ABM Inventory management solution impact
Switch your store and warehouse inventory management system into autopilot mode and increase your business turnover and profitability.



We are dedicated to assisting retailers of all sizes and formats
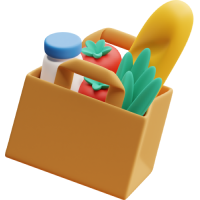
Food & Beverages
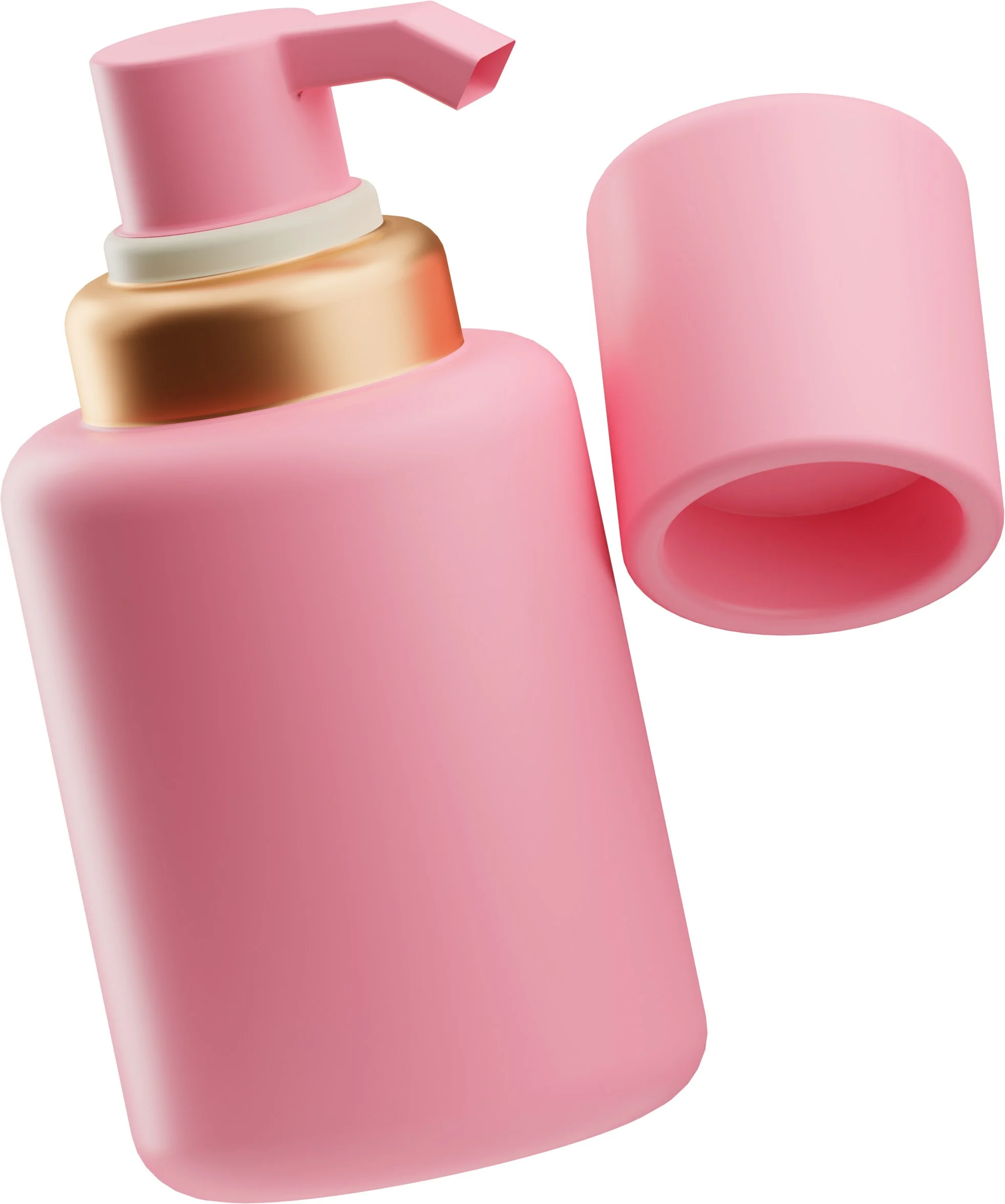
Health & Beauty
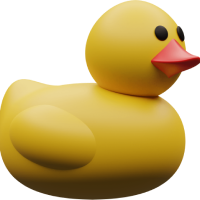
Toy stores

DIY
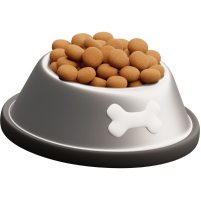
Pet stores
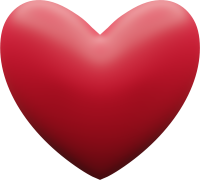
Pharmacies
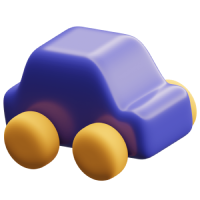
Auto parts

Electronics
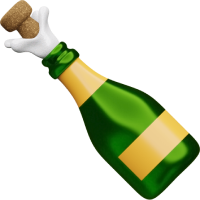
Liquor stores
ABM Inventory system features
