Управление производством продукции по TOC
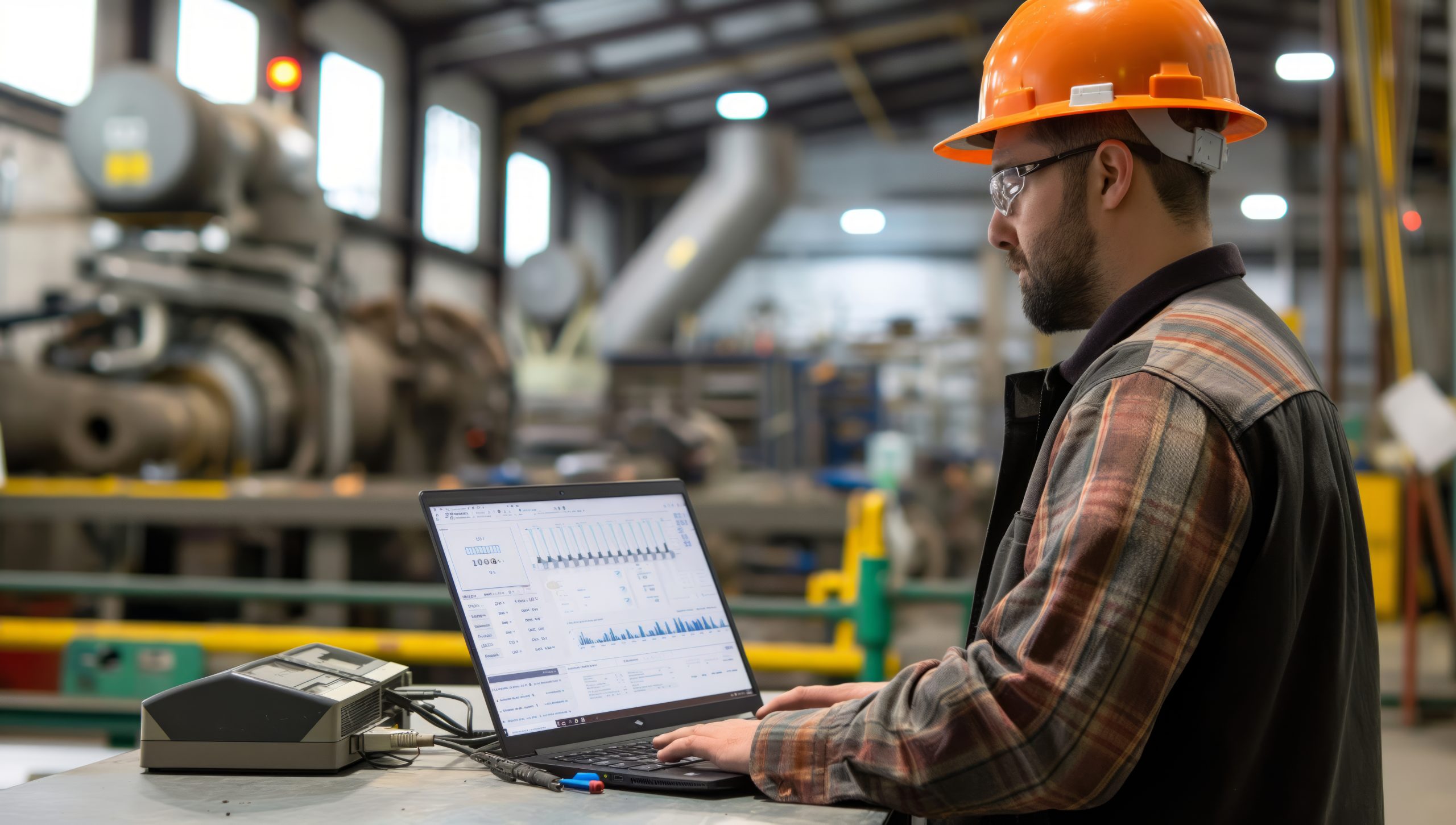
Содержание статьи:
Рассматривая управление производством продукции по TOC, мы в первую очередь будем говорить об управлении запасами и их потоками по методологии Теории Ограничений, т.е. о производственной логистике.
