TOP 3 steps for effective change inventory management
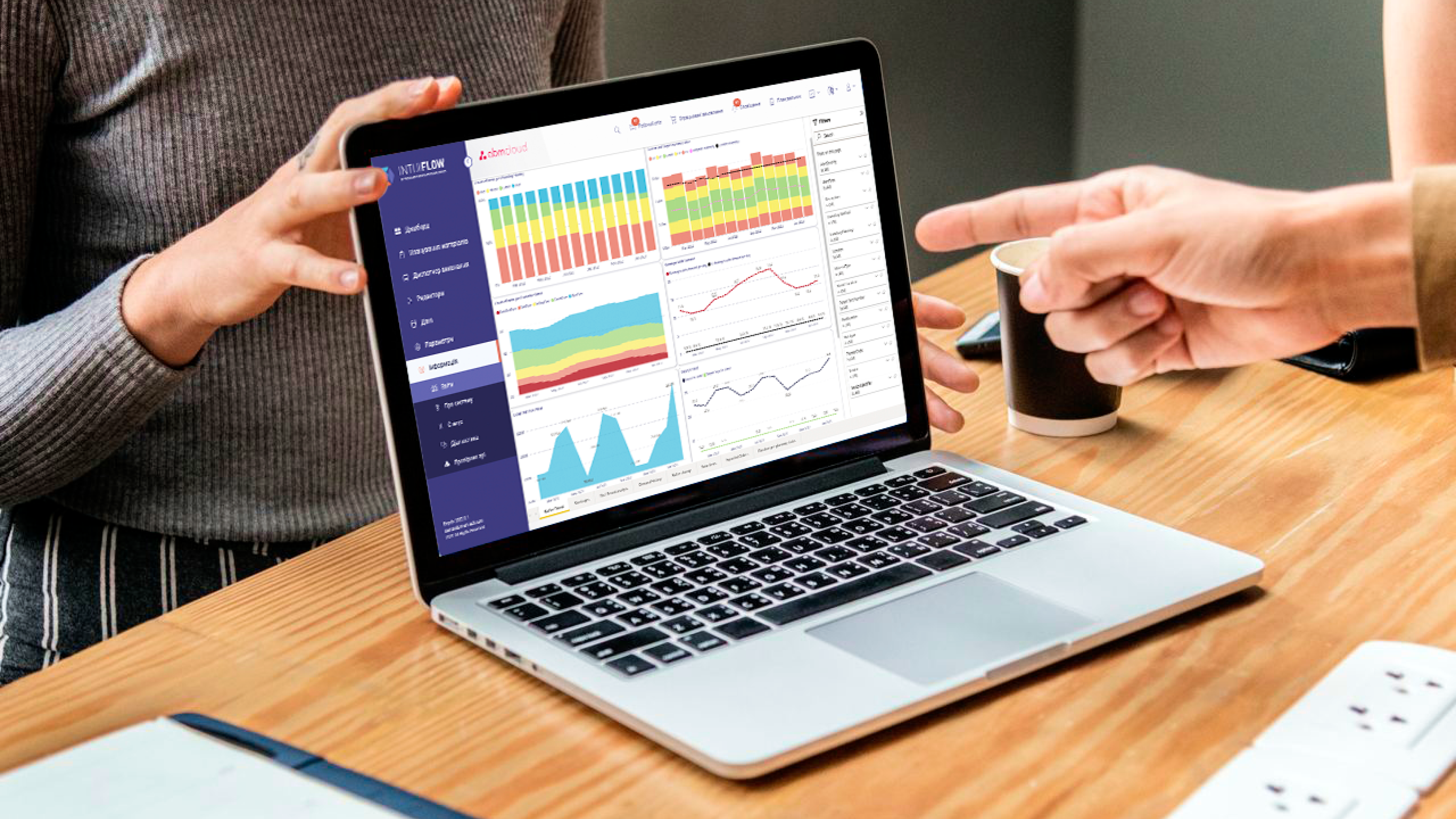
In today’s BANI world, where everything is changing and competition is at peak levels, it is important to “stay ahead of the game”. However, this is not always an easy task. One of the key tools for achieving competitiveness and economic sustainability is the implementation of technologies, software and change inventory management.
The real challenge is how fully the software will fit into the company’s existing business processes, as this is what determines the economic results and competitive advantage the company will gain in the future.
We have prepared this article to provide a clear understanding of where your company should strategically focus its attention. Our goal is to help you understand the key aspects of technology adoption and show you how it can be a powerful part of your success.
Challenges of today’s manufacturers and distributors
We`d like to start this article with the main challenges that manufacturers and distributors face today:
- Delayed process. The implementation timeline of technologies often extends beyond the agreed-upon boundaries. This can be attributed to technical or resource issues, peculiarities in the company’s business processes, or insufficient time allocation by key project stakeholders on the client’s side.