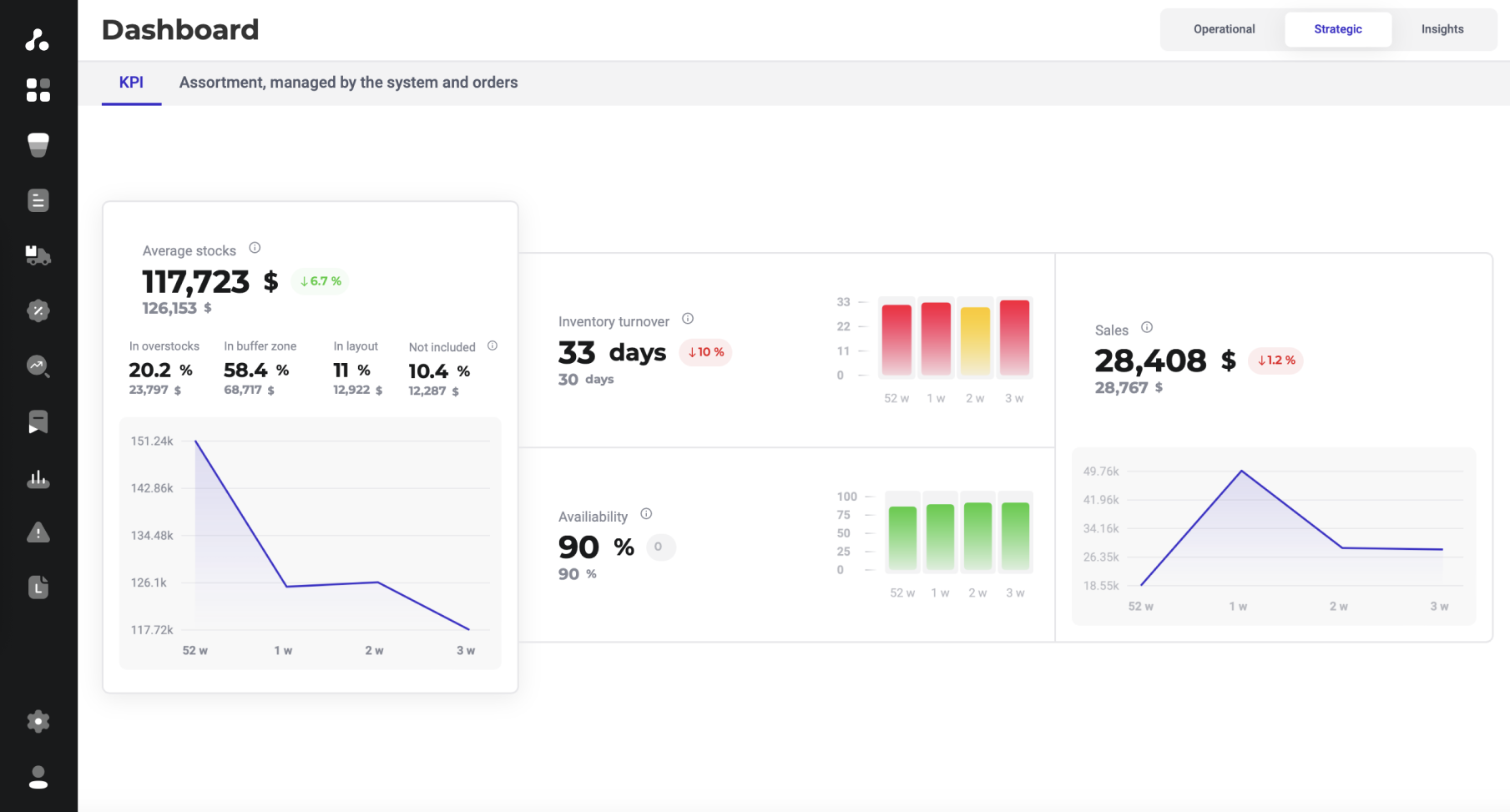
-
Operational
Provides the manager with an up-to-date list of tasks and shows how specific indicators of surplus and lost sales have changed on a daily basis. In case of negative dynamics, the system offers an additional report that helps to understand the reason for the trend.
-
Strategic
Comprehensive analysis of stocks, sales, availability, and turnover, their dynamics, as well as the efficiency of using the system and the accuracy of the generated orders.
-
Insights
An analytical overview of the inventory structure that allows you to focus on problem areas that can have a serious impact on the business.
