Внедрение автоматизированной системы управления производственными запасами в «KORMOTECH»
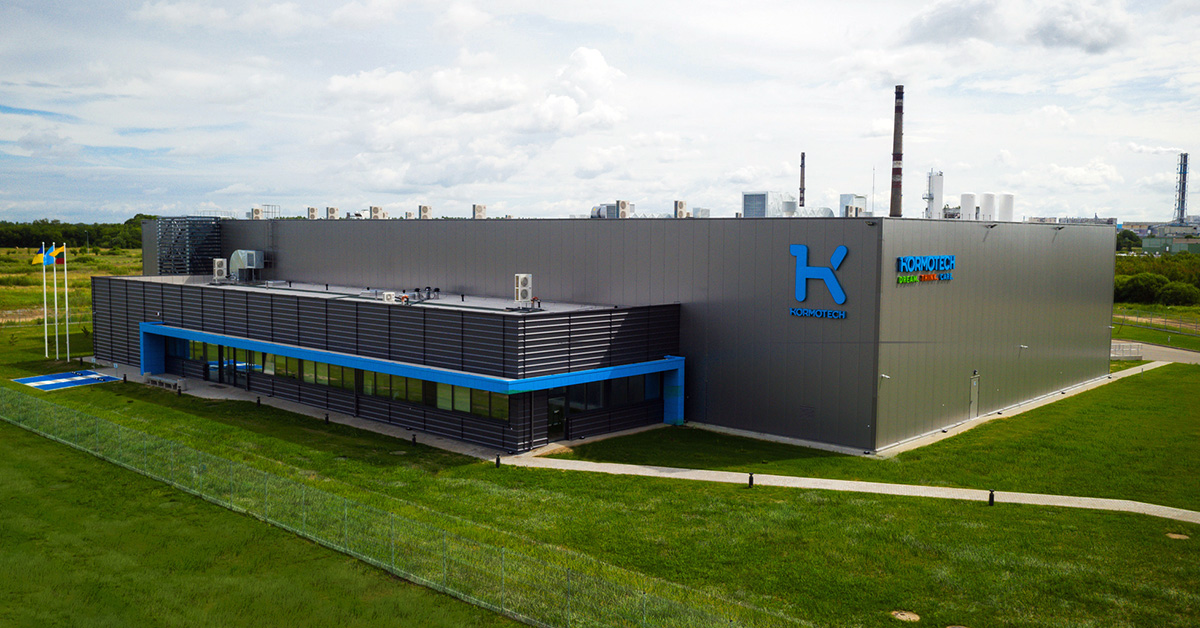
Справка о бизнесе клиента
«KORMOTECH» — производитель сухих и влажных кормов для домашних животных. Производственные мощности компании составляют 16000 тонн влажных и 30000 тонн сухих кормов в год. При этом, производственные объекты соответствуют всем европейским стандартам безопасности и качества продуктов питания.
Компания производит три вида кормов стандарт-класс (ТМ «Гав!», «Мяу!»), Премиум (ТМ «CLUB4PAWS» или «Клуб 4 лапы») и суперпремиальний (ТМ «Optimeal»). Продукция компании продается, используя разные каналы сбыта. Клиентами компании являются все крупнейшие супермаркеты, зоомагазины, продуктовые магазины, питомники животных и, конечно, ветеринары. 20% продукции экспортируется в 18 стран, в частности, во Францию, Польшу, Румынию, республики Молдова и Тунис, Объединенные Арабские Эмираты, Венгрию, Латвию, Литву, Эстонию и Нидерланды.
Компания «KORMOTECH» сертифицирована по стандартам ISO 22000, FSSC 22000, AFCO (США) и сегодня вводит программу 5S (от американского «sustainability» — бережливое производство). Каждое сырье и рецептура имеют спецификацию, согласно которой проходит входной/выходной контроль. Каждую партию сырья сотрудник отдела качества (в компании их 16) сверяет со спецификацией. Если обнаружены отклонения — партию возвращают.
