What are the benefits of implementing a transport management system?
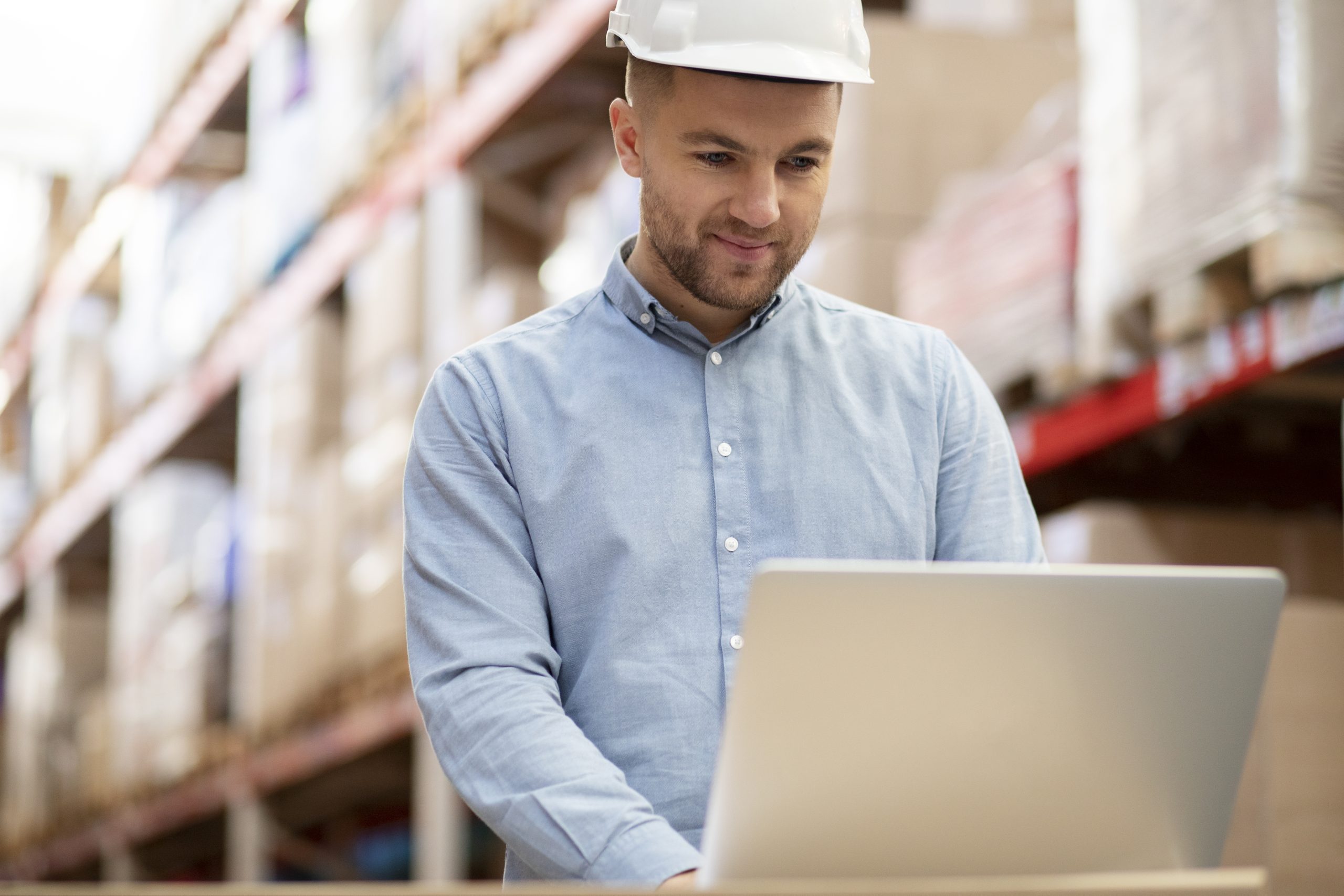
Last-mile delivery is the most expensive part of the delivery chain, as it involves many variables and requires speed from the performer. Unlike trunk lines, last-mile delivery involves point deliveries, which require many vehicles, and drivers increase the number of stops and complicate the route. In this sphere, we need to consider sanitary, technical, and temperature requirements for transportation of certain groups of goods and the client’s requirements for the quality of delivery. Since the quality of last-mile delivery directly affects the experience and level of customer loyalty, to be competitive in the market, optimize costs, and improve the quality of the process, companies need unique solutions to achieve this result.
