Efficient use of warehouse space
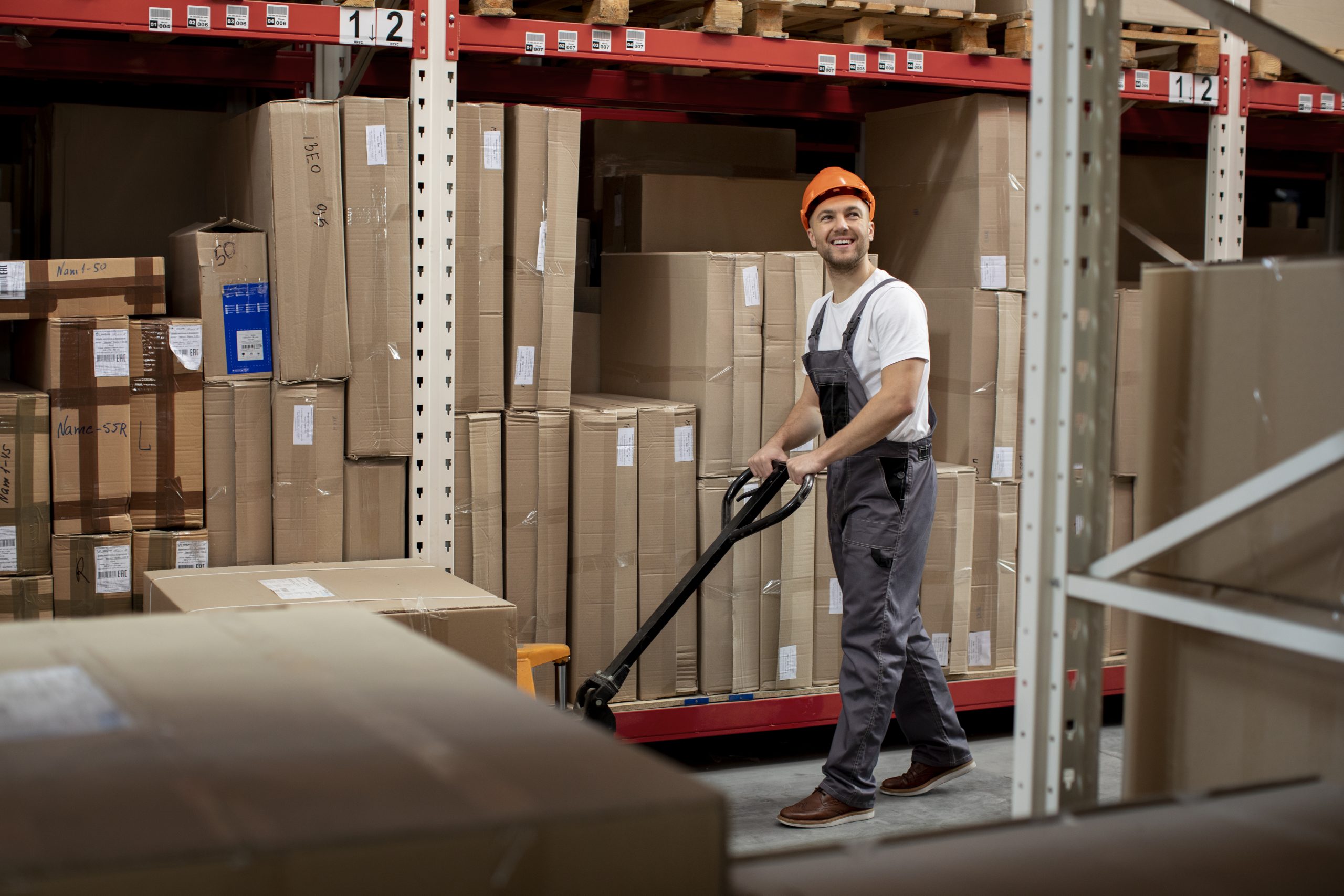
Efficient use of warehouse space, both for storage, forwarding, processing, and auxiliary, is impossible without optimizing the parameters of warehouse areas, allocating short-term storage areas for goods with a high turnover rate and storage areas for goods with a low demand and insurance stocks.