Предпосылки проекта
Предпроектная диагностика компании показала, что склады сырья переполнены запасами, но при этом постоянно возникает дефицит материалов, приводящий к невыполнению плана производства. Аналогичная ситуация обстоит с запасами готовой продукции на распределительном центре. В связи с этим, сотрудники компании видели два ложных направления усовершенствования текущей системы: путем расширения текущих складских площадей и за счет усовершенствования алгоритма прогнозирования.
Как происходило планирование на момент предпроектной проверки компании:
- Все заказы формировались менеджерами в полуавтоматическом режиме, что увеличивало трудозатраты и снижало качество заказов. Каждый менеджер управлял большим перечнем SKU в Excel, основываясь на месячном плане продаж и спецификациях, что что влекло за собой высокий процент ошибок.
- Взаимозаменяемость сотрудников была невозможна из-за отсутствия четкой формализации условий закупок. Каждый менеджер «помнит» условия работы со своими поставщиками и использовал свой Excel/блокнот, где отмечал важную для него информацию. Организация теряла адаптивность к кадровым и функциональным изменениям, что сказывалось на стабильности и бесперебойности производства. Кроме того, разрозненная архитектура системы требовала высоких трудозатрат на поддержание, поиск и управление информацией.
- Отсутствие целостной формализованной системы управления запасами и приоритетов при планировании (что, в какой последовательности и в каких объемах необходимо производить) вело к неритмичной загрузке мощностей, в результате снижалась доступность продукции, мощности использовались неэффективно.
- Отсутствовали инструмент мониторинга качества выполнения заказов поставщиками сырья, возможность быстрого анализа изменений уровня товарных запасов в точках хранения и мониторинга ситуации по цепи поставок в целом. Реальный масштаб проблем оставался неизвестен.
- Комплектующие, сырье и материалы часто недоступны (недостаточное количество, недопоставка или срок поставки длиннее горизонта планирования готовой продукции), что влекло за собой отсутствие продукции на складах и упущенные продажи.
- Желание перестраховываться для максимального удовлетворения спроса вело к чрезмерному уровню запасов по всему ассортименту. Это увеличивало стоимость хранения запасов и расходы на обслуживание, а также замораживало оборотные средства и снижало оборачиваемость.
- Качество управления запасами ограничено свойствами текущей системы, качеством и периодичностью прогнозирования. Даже если все комплектующие были в наличии, и было произведено все, что запланировано, всегда существовал риск, что реальные потребности рынка могут существенно отличаться от первоначального плана.
Такой подход к формированию заказов требовал больших временных, ресурсных затрат и порождал неизбежные ошибки, связанные с человеческим фактором. Вышеназванные причины негативно отражались на качестве управления товарными запасами, и, как следствие, на эффективности работы производства.
Для полноценного и комплексного управления запасами компании особенно важно иметь удобный инструмент, позволяющий оценивать размер и анализировать причины излишков (overstocks) и упущенных продаж (out-of-stocks).
Для обеспечения наличия необходимого сырья, полуфабрикатов и готовой продукции, а также упрощения планирования, производством была выбрана система управления запасами Intuiflow, которая работает по методологии Demand Driven MRP.
Причины выбора Intuiflow
При выборе решения по управлению запасами для производства, менеджмент компании KORMOTECH рассматривал программные продукты, которые можно разделить на 3 типа:
- Выталкивающие, т.е. основанные на прогнозе
- Вытягивающие, реагирующие на реальный спрос
- Гибридные, включающие в себя синтез преимуществ двух предыдущих систем
Поскольку выталкивающие системы ограничены сложностью и не точностью прогнозирования, а вытягивающие системы недостаточно или излишне реагируют на изменения в спросе, стало очевидным решение в пользу Intuiflow компании ABM Cloud.
Intuiflow качественно отличается от существующих систем уникальной методологией управления запасами для производства и форматом ее эксплуатации. В основе системы лежит методология Demand Driven MRP (планирование потребности в материалах на основании реального спроса), которая помогает обеспечить постоянное наличие товара при минимальных запасах в системе. Методология основывается на базовых принципах MRP, Бережливого производства, Теорий ограничений системы и Шести сигм, а также существенного блока инноваций.
Помимо методологического преимущества, решение Intuiflow имеет ряд дополнительных плюсов:
- Облачная (SaaS) модель работы системы не требует дополнительных инвестиций в оборудование (сервера) и поддержку системы. Оплата производится в виде ежемесячных арендных платежей по факту использования системы.