Избытки или выпадение запасов на производстве более критично, чем в обычной логистике в связи с тем, что каждый артикул является составляющей какого-то изделия. И если не будет хватать хотя бы одной детали, то и изделие не будет готово. Помимо наличия всех комплектующих важно правильно выстроить поток изделий в процессе выполнения операций. В этой статье будет рассматриваться ход и результаты одного проекта по внедрению инструментов Теории Ограничений для управления производственными потоками.
Проект был выполнен для производственной компании – изготовителя мебели под заказ. В ассортименте компании порядка 1500 готовых изделий. Изделия комплектуются из огромного количества деталей, которые проходят определенные стадии обработки.
Рассмотрим процесс движения заказа клиента:
- Клиент звонит в компанию и делает заказ
- Заказ передается в конструкторский отдел, который работает над заказом и делает чертежи будущего изделия
- Заказ передается в производственный цех
- Попав в производственный цех, изделие и комплектующие к нему проходят различные этапы производства, обработки, сборки и т.д. (см. рис)
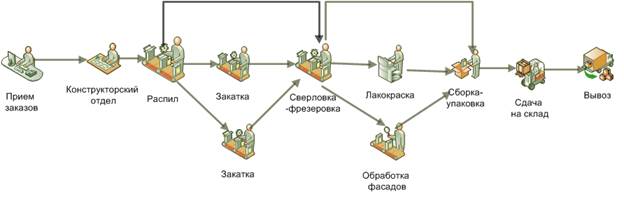
Управление производством продукции по Теории ограничений. Ход проекта
На первом этапе внедрения управления производством продукции по Теории ограничений мы сгруппировали каждый ресурс по участкам, сходным по операциям. Далее, для каждой комплектующей изделия описали маршрут обработки:
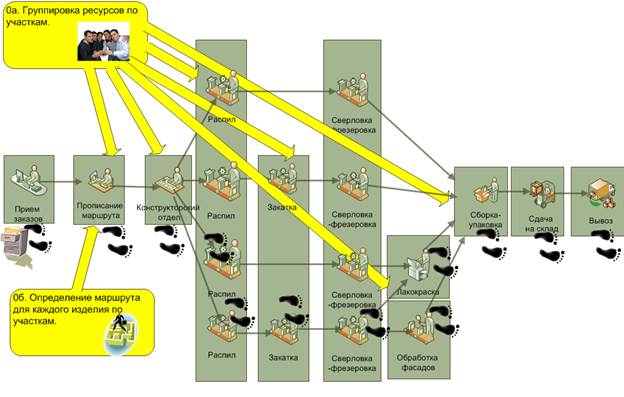
Получили набор из нескольких маршрутов для каждой детали. Далее мы оценивали все участки с точки зрения производительности с учетом рабочей силы на конкретном участке. Эта операция необходима для того, чтобы выявить узкое горлышко в системе – участки с минимальной мощностью (производительностью). Бутылочным горлышком оказался этап сверловка-фрезеровка, его производительность была самая низкая. Производительность остальных ресурсов была выше на 20-25 %.
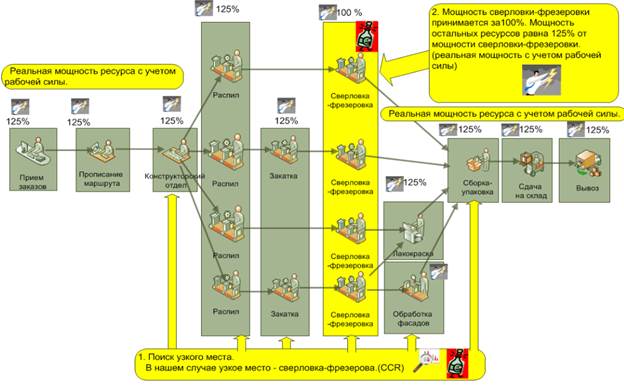
Буфер в управлении производством продукции
Далее мы определили время буфера. Для производства продукции буфер – это время выполнения заказа от первого до последнего ресурса. Готовая продукция может состоять из групп деталей сходных в обработке. К примеру, шкаф с крашеными дверками (фасадами) состоял из двух основных групп элементов или групп элементов со сходными маршрутами:
- Детали, проходящие по маршруту «порезка-закатка-сверловка-фрезеровка», – это буфер ДСП
- Детали, требующие порезки-закатки-сверловки-фрезеровки-покраски, – это буфер МДФ
Далее эти две группы деталей встречались на сборке, при этом скорость выполнения этих групп деталей разная. Детали первого буфера МДФ выполнялись дольше, т.к. для них требовалась покраска и сушка, что более длительно, чем распиловка и фрезеровка в случае с буфером ДСП.
