Управление запасами на производстве по Demand Driven
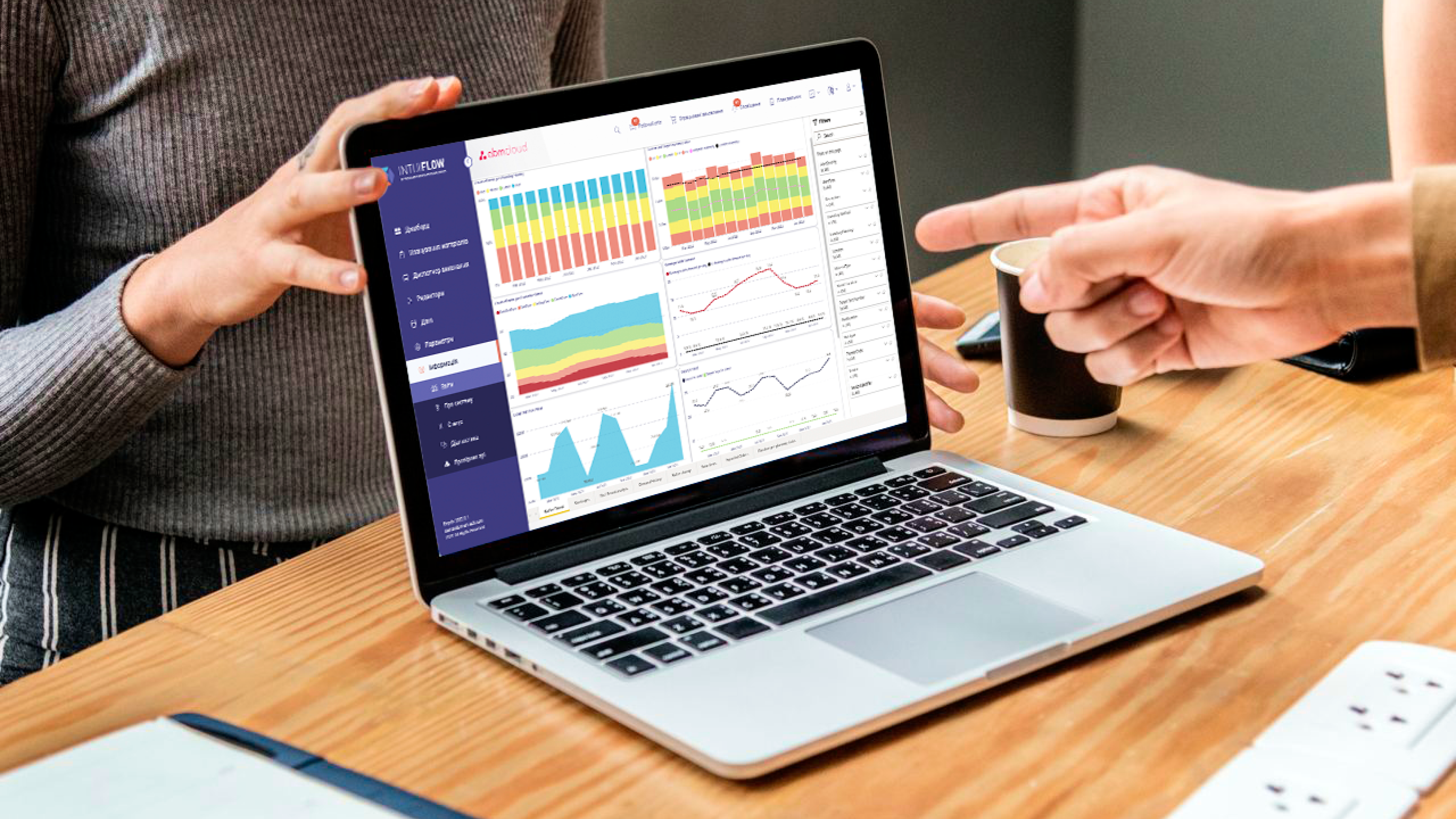
Содержание статьи:
Прибыльное управление запасами на производстве с Demand Driven – именно так звучала тема вебинара, на котором впервые для стран СНГ была представлена инновационная методология Demand Driven! Эксперты ABM Cloud рассказали, как с помощью современных инструментов сократить объемы запасов и повысить сервис левел.
Кратко рассмотрим основные аспекты в управлении запасами на производстве по методологии Demand Driven, которые были раскрыты на вебинаре.