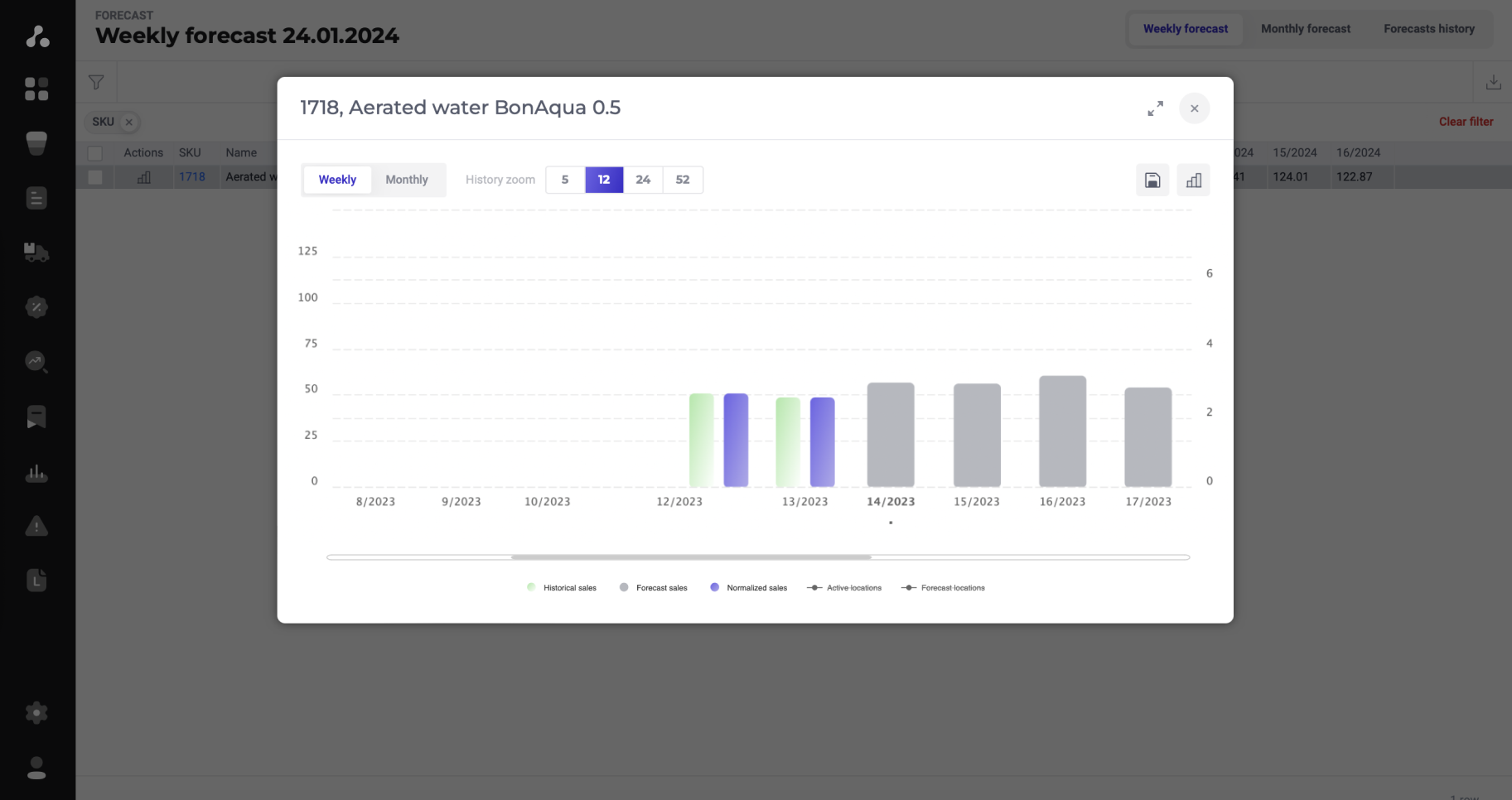
-
Strategic decision making
Precise ML-based forecasting allows you to make informed decisions regarding assortment expansion, opening of new stores, planning annual budgets and KPIs.
-
Determine the level of influence for each demand factor
The system takes into account only statistically significant factors, omitting negligible factors that reduce the accuracy of the forecast.
-
Forecasting based on business specifics
Depending on the specific requirements, the system builds a forecast using one of 3 forecasting models.
-
Assortment management tailored to customer preferences
Your customers will know that they will always find the right product at an affordable price. And you will be sure that they will come back to you.
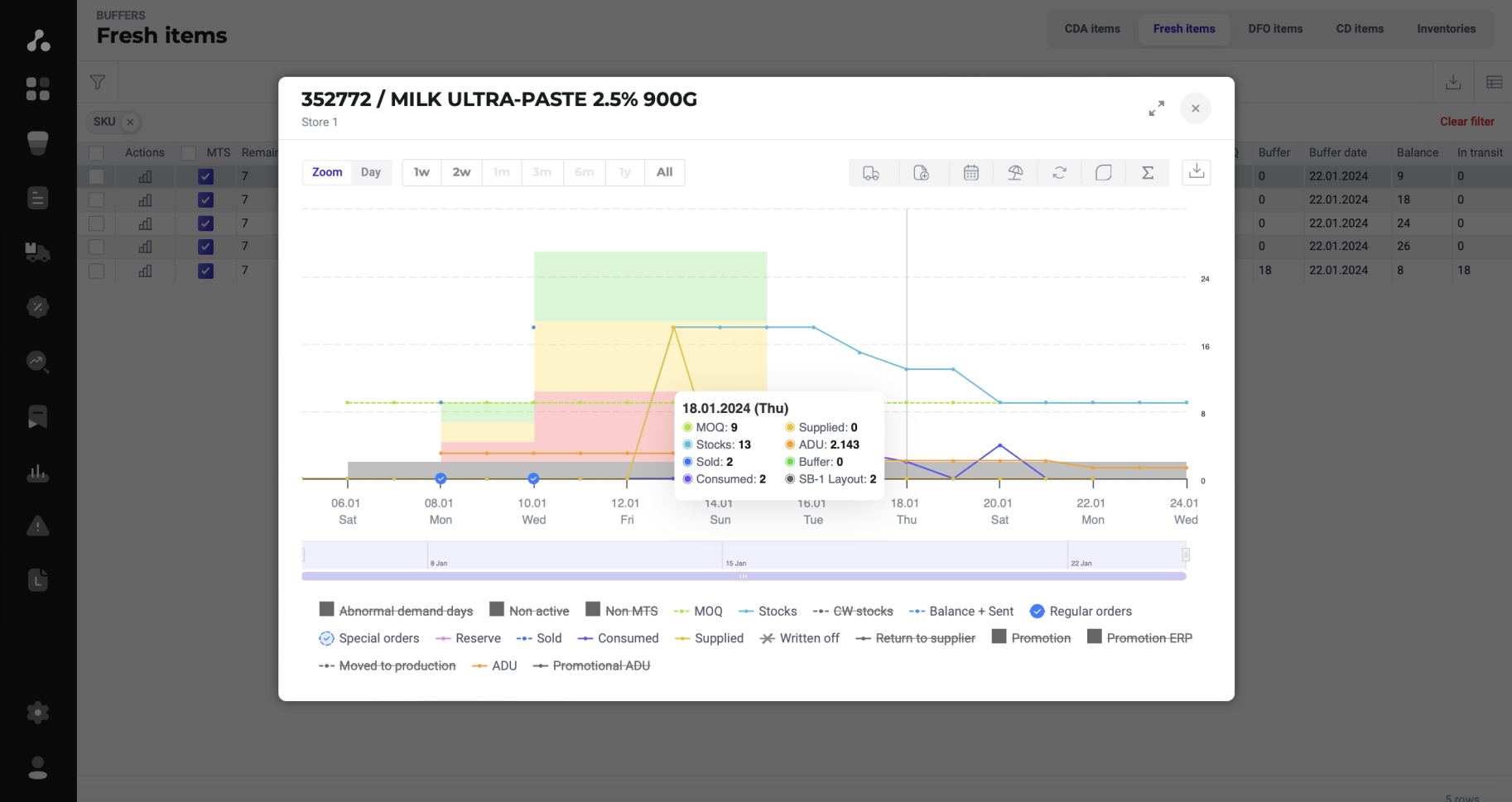
-
Calculation of the required quantity of goods