В связи с этим, буфер ДСП был короче, чем МДФ. Время буфера считается так: Фактическое время выполнения среднего заказа деленное на два. В нашем проекте буфер ДСП – 4 дня, буфер МДФ – 6 дней.
Буфер рассчитали для всех групп деталей, которые составляли изделия. Определенные модели шкафов имели 3 буфера и, соответственно, три группы деталей: ДСП, МДФ и ротанг (дополнительная обработка фасадов – вроде вставки стекла или элементов интерьера). Получается, что буфер – это время выполнения определенной группы деталей по какому-либо маршруту.
Следующий шаг – запускаем в производство группы деталей только за время их буфера. В результате мы снизили уровень «незавершенки» в производстве. Также, была установлена система управления производственной логистикой, в которой при вводе заказа в систему, он автоматически разбивался на буферы (маршруты) групп деталей для этого заказа. И по заданному алгоритму детали запускались в производство.
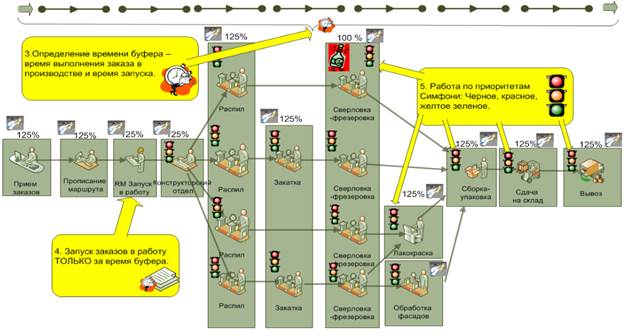
Для управления буферами также была введена система «светофоров». Например, буфер ДСП – 6 дней. С момента запуска в производство первые два дня (или 1/3 буфера) деталь находится в зеленой зоне. Когда с момента запуска этой детали прошло 2-4 дня – это уже зона желтого цвета (Желтый цвет буфера 2-4-ый день, или 2/3 буфера). Если деталь все еще находится в производстве на 4-6-ый день (3/3 буфера), то она попадает в красную зону. Деталь, находящаяся в производстве свыше буфера, – черный цвет:
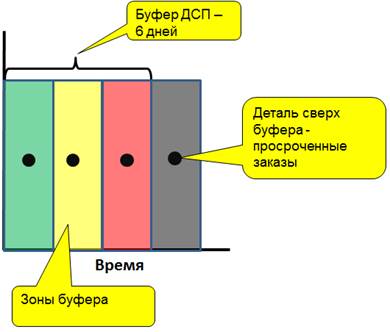
Благодаря такой системе цветовой индикации, производство получало понятные приоритеты для выполнения заказа. В первую очередь брать в работу заказы с черным цветом (если таковые были), затем красные и желтые. Таким образом, все участки на производстве видели в своих сменных заданиях цвет изделия для выполнения.
Управление производством продукции по ТОС позволило повысить производительность завода на 25%
Результаты следующего этапа преобразований – повышение производительности всего завода на 25 %. Мы начали работать с бутылочным горлышком, которым являлась сверловка-фрезеровка. Мы запретили перекуры на узком месте, наняли еще одного рабочего для работы во время обеда, сократили время пересменки. Это позволило к ресурсу времени узкого места добавить еще около 2-х часов, т.е. 25 % мощности. Заметьте, мощности не только бутылочного горлышка, но и всего завода. Наращивая производительность узкого места, мы повышаем производительность всего завода, т.к. мощность узкого звена – это мощность всей цепи.