- Staff rejection of radical changes. Managers may sabotage the implementation process because it is a change of established habits that have been formed over the years in the company.
- Changing priorities. A company may change project goals or resources begin to be allocated to other projects.
- Change of team. Changing users, project managers, or technical specialists directly affects the course of the project, as there is an immediate understanding that it takes time to adapt to the new team members, as well as to transfer the necessary knowledge to them.
- The functionality of the system is not used 100%. This can happen for various reasons: insufficient resources or training, lack of understanding of how to use the new system by the company’s employees.
- The data needed to run the project is simply not kept up to date by users or is even missing from the records. Before you begin the automation process in your company, you need to carefully determine the degree of automation that is currently used in your company’s inventory management processes.
If your answer is yes, sufficiently automated, then you are on the right track. To assess if there are areas you can optimize – note what percentage of your purchasing mix is already automated. Based on what methodology? How much staff time is spent manually adjusting the quantities recommended by the system for ordering? If you use methods based on forecasting, it is likely that during the uncertainty your business has already experienced weaknesses in its profits: the dependence of the result on the accuracy of the forecast, failures of the entire chain even in case of small deviations. VUCA and the new world of BANI (fragile, disturbing, non-linear, incomprehensible) require companies to use new approaches that correspond to reality, take into account real demand, and promptly respond to its changes.
If your answer is no, your inventory management processes are not automated at all yet, then you should realize that in the complete absence of automation, there is no single approach to inventory management, any manager can form their own methodology and replenishment algorithms that are based on their own experience. This leads to the fact that people become indispensable, it is impossible to solve their tasks when they are absent. Such a system is highly risky and non-transparent for the company’s management. In this case, you need to act now. The automation project will significantly increase the transparency of the system for top management, take away the routine component of the work of specialists, reduce the degree of influence of the human factor, and increase business efficiency.
What are the top 3 steps we recommend for automating your inventory management process?
Team Formation. The process of system implementation must necessarily involve:
- project sponsor (owner, co-owner of the company, director, top management)
- head of planning
- head of production or distribution
- head of logistics
- IT-specialists
- main users of the system (managers)
Updating data for system integration. The following data are required for calculations:
- current balances in the system
- current orders to suppliers and production
- up-to-date customer orders, distribution orders
- production specifications or distribution routes
- SKU parameters: min. lots, order cycles or frequency, lead-time, actual consumption or forecast, cost price, etc.
It’s worth noting that the lack of certain data is not a reason to give up on automation.
From our practice, no client company had all the necessary data ready before the project started. However one of the advantages of implementing the Intuiflow system is that all the necessary data is collected, updated, and entered into the accounting system as part of the project. Thus, at the end of the project you have not only customized software but also up-to-date data and properly built processes
![]()
Alina Dorosh, Senior Project Manager at ABM Cloud.
Support for the project. For a project to be successful in the long term, it must ensure:
- Motivate for change: train users to work independently in the system, reward them for achieving results
- guarantee continuous development, and update the system functionality, this is ensured by the implementation team
- data maintenance up-to-date
After figuring out the specific steps that company management must take to prepare for technology implementation, an important question arises: what system to choose and what functionalities are important to have in the system to meet user needs and achieve future supply chain management results. Thus, identifying the key decision criteria becomes an important step. In this regard, we would like to share our top criteria for system selection:
- Quick launch, expected results, and return on investment
- Transparency of the control system for management
- Ease of use of the system by employees
- Possibility of remote work in the cloud Cases of successful implementations in various industries
- The modern methodology on which INTUIFLOW is based
- Developed implementation technology
- Constant updating of the system’s functionality and training of personnel
- Clear priorities, recommendations, system notifications for replenishment, flexible analytics
- Possibility to integrate with any commodity accounting system
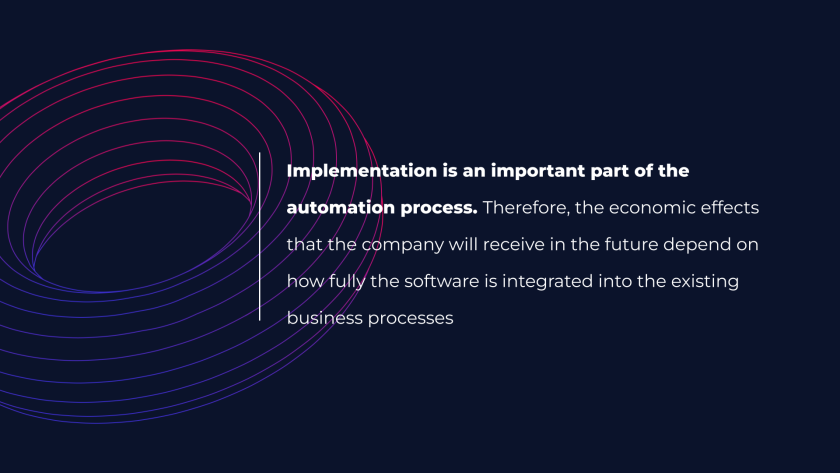
For a successful implementation project, from our ABM Cloud team, we recommend using the following scrum methods:
- Daily meetings. It is important to involve all participants in the process as much as possible so that everyone has an idea of how the project is progressing
- Using a task board. Kanban boards help you visually track tasks in progress, as well as generate the following
- An iterative approach and dividing a large task into subtasks. One large-scale task is broken down into smaller tasks and gradually realized. This is done to deliver value to the customer as quickly as possible and respond flexibly to changes
- Formation of customer competence center. A unified knowledge base is created in the LMS system, onboarding new managers to form a team of interchangeable experts
Our team specializes in implementing an innovative inventory management system for manufacturing and distribution known as Intuiflow. The name means that the system allows you to manage the flow of materials and information intuitively and extremely simply. We offer training services on the system and the methodology behind it, project implementation, and provide ongoing support for your company through our full-time customer support team.
