Qualiko's entry into the UAE market
Prior to the implementation of the system, Qualiko had been operating in the UAE market for only 6 months and faced typical problems of newcomers - lack of customers and sales outlets.
Hired warehouses and signed an agreement with a carrier for several cars
Their number grew steadily in proportion to the increase in sales.
The company chose the Van Selling strategy to find customers
The trucks essentially operated as a mobile warehouse, and the purchase of products was offered directly to stores and restaurants from the trucks. After this first sale, the outlets were offered to sign an agreement on regular deliveries. Thanks to this model, the volume of deliveries grew by 70-100% every month over the course of a year.
In the first months, deliveries to the Qualiko branch were made by air, and as the number of orders increased, they switched to truck delivery
Project goals
Project stages

Integration of ABM Rinkai TMS functionality
Routes for the products were planned, taking into account the temperature regime of each product. We also took into account the specifics of the fleet, which includes vehicles from 3 tons to 20 tons.
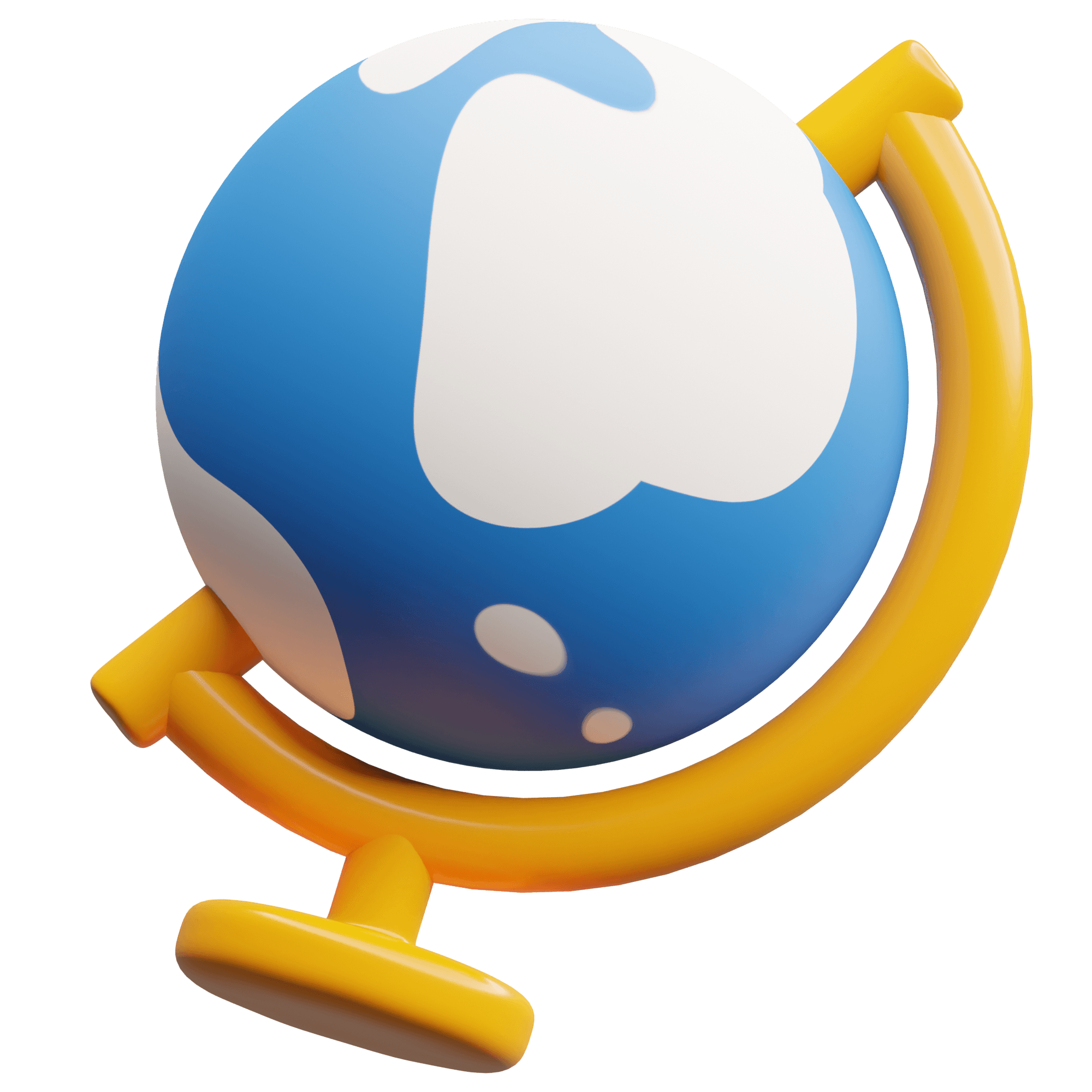
Finalizing maps
We adapted the map display to English. At launch, the system showed the map to the driver only in the local language. This led to significant problems when searching for an unloading point, because due to the specifics of the UAE carrier market, most drivers do not speak Arabic.