Taking into account the demand for each SKU at each point of sale and analyzing the available balance and goods in transit.
-
Formation and dispatch of orders
Every day, after calculating the demand, orders are automatically generated based on the assortment matrices and schedules. Then the orders are automatically sent to the user's system and suppliers.
-
Automatic editing and control of order fulfillment
Allows the supplier to edit the quantity of goods after receiving the order, automatically updating the information in the sent orders and tracks the delivery time of the order, sending a notification to the manager in case of delay and recording information about the delay in the analytical report.
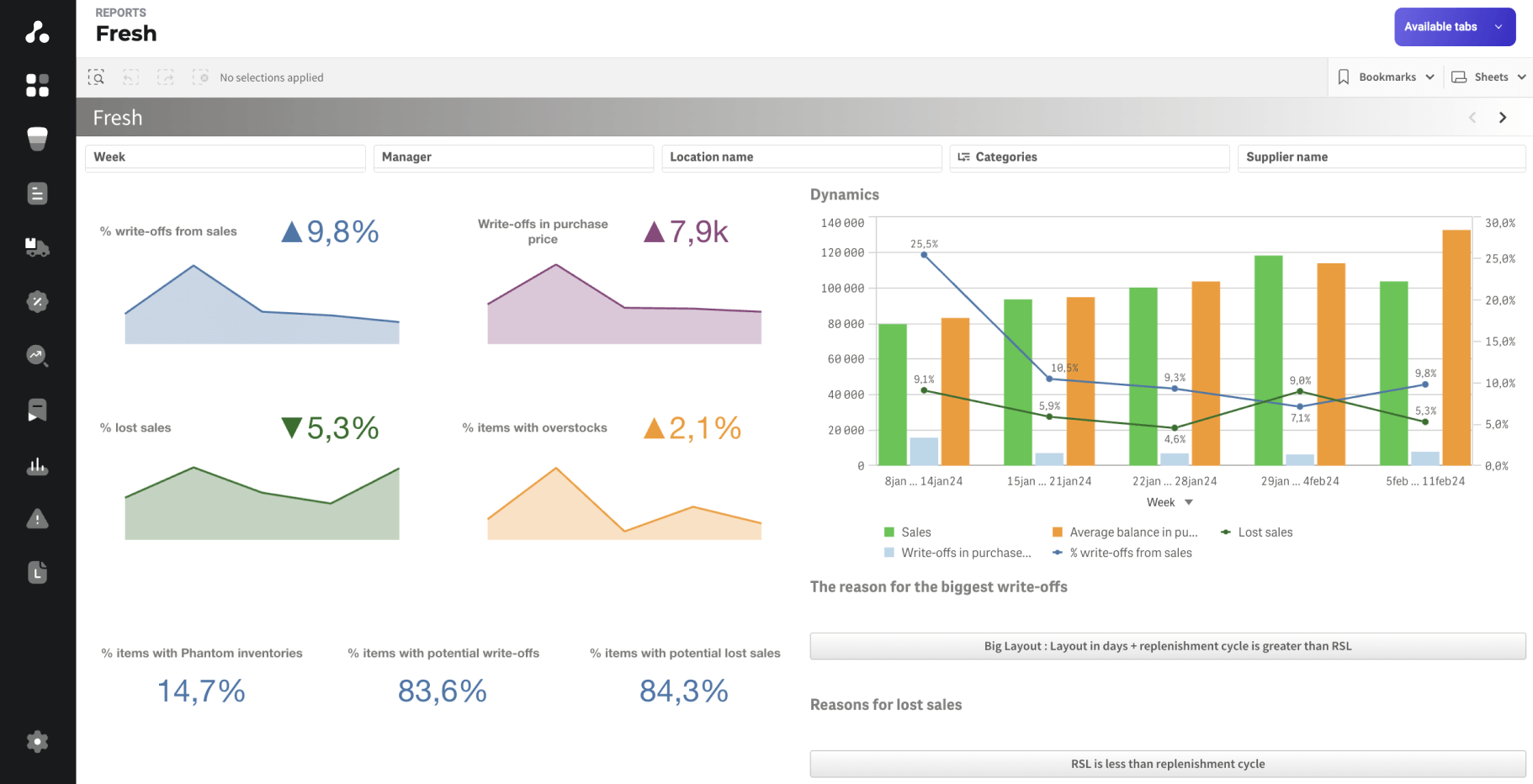
-
All key factors are taken into account:
Demand forecast, order fulfillment time, packaging and supplier restrictions, demand volatility, available stocks.