- Визуализация проблемных зон и текущего положения дел даёт возможность быстро оценить ситуацию и принять соответствующие меры. Отчётность, представленная в системе, позволяет менеджерам быстрее и лучше ориентироваться в ассортименте и управлять запасами, а руководству контролировать ситуацию и держать руку на пульсе.
- Вся цепь поставок в одной системе. От закупки сырья до управления запасами в дистрибуционной сети, где каждое размещение запаса — это стратегическое решение, которое обеспечивает сокращение скорости реакции, повышение надежности цепи поставок, а главное, обеспечивает рост ROI.
- Обучение пользователей начинается с изучения передовой методологии управления цепями поставок (DDMRP), что существенно повышает общий уровень компетенций сотрудников и создает надежный фундамент для дальнейшего развития компании.
- Сопровождение осуществляется службой технической поддержки, предоставляющие технические и методологические консультации на постоянной основе в режиме реального времени.
- Отработанная технология внедрения позволяет зафиксировать этапы внедрения, рассмотреть существующие бизнес-процессы и при необходимости разработать план их изменения. Сама система не требует дополнительного программирования или длительной трудоёмкой настройки.
Описание проекта
Реализация проекта предполагала 3 условных этапа:
- Подготовка к запуску проекта: диагностика текущей деятельности компании, определение «узких мест» в управлении производственными запасами, фиксация текущего состояния цепи поставок.
- Запуск: внедрение алгоритмов DDMRP, оптимизация и автоматизация управления производственными запасами).
- Сопровождение: обеспечение методологической и технической поддержкой.
Перед началом проекта были сформулированы цели, которых предстояло достичь:
- Сократить запасы сырья и готовой продукции
- Обеспечить постоянное наличие необходимой продукции для удовлетворения входящего спроса
- Стандартизировать, визуализировать и автоматизировать планирование производства и управление запасами по цепи поставок
Проект начат с обучения проектной команды KORMOTECH методологии DDMRP. Параллельно консультанты ABM Cloud приступили к аудиту текущих бизнес-процессов, напрямую связанных с цепью поставок. Ниже представлена укрупненная схема цепи поставок KORMOTECH:
Процесс внедрения на всех этапах сопровождался обучением пользователей, которые будут в дальнейшем работать с программой:
- семинар-тренинг по методологии управления запасами по Demand Driven MRP
- обучение пользователей работе с программой Intuiflow, ее алгоритмами и настройками
- обучение пользователей работе с отчетностью системы
Проектные работы
После первичного анализа цепи поставок и обучения проектной команды новой методологии управления цепями поставок – DDMRP, следующим шагом стала полная формализация, очистка и систематизация данных.
- Формы данных в ERP. Разработали форму для ведения всех параметров заказа по поставщикам в ERP системе. Согласовали бизнес процесс по внесению и поддержке данных, определили ответственных и систему контроля. Определили реальные и достаточно детальные условия по работе с поставщиками Lead Time, MOQ, цикличность заказа и т.д.
- Подготовили данные. Прошли множество итераций фильтрации, анализа и очистки данных по ключевым элементам цепи поставок.
- Автоматизировали обмен данными. Разработали, протестировали и успешно внедрили автоматический обмен данными между ERP системой клиента и программой Intuiflow.
- Автоматизировали заказы сырья и планирование производства. С помощью Intuiflow автоматизировали прежде сложные, трудоемкие и ненадежные ручные расчеты, тем самым создав сотрудникам дополнительные возможности для развития своих управленческих качеств.
- Собрали все данные в одной базе. Это помогло создать фундамент для дальнейшего стабильного роста и развития компании.
- Внедрили новую систему отчетности. Система управления запасами стала эффективной и прозрачной для анализа. Открылись новые возможности постоянного совершенствования (Kaizen).
- Существенно повысили компетенции. Теперь сотрудники могут оценить результаты своих действий, используя разные критерии оценки: надежность, эффективность и финансовые результаты всей компании, а не только своего отдела.
