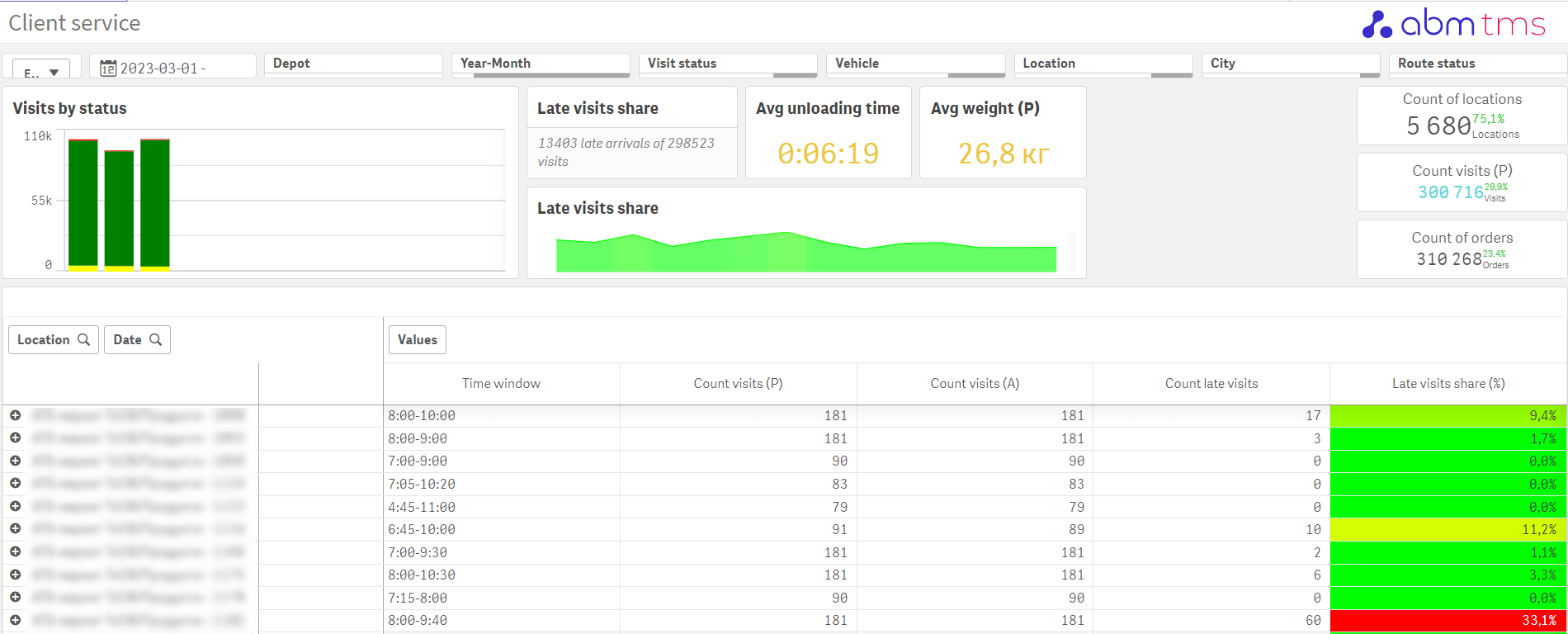
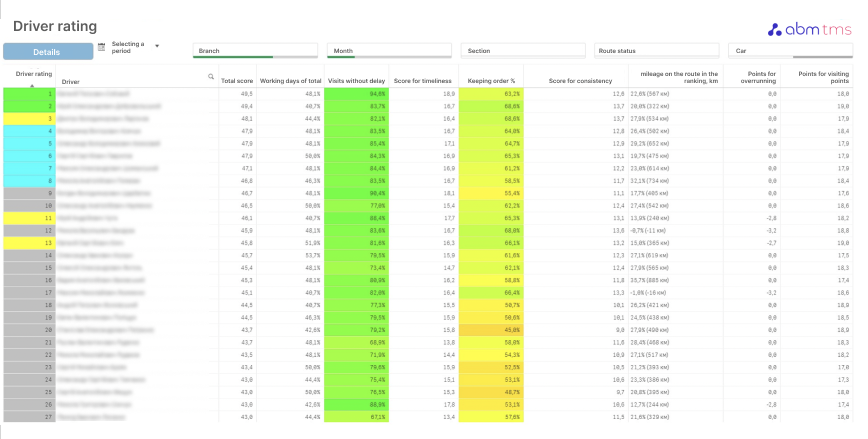
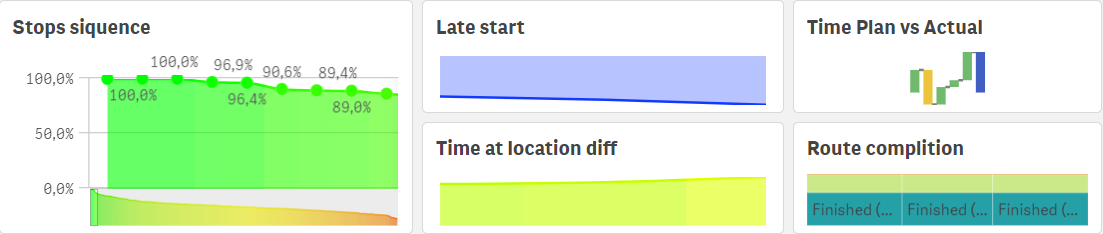

The results of implementing ABM Rinkai TMS at the first plant
Khlibprom is the first company in Ukraine's bread industry to utilize dynamic delivery route planning
At the pilot plant, when comparing indicators for July 2021 and February 2023:
Quality indicators:
-
Fully automated the route planning process and minimized the human factor, resulting in improved quality, speed, and accuracy of route planning.
-
Optimized the utilization of vehicles and significantly reduced transportation costs.
-
Increased the level of customer service through the implementation of delivery time notifications and the use of waybill data.
-
Enhanced the efficiency of monitoring on-time product delivery to customers.
-
Automated the process of monitoring deviations from the route, significantly reducing mileage deviations beyond planned routes.
-
Created reliable reporting based on GPS-generated actual data, updated daily.
-
Implemented an analytics module.
The results of implementing ABM Rinkai TMS at the second plant
At the second plant, comparing December 2021 to February 2023:
Quality indicators:
-
Fully automated the route planning process and minimized the human factor, resulting in improved quality, speed, and accuracy of route planning.
-
Optimized the utilization of vehicles and significantly reduced transportation costs.
-
Increased the level of customer service through the implementation of delivery time notifications and the use of waybill data.
-
Enhanced the efficiency of monitoring on-time product delivery to customers.
-
Automated the process of monitoring deviations from the route, significantly reducing mileage deviations beyond planned routes.
-
Created reliable reporting based on GPS-generated actual data, updated daily.
-
Implemented an analytics module.
The results of implementing ABM Rinkai TMS at the third plant
At the third plant, comparing May 2022 to February 2023:
Quality indicators:
-
Fully automated the route planning process and minimized the human factor, resulting in improved quality, speed, and accuracy of route planning.
-
Optimized the utilization of vehicles and significantly reduced transportation costs.
-
Increased the level of customer service through the implementation of delivery time notifications and the use of waybill data.
-
Enhanced the efficiency of monitoring on-time product delivery to customers.
-
Automated the process of monitoring deviations from the route, significantly reducing mileage deviations beyond planned routes.
-
Created reliable reporting based on GPS-generated actual data, updated daily.
-
Implemented an analytics module.
Customer review
We appreciate that you are interested in our products. One of our staff will be in touch with you shortly. Have a great day!