-
Takes into account the remaining shelf life and weekday-related demand variation
-
A simplified analogue of LIFO batch accounting
-
Required availability level:
Allows you to set an acceptable level of availability for each item to avoid write-offs.
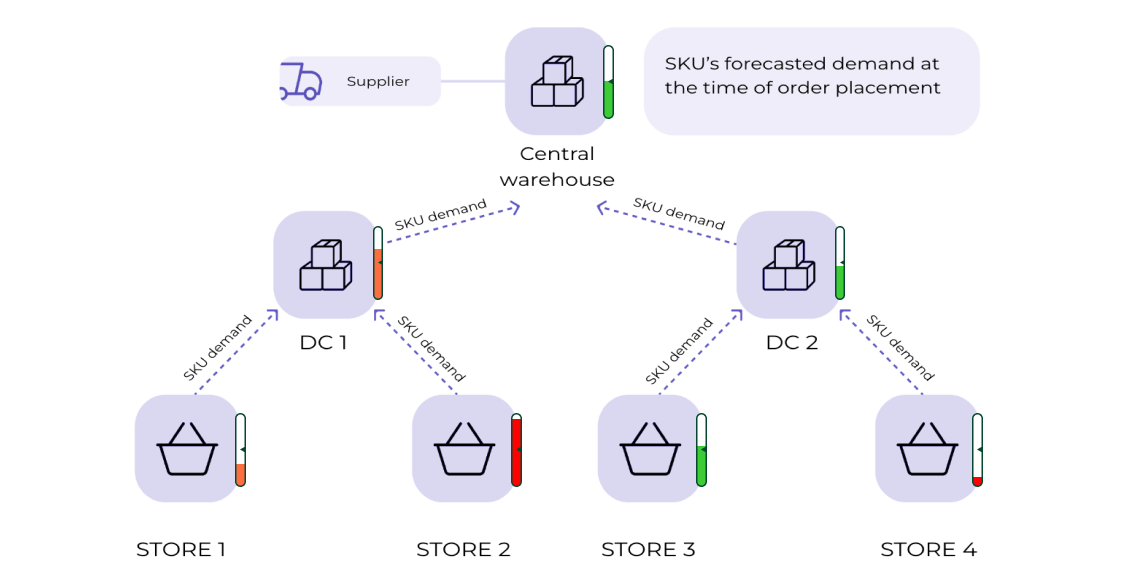
-
Ensuring inventory balances
Transparent, unified inventory management process at all levels of the supply chain due to the close connection between supply and demand of goods.
-
The system takes into account various business processes of supply:
Classic warehouse storage, cross-docking, pick by line, pick by zero;
-
Flexible settings
There is a possibility of truly flexible algorithm settings that take into account all the necessary factors and features of the goods delivery process.
