Background
Decentralised inventory management system.
Costs of moving goods between stores due to incorrect distribution of goods from the central store across the network.
Surpluses in some stores and lost sales in others.
Formation of network orders manually by central warehouse managers in Excel and in the accounting system (1C) by store supervisors.
The rapid obsolescence of goods and their high cost requires controlling not only the level of stocks, but also the assortment, which managers had no time for.
High influence of the human factor.
Project goals
Progress of the project
Centralisation of procurement:
The ABM Inventory team, together with the Evrika project team, centralised all procurement processes. This ensured more efficient inventory management, reduced redundant costs, and improved supply coordination.
Appointment of managers:
Eleven managers responsible for purchasing at the central warehouse and in stores have been appointed. They coordinate purchases, interact with suppliers and ensure timely replenishment of stocks.
Create order and delivery schedules:
We have developed order and delivery schedules that optimise supply processes. This ensures timely delivery of goods, reduces delays and transport costs.
Assortment automation:
Within four days, the entire assortment of each store was connected to the automated ordering system. This allows orders to be placed based on current stock levels and forecast demand, avoiding overstocks and shortages.
Setting up the process of replacing goods:
The process of replacing goods is set up to solve two tasks:
removing goods of one alternative group from the assortment and introducing new goods;
automation of the formation of orders for goods in an alternative group, taking into account the balances of the entire group.
Results of ABM Inventory implementation
Key effects:
-
Transition to a centralized inventory management system.
-
Improved turnover by 2 times.
-
Reduction of surpluses by 1.5 times.
-
Automation of the order formation process taking into account such factors as seasonal fluctuations, availability of substitute goods, and the balance of goods in the centralized inventory management system. In this regard, freeing up time that managers can use to manage the assortment.
-
Setting minimum order quantities and package sizes.
-
Introducing the functionality of removing products from the assortment.
-
Setting up scheduled shares and seasonal fluctuation algorithms.
-
Setting up analytics to monitor overstock, lost sales, OUT stock, and last week's stock.
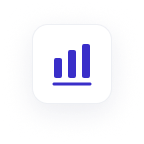
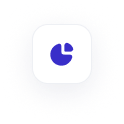
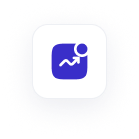
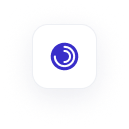
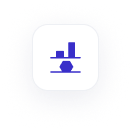
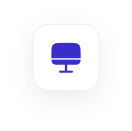
We appreciate that you are interested in our products. One of our staff will be in touch with you shortly. Have a great day!