Спикер начал свой доклад с проблематики производственных компаний, отметив, что менеджеры утопают в попытках синхронизировать то, что «есть по факту», с тем, что «необходимо». И зачастую это делают просто в Excel.
Какова статистика использования компаниями Excel в управлении запасами?
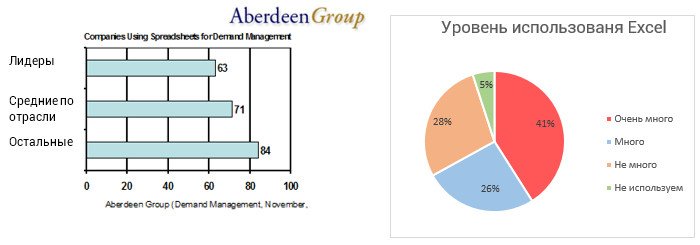
Исследования компании Aberdeen Group показали, что 63% лидеров рынка используют для управления запасами Excel. Если говорить о средних компаниях по отрасли – это 71%. Прочие компании – 84%.
Обратите внимание, всего лишь 5% компаний не используют Excel в целях управления запасами. Все остальные, как мы видим, используют Excel в той или иной мере.
Управление запасами на производстве: Новые вызовы – старые методы и инструменты
В чем же причина, неужели современные системы планирования не работают? Все дело в том, что новые вызовы, стоящие перед компаниями, не позволяют в полной мере пользоваться той функциональностью, которая заложена в системах.
Рассмотрим главные вызовы, с которым столкнулось производство
- Сроки выполнения заказа сокращаются. Клиенты не хотят ждать. Если компания не может предложить меньший срок, его предложат конкуренты и компания потеряет заказчика.
- Продуктовые линейки становятся шире, а товары сложнее. Для сравнения, если в 60-е гг компания Colgate и Crest конкурировали с одним видом зубной пасты, то на сегодняшний день у Colgate их 20, а у Crest их около Это уже другой уровень конкуренции.
- Долгие сроки поставки сырья/комплектующих. Еще 10 лет назад участники цепи поставок почти всегда располагались в одной стране или хотя бы на одном континенте. На сегодняшний день это не так, много сырья/комплектующих ввозится из Китая, Индии или других стран. Количество участников в цепи поставки увеличивается, что делает ее более сложной и менее гибкой.
- Сокращение жизненных циклов товаров. Если раньше модель телефона могла существовать 5 лет, то на сегодняшний день срок жизни модели телефона составляет не более 9 месяцев, после чего компания должна выпустить следующую модель. В противном случае это сделают конкуренты и заказчик перейдет не просто на новую модель, он перейдет на новый бренд.
- Цель – низкие запасы на производстве. Привлечение денежных средств – не всегда простая задача, в то время, как деньги в Вашей компании есть всегда, и они в большей мере заморожены в запасах. Если правильно поставить цели и воспользоваться современными системами для эффективного управления запасами производства, то можно одновременно снизить уровень запасов и сохранить или даже повысить сервис левел.
- Добавим к этому списку еще и неточность прогнозов. Неточность прогноза и ненадежность поставщиков способствует эффекту кнута, а взаимозависимости внутри системы и фрагментарность информационных потоков передают и усиливают этот негативный эффект.
Эффект кнута в управлении запасами на производстве
Для того, чтобы рассмотреть эффект кнута достаточно взять 4 звена: Поставщик — Производитель — Дистрибьютор — Ритейлер.
Предположим, что на сегодняшний день покупателю нужно 10 единиц товара (спрос в районе 10). Ритейл, формируя заказы на дистрибьютора, заложит страховой запас и закажет 20 единиц товара.
Дистрибьютор, получив заказ на 20 единиц, заложит также и свой страховой запас, поскольку производитель не раз его подводил.
В итоге дистрибьютор закажет 30 единиц. Производитель заложит свой страховой запас и заказ поставщику будет составлять 50 единиц. Поставщик заложит свою страховку и получит в итоге товар.