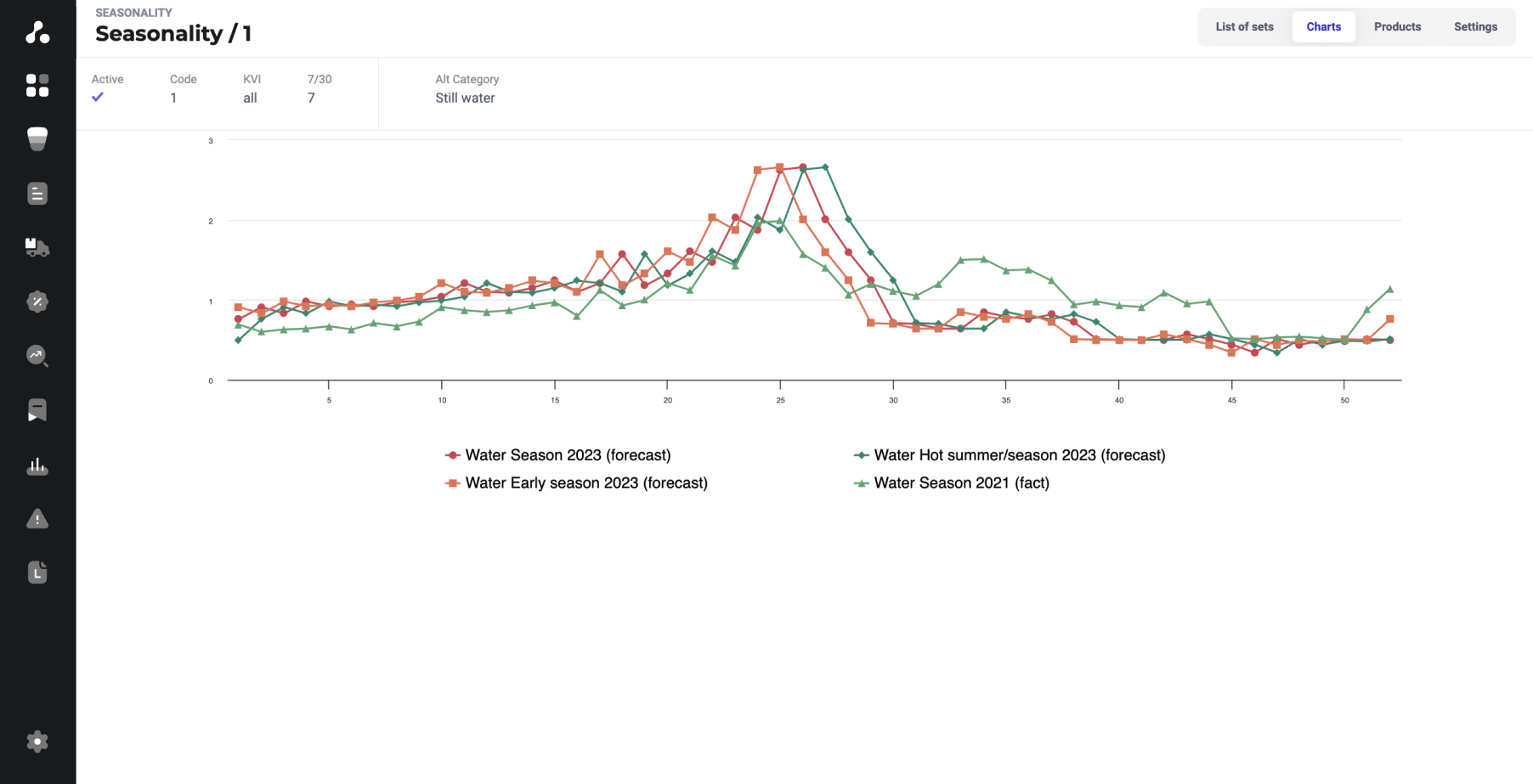
-
Automatic calculation and application of seasonality coefficients
Taking into account demand fluctuations for a regular assortment, seasonal goods, and those that are available only for a limited time.
-
A set of different scenarios
They are applied depending on the market situation.
-
Quick analysis due to high-quality visualization
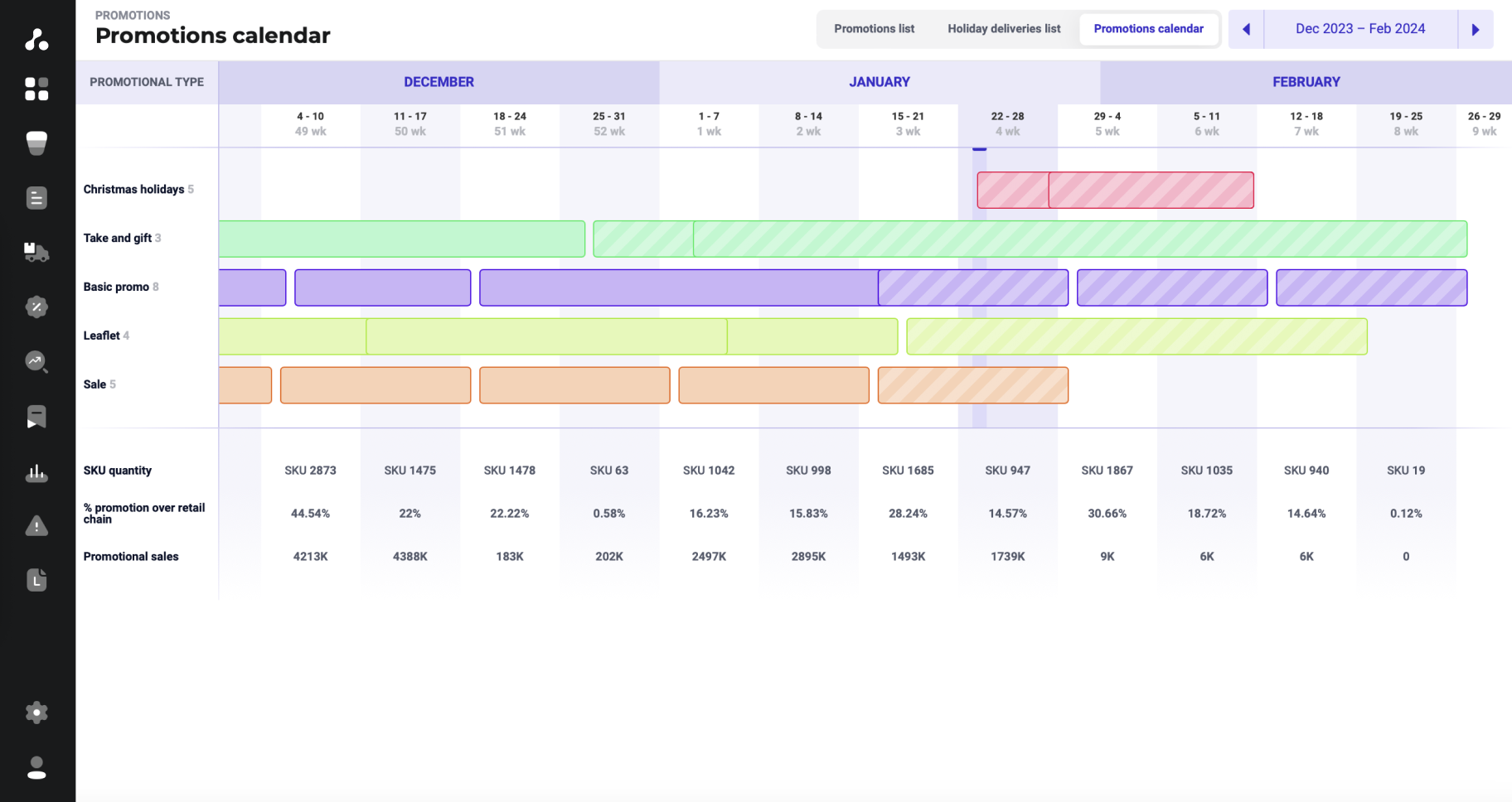
-
Sales forecasting and preparation for promotional activities
The forecast is generated with the help of ML models taking into account various factors affecting the demand for promotional products.