It is important to note that our system provides high results. The average quantitative results that companies get from using the system can be seen below:
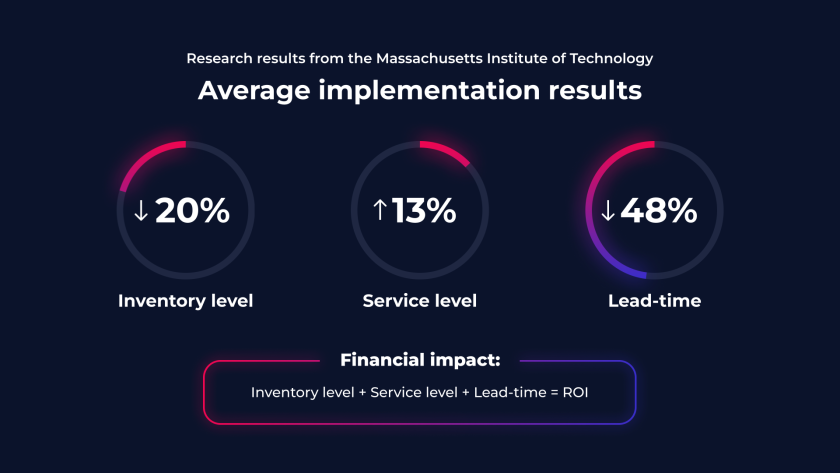
In terms of qualitative changes, we have seen the following positive trends: increased stability of planning, increased clarity of priorities, increased level of control over operations, and reliability of material flows.
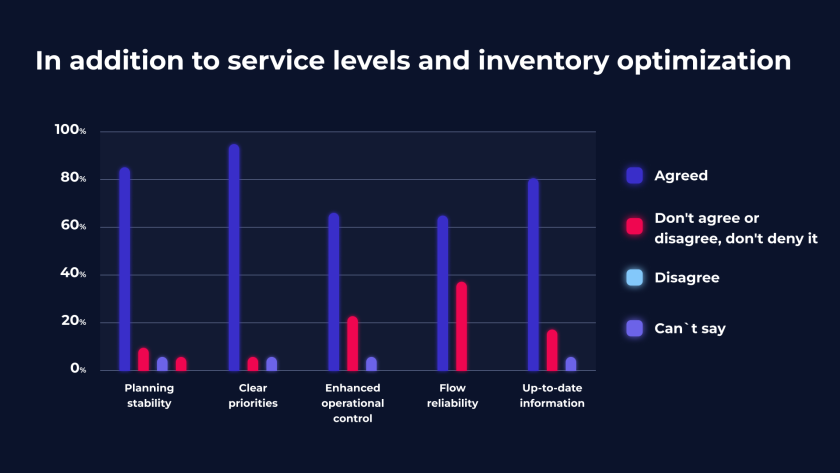
In conclusion, it should be noted that inventory management automation is a necessary stage in the development of any company. It affects all aspects of operations – from optimizing financial performance to improving customer satisfaction. Companies can maximize their operational efficiency, minimize risk, and provide high-quality service to their customers.
If you still haven’t considered implementing inventory management automation systems, now is the time. Contact our team for a detailed consultation and an assessment of how we can help you reach new heights in inventory management. Your company will gain an undeniable competitive advantage, so you can manage the future with confidence.