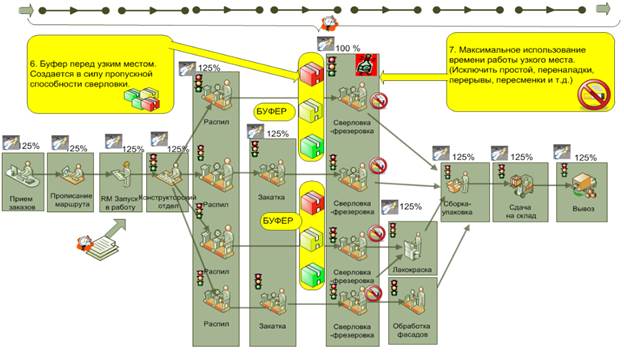
Мощности производству добавил еще и контроль качества, который был введен перед сверловкой-фрезеровкой. Теперь узкое место обрабатывало исключительно качественные детали и не тратило время на исправление брака.
На следующем этапе необходимо было заполнить всю производственную цепь заказами в соответствии с загрузкой бутылочного горлышка. Так как сверловка-фрезеровка в состоянии произвести определенное количество деталей за смену, то необходимо загружать ее до 100 % использования. Оставшиеся ресурсы же могут простаивать, т.е. если загрузить все ресурсы на 100%, мы не только не увеличим производительность, но еще и увеличим уровень «незавершенки». Итак, зная, сколько может обработать деталей бутылочное горлышко, столько деталей мы и даем заводу. Дело еще в том, что часть заказов скопится перед сверловкой-фрезеровкой из-за того, что остальные ресурсы работают быстрее этого участка.
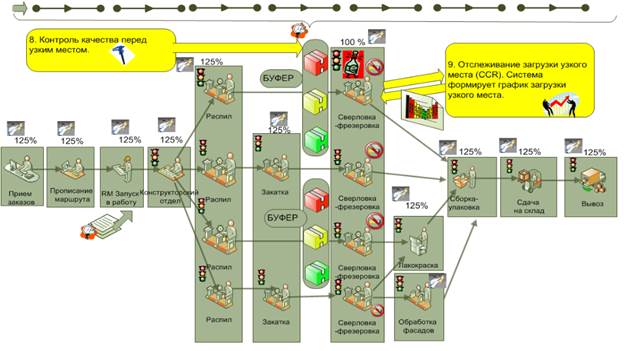
Еще одним нововведением был запуск системы, которая принимает заказы на основании графика загрузки узкого места. Благодаря преобразованиям, мы смогли добиться одного из самых важных для производственной компании показателей – гарантировать клиентам выполнение заказов в срок практически в 100% случаев.
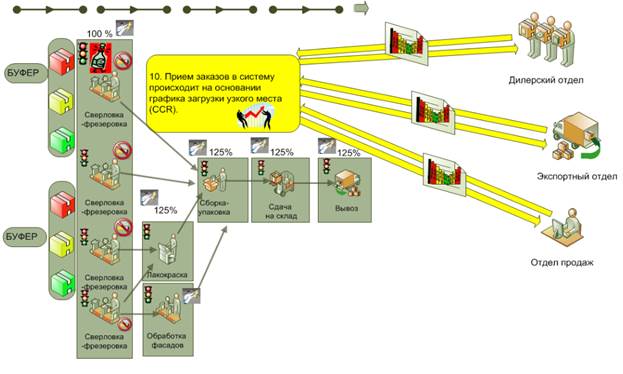
Сменное задание для каждого участка выглядит так:
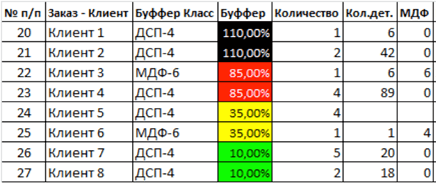
Чтобы вся система заработала, нужно еще и перестроить «мозги» рабочим. Мы изменили мотивацию сотрудникам и вместо выработки по деталям ввели мотивацию на количество черных и красных заказов. Таким образом, мы стимулировали работников снижать долю опаздывающих заказов. Также был запущен процесс непрерывных улучшений. Но об этом в следующих статьях.