Automated Ordering of Goods
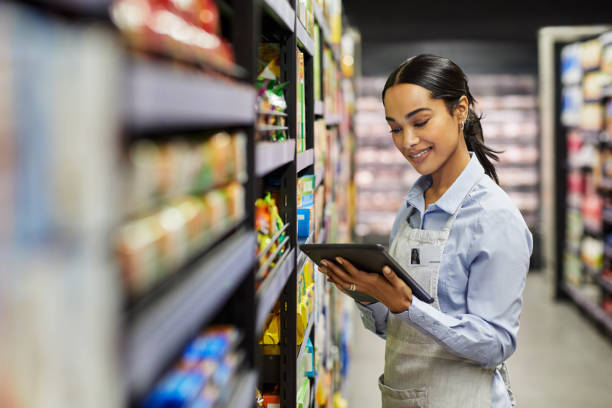
Article Contents:
Automated ordering of goods (auto-ordering) in ABM Inventory: reducing lost sales, improving product availability, and speeding up inventory turnover. What tasks does the auto-ordering system solve in retail? What effects does the company experience?
Instead of a Prologue
I have a DREAM. I see myself sitting on the shore of Lake Geneva with a glass of champagne in hand, working. My workday starts at 8 a.m. and ends at 8:01 a.m. My job is pressing a single button on my laptop. What is my job? I am an inventory management manager (or purchaser) and I manage inventory using an automated inventory management system, commonly called auto-ordering.
This is the kind of picture imagined by those just starting to think about automating the procurement process. Managers think the system will fully handle their work. Business owners and executives, when considering the implementation of an automated inventory management system, often see the effect primarily as reducing jobs and the time spent processing orders. Both are partly right, but these are not the main tasks or effects of automating the ordering process (auto-ordering) in retail.
Automated Ordering System
The automated ordering system for goods from suppliers is a complex of inventory and ordering management processes, with the main functions including:
- Maintaining inventory levels at a set standard to ensure constant product availability at optimal stock levels within the system. This is achieved through the automatic execution of processes such as:
- Order planning
- Order generation
- Order optimization
- Order submission
- Periodic adjustment of the necessary storage level
- Economic justification of the maintained level
- Inventory status monitoring
- Assortment management. To achieve this:
- various forecasting mechanisms are used. The more complex the formula and the more well-known the name associated with the forecasting method, the better the forecast results align with actual sales. Unlike systems based on forecasts, the ABM Cloud inventory management system uses a buffer stock tool when planning orders, focusing not on sales forecasts but on current stock levels and target inventory levels.
- Automated generation and submission of orders to suppliers
- Automatic order optimization to reduce logistics costs
- System alerts for under-delivery and the need for urgent orders due to insufficient current stock levels
- Specialized reports for inventory status monitoring (excess stock, lost sales, supplier reliability, stock dynamics, etc.)
- Reports utilized in assortment management. The auto-ordering system provides insights on which items, due to low turnover, can be removed from regular stock, which ordered items are popular and can be included in the permanent assortment, and whether there are remaining stocks of items being phased out, etc.
- various forecasting mechanisms are used. The more complex the formula and the more well-known the name associated with the forecasting method, the better the forecast results align with actual sales. Unlike systems based on forecasts, the ABM Cloud inventory management system uses a buffer stock tool when planning orders, focusing not on sales forecasts but on current stock levels and target inventory levels.
As we can see, the capabilities of the system to bring the dream outlined in the prologue closer are indeed vast. The automated ordering system will take on a significant portion of the tasks related to order and inventory management. However, there will be functions that cannot be fully delegated to the system, where managerial decisions are necessary:
- Considerations include:
- – What needs to be addressed and what can be ignored due to its minimal impact on the company’s efficiency.
- – How likely is it that a product recommended for removal from the active assortment by the auto-ordering system is actually non-promising?
This is where manual management cannot be avoided.
The inventory and ordering management system significantly reduces the number of routine operations, provides detailed information about inventory status, and greatly simplifies the decision-making process. However, strategic tasks remain the responsibility of the manager. Moreover, these operations require a deep understanding of the market, the specifics of the enterprise’s operations, and oversight of business process compliance, which represents a much more complex functionality that demands high skill and good motivation.
Economic Effects of Using an Automated Ordering System
- Reduction of excess inventory (by 30-60%)
- Improvement in product availability (up to 98%)
- Decrease in lost sales
- Acceleration of inventory turnover
- Increased reliability of suppliers, etc.
The inventory management system allows for the management of vast amounts of information, enabling informed managerial decisions, as well as supporting, monitoring, and optimizing the company’s inventory with minimal time and resource expenditure. Your purchasing managers may indeed have a chalet in Switzerland, but that’s because automated ordering cannot function without human intervention, and this employee must possess all the talents of an effective Manager with a capital M.