Assortment optimization
Product assortment optimization becomes irreplaceable in view of modern trends of increasing the product versatility. There is a need to keep a bigger amount of different stock keeping units (SKU). Each separate stock unit requires a separate managing. However, the limitedness of money forces managers to design a single policy in order to manage all the units. This policy is usually based on forecasting, which is inaccurate and leads to the following deplorable consequences:
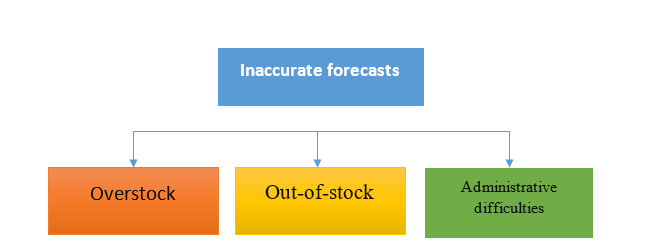
Assortment optimization
1. Deficiency of working capital due to decrease in turnover; 2. Distribution costs of unprofitable goods; 3. Advertising costs on development of marketing arrangements of slow-selling goods; 4. Expenses on storage and movement of product surplus; 5. Wearing and obsoleting of goods. |
1. Potentially closed lost client; 2. Loss of sales caused by deficiency of running positions; 3. No possibility of measuring the rate of lost sales; 4. Misestimation of SKU and suppliers. |
1. Absence of common methodology in SKU management; 2. Escalation of costs on ‘express order’s; 3. Faulty assessing the systems of suppliers’ credibility. |
In order to avoid similar risks, the optimization of product assortment in a store or a chain is needed. Obviously, we cannot consider the process of product assortment optimization separately from the other enterprise processes. It is necessary to consider the whole system of inventory management and the ABM Cloud system will help to do it.
Optimization of a store’s product assortment with help of the ABM Cloud system?
You must admit that if the forecasts would be more accurate, there would be less problems! The assortment would meet the clients’ demands, there would be no unsaleable goods, goods would be always in the needed volume. Thanks to the ABM Cloud system, you have a possibility to optimize the assortment of goods based on accurate numbers and analytical findings.
In order for a business to be a successful one, the products with good turnover should form the turnover’s basis. With help of the system reports “TOP Mover Company” and “TOP Mover Warehouse”, you will easily detect the goods that generate 80 % of company’s turnover. TOP Mover is calculated and defined as of the first day of month.
Minimizing the number of unsaleable goods with low turnover is as equally important. The system detects the non-moving goods making 2 % of company’s total turnover within the last 3 months, so-called NON mover. In such way, the program draws your attention to the possibility of removing this product from the assortment.
Possibilities of the ABM Cloud system
Everyday reports based on the analysis of the buffer of reserves demonstrate the most effective type of delivery for each SKU. You can easily define the product that always should be in-stock at storage locations. The report presents the list of MTO (Make-To-Order) SKU, which are suggested to be transferred to MTS (Make-To-Stock). It will give a possibility to keep the surplus of necessary product at a warehouse, which was earlier delivered only due to a special order. Therefore, you can avoid loss of sales that are caused by deficiency in the running positions.
Methodology of ABM Cloud system helps to correct and optimize the product assortment due to the actual demand of consumers. The system automatically estimates the available surplus of each SKU and outputs the information in compact reports.
The following are the reports that help to make quantitative and qualitative changes into the assortment structure with purpose of its optimization:
-
TOP Mover company report:
shows company’s TOP Movers generating 80 % of turnover;
-
NON Mover company report:
shows slow-moving goods;
-
Lost Sales SKU per week:
shows due to the shortage of which SKU a company lost its sales;
-
Overstock SKU per week:
shows due to which SKU a company got surplus;
-
SKU Count:
shows the summarized data of the available TOP and NON in a company.
-
Transfer of MTO into MTS (MTO2МТ
S):
presents a list of MTO SKU that are offered for transferring into MTS due to request of unscheduled replenishment in the delivery process.
You can find more about the functional capabilities of the system and the effects that a company achieves using the ABM Cloud at free webinars or you can order an individual presentation.