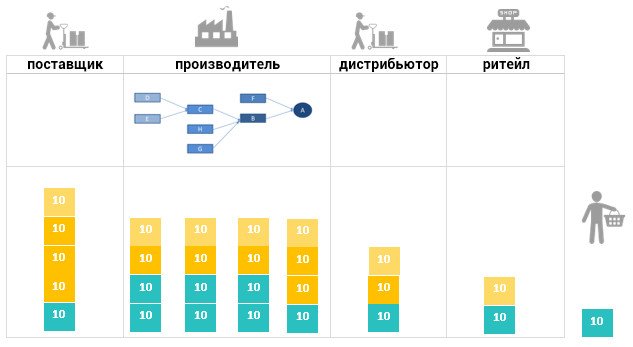
Теперь предположим, что одна комплектующая не доставлена. Но именно эта комплектующая лежит в основе большинства товаров, которые производит наш производитель. Все прекрасно понимают, если компания собирает компьютеры и не приехала хотя бы одна составляющая, то уже не имеет значения размер запаса прочих элементов (процессоров или мониторов). Отсутствие единой комплектующей не позволит ничего произвести. Производитель ничего не поставит дистрибьютору, ничего не получит ритейлер, а наш покупатель будет очень огорчен. Когда поставщик осознает всю ответственность, то в следующий раз закажет гораздо больше того товара, из-за отсутствия которого пострадали все. Каждое последующее звено поступит точно таким же образом.
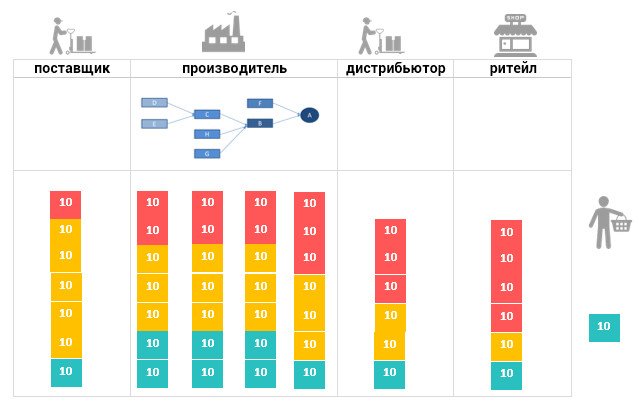
Все это время мы помним, что наш покупатель хочет купить всего лишь 10 единиц товара, не больше.
Что происходит дальше, когда каждое звено цепи поставок имеет запасов куда больше, чем нужно?
Понимая сложившуюся ситуацию с оверстоками, ритейлер ничего не закажет у дистрибьютора, тот в свою очередь ничего не закажет у производителя, а производитель ничего не закажет у поставщика.
В процессе управления запасами на производстве, эффект кнута повторяется неоднократно. Это явление имеет постоянных характер для выталкивающих систем. Чтобы в этом убедиться, вниманию аудитории был представлен реальный пример компании FMCG сферы.
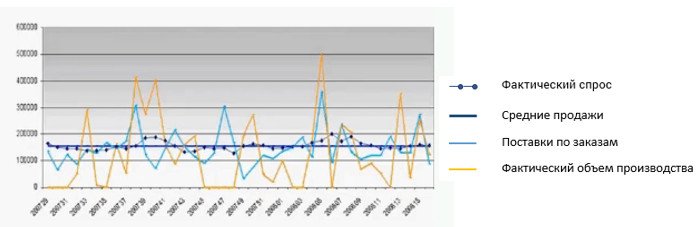
На графике мы видим, что в некоторых пиковых точках производство работало сверхурочно, но при этом есть промежутки простоя в несколько недель. И это для того, чтобы обеспечить, как это ни парадоксально, практически равномерный спрос, который колеблется в пределах 10%.
Продолжительное исследование этих и других проблем, связанных с управлением запасами в производстве, дало начало первым методологиям, которые были призваны преодолеть эффект кнута и построить систему вытягивания, а не выталкивания.
Это были методики Lean, TОC, 6 Sigma и прочие. Но те или иные методики в большей или меньшей степени применимы для разных отраслей. Методика Lean хорошо себя зарекомендовала в машиностроении, но не даст похожего эффекта на предприятиях с высокой вариабельностью спроса.
И в итоге возник вопрос: возможно ли доработать уже существующие методики и сделать их более универсальными? Практика показала, что возможно. Demand Driven MRP. Революционная концепция управления запасами на производстве.
DDMRP — многоуровневое решение для планирования и обеспечения прозрачности выполнения работ по управлению сырьем и готовой продукцией в современных рыночных условиях. Методология DDMRP объединила в себе методики:
- Material Requirements Planning (MRP)
- Distribution Requirements Planning (DRP)
- Lean
- 6 Sigma
- Theory of Constraints
- Innovation
Чем же отличается DDMRP от прочих методик?
- Отсоединение спроса от поставок
- Сжатие времени реакции системы
- Уменьшение влияния вариабельности на систему.
- И самое главное – переход к планированию на основании реальных продаж.