-
Flexible response to actual demand during the promo
The system analyzes sales and demand, recalculating the required inventory level for each store. Therefore, allowing you to strike the balance between high product availability and minimal overstocks across all outlets.
-
Promo performance analysis
Allows you to quickly assess the promotion’s effectiveness by evaluating the plan/fact numbers, balances, turnover, product availability level, and lost sales during the campaign.
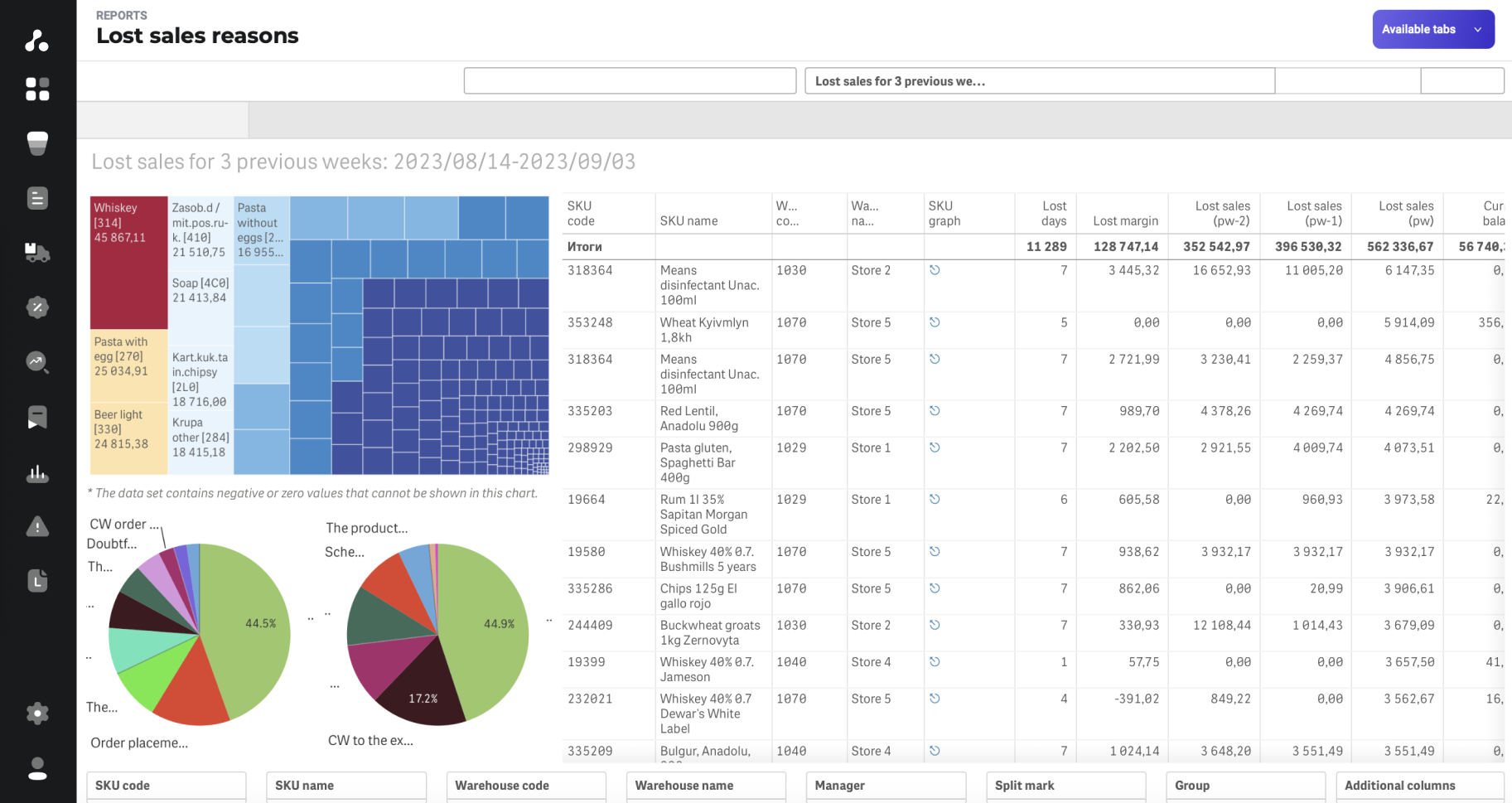
-
A flexible BI tool based on the Qlik Sense platform
-
40+ reports to analyze the efficiency of inventory management
Among them are ABC(D) + XYZ assortment analytics, inventory availability and turnover, reasons for lost sales, supplier service level, effectiveness of promotional activities, analysis of overstocks, and many others.