На этапе разработки и моделирования определили, где есть необходимость держать запас, какими должны быть профили и уровни буферов (буфер позволяет видеть картину потребляемых и формируемых запасов).
Буфер имеет три основных свойства:
- Погашает вариабельность спроса
- Сокращает время до поставки
- Улучшает Return On Investments (ROI)
На практике не просто принять решение, по какой позиции стоит держать буфер (запас), а по какой нет. И порой кажется: если у нас есть план, нет смысла держать в запасе дорогое сырье, ведь, когда появится необходимость, поставщик нам сразу его подвезет. Но к чему может привести такой подход в итоге?
План
Что выгоднее: хранить дорогое сырье, которое редко используется, либо закупать сырье ситуативно, в зависимости от потребности в производстве новой продукции?
На первый взгляд может показаться, что закупка сырья к дате производства экономит деньги и складские площади, а также не замораживает оборотный капитал в запасах. Чтобы понять, что действительно экономит деньги компании, важно смотреть не на показатели отделов, а на результаты предприятия в целом.
На практике оказалось, что размещение «правильного» буфера по одной номенклатурной позиции помогло сократить цикл планирования на 9 дней (уменьшился срок от выявления потребности в готовой продукции к моменту его производства с 17 до 8 дней). Срок производства при условии наличия сырья – 8 дней. Компании удалось сократить запас готовой продукции, тем самым высвободив денежные средства в размере 28 319 грн. И что важно, удалось повысить показатель доступности запаса готовой продукции. Расчеты эффекта размещения «правильного» запаса по одной номенклатурной позиции мы можем видеть в таблицах (Рис. 1).
Пример расчета эффекта устранения логической ловушки «классической системы управления запасами» – «закупка дорогостоящего сырья в момент возникновения потребности».
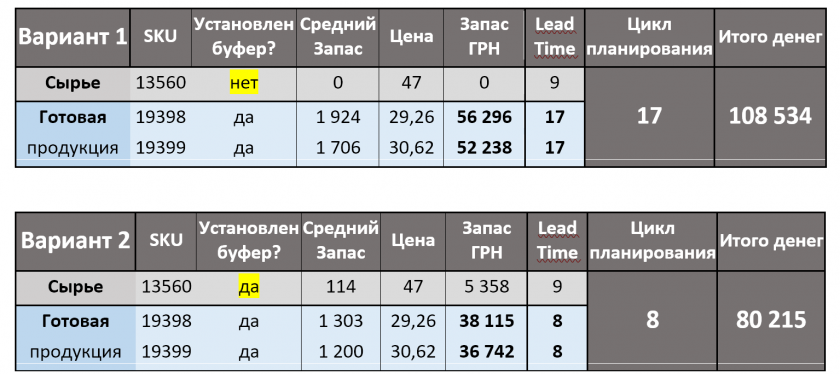
Рис. 1– Результат размещения «правильного» запаса по одной номенклатурной позиции
Себестоимость
Больше сырья по выгодной цене – лучше для компании. В среде производства существует еще один способ сэкономить – закупить оптимальную партию сырья по самым выгодным ценам и условиям. Но как выглядит ситуация на самом деле?
Когда запасы закупаются по очень выгодной цене, но без реальной необходимости, это влечет за собой негативные последствия:
- временно заморожены оборотные средства компании
- со временем запасы могут испортиться, морально устареть, либо вообще перестанут использоваться в производстве, что означает прямые потери для предприятия

Рис. 4 – Аналитика. Движение остатков по SKU
Из примера выше (Рис. 4) видно, что была закуплена «оптимальная» партия, и от момента запуска системы количество на остатке практически не изменилось. Себестоимость единицы – 1,18 грн. Мы заморозили на неопределенный срок 1,18*516 650 = 609 647 грн.
Решение, которое было принято в ходе проекта: проанализировать индекс потока, как по сырью, так и по готовой продукции, с целью нахождения «хвостов» и возможных способов сокращения «оптимальных-минимальных» партий.
Для предприятия гораздо выгоднее договориться с поставщиками о меньших минимальных партиях поставок, даже если для этого необходимо заплатить дороже за единицу сырья. Еще лучше – найти общие интересы и понять, как можно помочь поставщику поставлять отдельные SKU меньшими партиями, не доплачивая при этом, а решая какую-то его потребность.