For whom it is primarily essential to optimize the last mile delivery:
- couriers;
- logistics companies;
- food delivery companies;
- supermarkets with delivery;
- florists;
- restaurants with delivery;
- pharmacies with delivery;
- electronic commerce;
- FMCG distributors.
Three reasons to think about the implementation of a transport management system.
Automation
In the outdated version of logistics process construction, the logistician plans the route manually, that requires a significant investment of time – up to several hours and increases the risks associated with the human factor. Using TMS allows you to get a holistic platform that helps to manage transport systematically and automate all functions and procedures into a single process. In this case, the logistician has the opportunity not to waste time on a route construction, and he can concentrate on choosing the best option. The transport and logistics program will make all the calculations accurately in minutes. In addition, automation allows you to quickly and efficiently scale a well-established process with a guaranteed level of quality.
For example, companies that have implemented TMS have been able to improve the speed and quality of route planning:
- In the “Avangard” agro holding, only 3 logisticians plan routes of 24 branches across the country and are 100% interchangeable.
- “FoodEx” managed to reduce route planning time by 4 times. At the same time, the company’s number of clients increased by 2.5 times.
Service Enhancement (NPS)
The critical component of customer satisfaction is the level of service. The quality of delivery is the primary indicator of this service. A separate concept appeared – “Just in time” when delivery should be on time, which means it should be invested in time windows. However, if the time windows are reduced, it inevitably creates problems with the number of vehicles or the delivery costs.
With the help of TMS, when planning a delivery, it is immediately apparent the amount of transport required to complete the task. With ABM Rinkai TMS, the driver sees the order of visiting points, the planned time at the delivery point, and the client’s time window in the route list. The function of the route sheet alone allows you to get a significant effect from the use of TMS.
At the same time, in addition to the need to increase NPS, B2C companies have the task of maintaining a certain break-even point. It is crucial to find a balance that will suit companies in terms of costs and the client, who receives the goods after the order is placed. With the help of TMS, you can quickly measure the break-even point – correlate the size of time windows with the number of timely or late visits to the client. If necessary, you can generate reports by vehicles and carriers.
As an example of working with customer experience, the case of “FoodEx” balanced meal delivery service is indicative. They implemented TMS in 1.5 months, which immediately increased NPS since the client received his order at a well-defined time. At the same time, even the night before, the client gets a notification with the arrival time adjustment, and he knows exactly when the order will arrive. For the companies operating in the B2C segment, delivery is one of the critical elements of service evaluation. At “FoodEx”, the delivery of the daily ration takes place in the morning between 6:00 AM and 11:00 AM with a time window ranging from 30 to 60 minutes.
For the companies that included the work with the timeliness of delivery in the KPI results can be noted:
- Meat processing plant “Yubileyny” can now deliver products to company stores until 9:00 AM.
- “MHP” (“Qualiko”) has reduced the unloading time at the point by 30%, and the lateness rate has decreased by 20% through real-time automated control.
Cost reduction
Before investing in logistics planning and optimization software, it is essential to understand the profitability of a project. The total logistics costs for each company are available in the financial statements. However, it is difficult to trace the factors influencing the formation of this cost item. Therefore, it is essential to derive key performance indicators for process control and regulation:
- planned and actual mileage;
- the amount of transport used;
- monetary unit for the weight and size parameters of the products planned for delivery;
- the number of exported kg (cubic meters, etc.) per 1 kilometer of distance.
By noticing an increase in costs using these indicators, you can find the root cause of the expenses.
After the implementation of TMS, companies were able to track the improvement in key indicators:
- Engin’s active customer base increased by 25%, while the number of vehicles needed to deliver orders increased by only 14%.
- Delivery costs of the leader in the production of dairy products – “Lustdorf” for one store decreased by 21%, and delivery costs for the delivery of one kilogram of products decreased by 25%.
- Meat-packing plant “Yubileiny” notes the optimization of the personnel of the logistics department by 15%. The reduction in fuel consumption per unit of exported products amounted to 12%.
Service and transport logistics costs are a kind of “scale”. It is crucial to understand whether we are moving towards a balance of the first and second or prefer one thing.
ABM Rinkai TMS is used by companies in more than 15 countries worldwide. The team implements complex projects. Before the start, a simulation is performed technical support team The customer success team is connected at all stages: during implementation and the use of the product. For convenience, a separate mobile application – Route Sense. The solution is constantly updated to meet customer requirements.