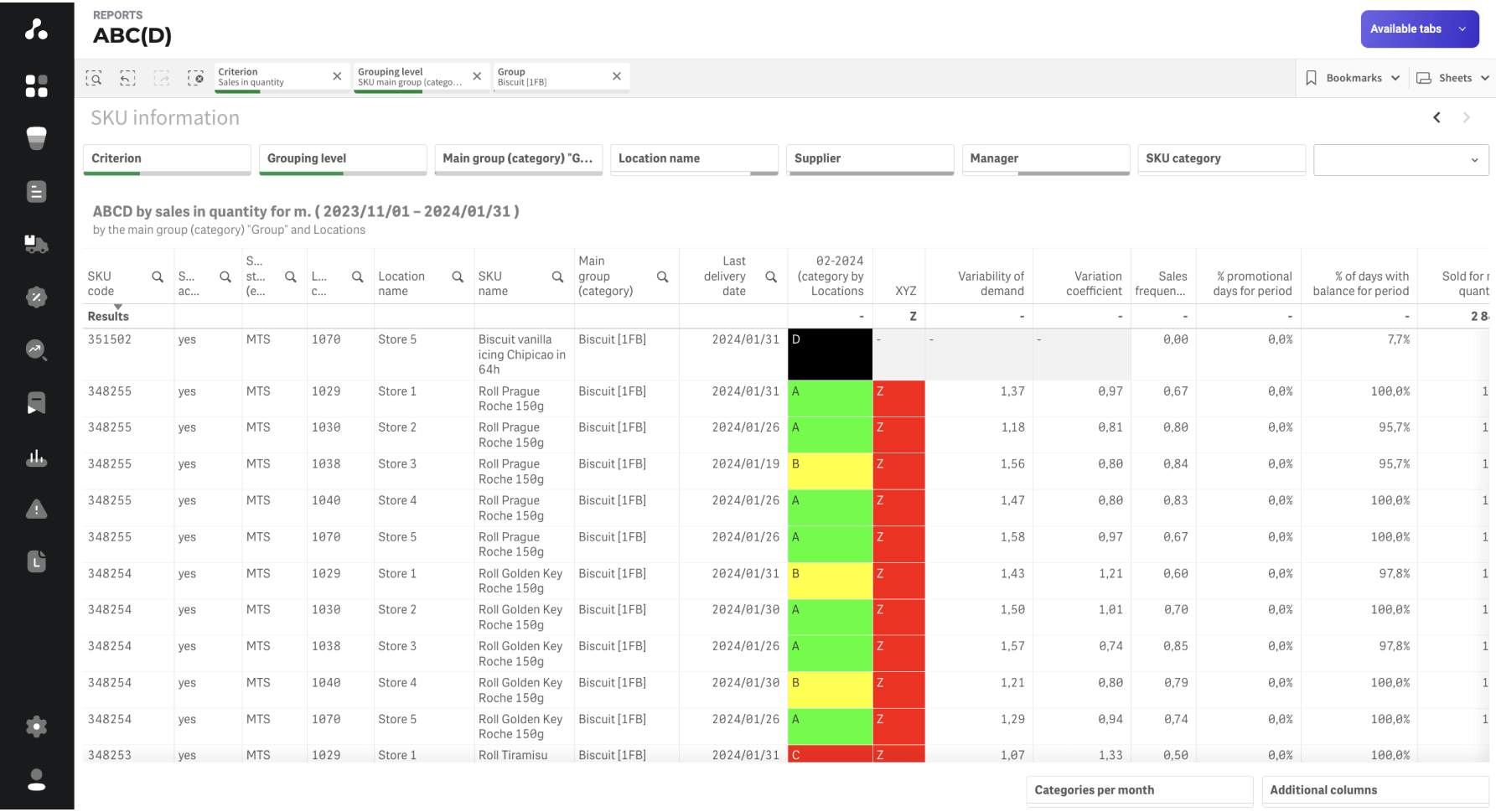
-
Demand forecasting for new products
The system automatically forecasts demand and generates the first order based on historical sales data for analogs, substitutes, or groups of products with similar characteristics.
-
Withdrawal of an item from the assortment
Automatically changes the status of goods at different levels of the supply chain depending on the balances.
The implementation stages
Advantages of working with us
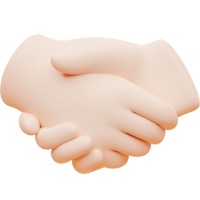
We are always by your side
We guarantee support, assistance and consultations at all stages of our cooperation.
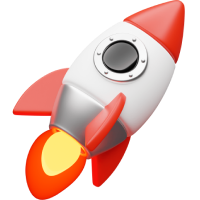
Continuous Improvement
We actively implement innovations in the system and respond to our clients' suggestions.
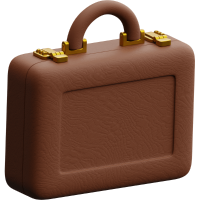
Proven Track Record
With over 500 successful implementations, we have earned our clients' trust.