How to organize the rational placement of goods in a warehouse? The main areas (zones) of the warehouse
A list of the main technological operating areas (zones) for the rational placement of goods in the warehouse, which should be connected to each other by aisles and passages:
- unloading area;
- acceptance area for quantity and quality;
- storage area;
- order picking area;
- shipment area.
Optimal zoning of the warehouse: the unloading area is adjacent to the receiving area in terms of quantity and quality. The storage area is adjacent to the order picking area and is located next to the shipping area.
In the receiving area, the quantity and quality of the goods are recorded, as well as temporary storage records until the goods are transferred to the warehouse storage area. When preparing the goods for storage, storage areas are formed. Goods are delivered to the storage area from the receiving area or the unloading area. Orders are selected and formed in the picking area.
Rational placement and stacking of goods in the warehouse: key aspects of optimization
- Intensity of cargo flow.
If the intensity of the incoming flow exceeds the outgoing flow, there may be a lack of warehouse space. - Packaging, storage methods.
Goods with a short shelf life should be placed closer to the main aisles, fragile goods should be placed higher and further away from the main aisles, defective goods should be placed on high shelves and in corners, and goods for labeling/packaging/packaging should be placed on low shelves. Proper zoning of the warehouse and selection of equipment helps to ensure the rational placement of goods in the warehouse. - Warehouse structure.
The warehouse space is not always perfect – there are ledges, recesses, columns, partitions. There may also be restrictions on the warehouse load. To avoid surprises, it is recommended to calculate an individual project for the use of warehouse space. - Warehouse operations.
The warehouse can be zoned according to warehouse operations – placement, unloading, loading, sorting, packaging, storage. - Warehouse staff.
Based on many years of experience in auditing and restructuring warehouse complexes of various types, types, and formats, we recommend “growing” staff, encouraging, training, and motivating them.
Rational use of warehouse space: organization of the goods placement system
The rational use of warehouse space can be calculated using the main space utilization factors (depending on the type of warehouse, layout, and equipment, the value can range from 0.25 to 0.6 – the higher the figure, the more efficient the use of warehouse space) and volume (capacity).
Calculation formulas:
Warehouse space utilization = cargo area / total warehouse area
Warehouse volume utilization rate = warehouse cargo volume / total warehouse volume
A WMS system (for example, ABM WMS) with the necessary functionality, such as
- the ability to categorize by grade, size, and inventory turnover;
- the ability to account for volumes;
- the ability to keep records of the order of receipt of goods to the warehouse;
- the ability to keep records of the commodity neighborhood;
- the ability to take into account the specific properties of the goods;
- the ability to group goods by assortment;
- ability to group goods by storage mode.
Minimizing cargo flows is facilitated by placing goods with high turnover, heavy and bulky goods close to the unloading area. Goods with large volumes of receipts and sales are usually located near the order picking area. In contrast, goods for long-term storage should be placed further away from entrances and exits.
The principle of commodity neighborhood
To ensure order in the arrangement of goods in the warehouse, it is advisable to assign permanent storage locations to goods of certain types/groups/subgroups.
Odorous, moisture-emitting, flammable, and highly hygroscopic goods should be stored separately from each other. It is better not to store fabrics next to household chemicals, and sugar/flour next to fruit.
Efficient use of warehouse space
Efficient use of warehouse space is achieved by assigning a code to storage areas, which greatly facilitates the selection of goods and is also duplicated in quantitative warehouse accounting. The code of storage locations for each group of goods consists of numeric or alphanumeric designations. The code consists of a rack number, section, tier, and cell.
Different methods of placing goods are used (depending on the features and characteristics of the goods), which ensure the efficient use of the warehouse space: nomenclature, grade, complete, batch, etc.
An assortment with many values and small storage volumes is most often placed using the nomenclature or varietal method, when each SKU is assigned a specific storage location, such as a rack, shelf, cell, or stack, based on brand and size.
The complete method of placing goods in the warehouse involves the joint storage of product sets that differ in the types of goods and the products themselves, but are shipped at the same time.
FMCG (Fast Moving Consumer Goods) goods of various types and names are placed in batches, with replenishment until the end of the sale of these goods.
Regardless of the size, type of warehouse, characteristics of the goods, ABM Cloud warehouse logistics experts are ready to advise on the rational use of warehouse space and placement of goods in the warehouse.