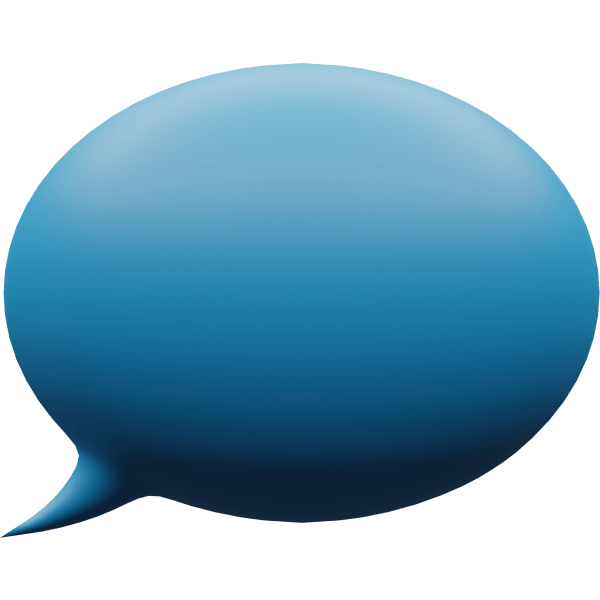
Work with employees
We worked with the branch's employees and updated the restrictions on the entry of trucks into a particular emirate. Based on this, ABM Rinkai TMS automatically created routes and assigned drivers to delivery destinations.
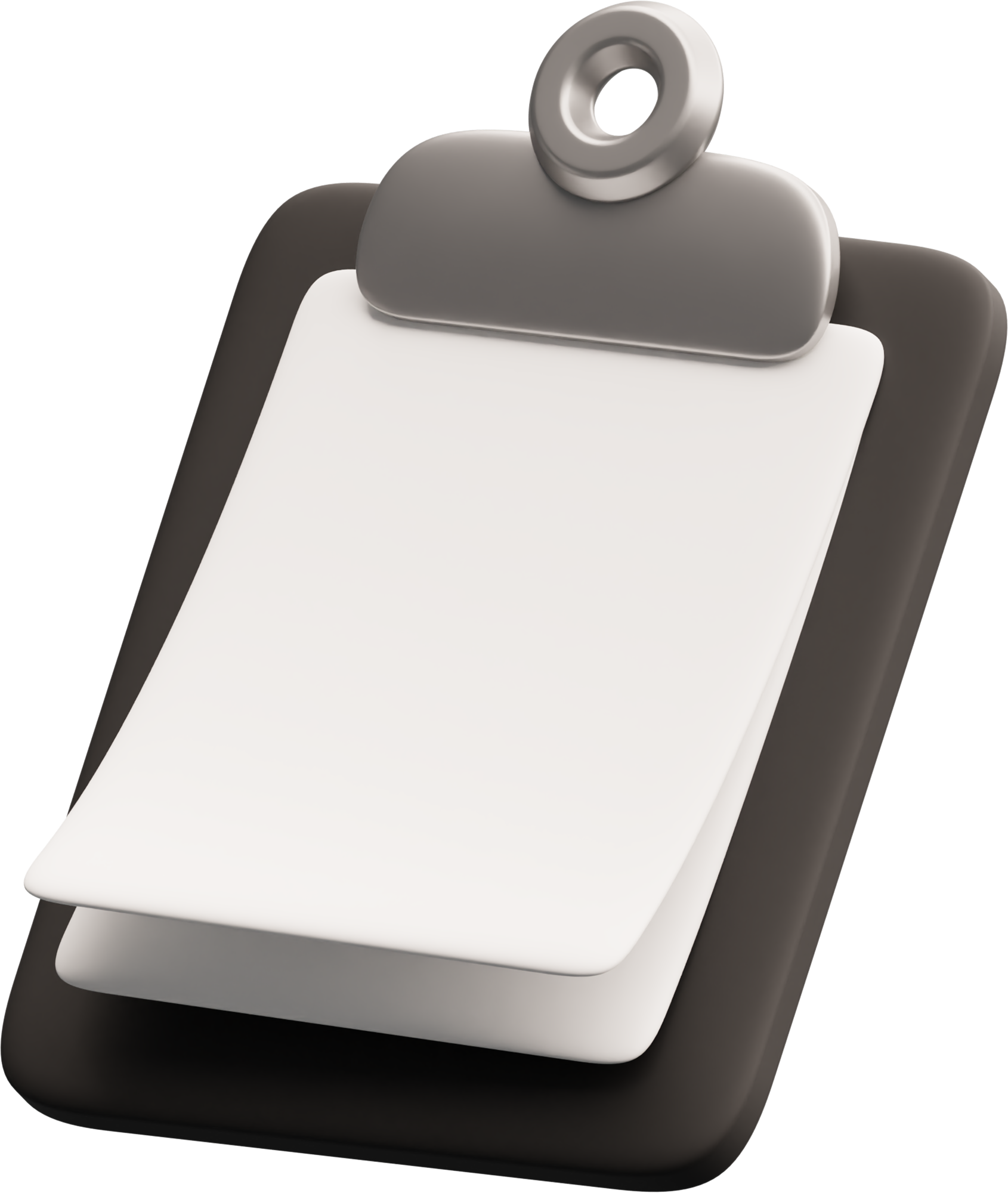
Data reconciliation
The geographical coordinates of the points have been adjusted so that the routes loaded into the application lead the driver not only to the desired building, but also directly to the ramp.
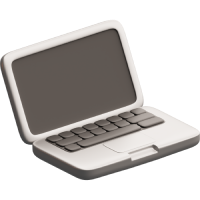
Analytics settings
During the project, more than 20 new schedules and 17 parameters were set up to effectively achieve the project goals, including driver and department-wide evaluation metrics.
Results of implementation
ABM TMS
Results for Qualiko
-
Reduced the number of late arrivals. The rate decreased from 12% to 5%.
-
As a result of the implementation of ABM Rinkai TMS, the entire logistics department was able to organize the work. At the moment, with 1,136 delivery points and 231 vehicles, all routes are planned by only 1 logistician.
-
We automated the routing process. Previously, a lot of working time was spent manually calculating the capacity of trucks and the amount of goods that could be delivered by the existing fleet. Now, ABM Rinkai TMS independently plans deliveries with the maximum vehicle capacity, and the company is able to deliver several orders at the same time with one vehicle.
-
Thanks to the analytical module of the ABM Rinkai TMS system, we now have control over route execution. Now logisticians can track the delivery process in real time. It's also possible to analyze the performance of each driver and route, and based on this information, make the most informed and effective decisions.
-
The level of customer service has improved.
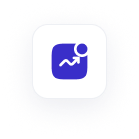
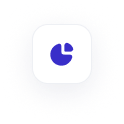
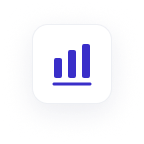
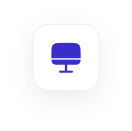
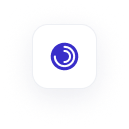
Video review:
We appreciate that you are interested in our products. One of our staff will be in touch with you shortly. Have a great day!