В результате проведенной работы было выявлено, что решение еще одной сопутствующей проблемы – нехватки складских площадей, кроется не в изменении целевых уровней запасов, а в пересмотре условий закупок сырья. Обсуждая условия поставки, необходимо одновременно обращать внимание на три ключевые цели: купить дешевле, купить меньше, получить быстрее.
Оптимальные партии
На производстве была определена оптимальная партия в 3 т, и она действительно отвечала критериям минимизации производственных потерь.
Парадокс локальной эффективности повторяется аналогично предыдущим примерам. Чем более эффективно производство, тем, как правило, менее эффективно предприятие в целом.
Как было до проекта
Производство максимально эффективно и с минимальными затратами производило 3 т готового продукта и отгружало на РЦ. С РЦ эта партия отгружалась максимум полтора года, так как дальше истекал срок годности продукта. Все что оставалось (около половины произведенной партии) утилизировалось, а это – прямые потери. При этом, если на РЦ не было остатка, производство продолжало производить «оптимальные» по затратам партии — в количестве 3 т. Серьезность этой ситуации вы можете оценить на графике «до DDRMP» и результаты работы команды по балансировке потока на графике «после».
По оси ординат расположилось количество SKU, по оси абсцисс – количество дней, округленных до недели. Идея всей системы заключается в балансировке потока. Наилучшим индикатором сбалансированного потока являются минимальные партии.
Что мы сделали? Мы пересмотрели и сократили размер минимальных партий в несколько итераций, практически в два раза.
Управление целевыми уровнями запасов обычно влияет только на левую часть графика. Качество прогноза или совершенство системы управления запасами никак не повлияет на правую сторону графика. Мы еще раз убедились, что секрет не в сложной системе управления запасами, а в согласованности отдельных функций компании для достижения одной цели, а не локальных оптимумов.
Это лишь некоторые из многих примеров сдвига парадигмы в понимании управления производством и запасами. Именно благодаря пересмотру фундаментальных принципов, систематизацию, пересмотр бизнес процессов и, наконец, автоматизацию управления запасами удалось достичь поистине выдающихся результатов.
Команда клиента благодаря эффективному инструменту и глубокому пониманию текущих бизнес-процессов, смогла достичь высоких результатов при переходе с логики классической MRP на Demand Driven MRP. В процессе перехода на новую методологию произошел сдвиг парадигмы и переосмысление того, что действительно полезно для компании, а что является всего лишь локальной оптимизацией, вредящей компании.
Эффекты:
В компании «KORMOTECH» внедрена автоматизированная система управления производственными запасами Intuiflow. Используя систему, компания улучшила свою эффективность по ряду показателей. За период с апреля по сентябрь 2017 года были достигнуты следующие эффекты:
- Готовая продукция и полуфабрикаты: Повысился уровень наличия (Service Level) с 90 до 99%. Сократились запасы более чем на 45% при росте объемов производства на 40%!
- Сырье и упаковка: Сокращение излишков на 50%.
- Поток: Снижение колебаний продаж и производства более чем на 50%, что является хорошей основой для более эффективного операционного управления, надежного денежного потока и эффективности затрат.
Если первоначальные ожидания клиента ограничивались снижением запасов без ухудшения доступности через автоматизацию закупок и доработки части бизнес процессов, то в итоге результаты превзошли самые смелые ожидания.
Снижение запасов готовой продукции более чем на 45% при параллельном улучшении показателя доступности с 90 до 99%
Во-первых, исчезла необходимость аренды дополнительных складских площадей (до проекта были обращения руководства РЦ о временной остановке производства или об искусственном перемещении части запасов к дистрибьюторам, поскольку физически негде было хранить запасы. Теперь на том же РЦ полно места!). Это стало возможным благодаря снижению уровня излишних запасов более чем на 50% и устранению 2 ключевых драйверов их формирования: ошибки в прогнозах предыдущих периодов; производство «оптимальными» партиями.
Во-вторых, из-за длинного цикла планирования, сложно было предугадать будущие заказы клиентов, поэтому недельный план производства устаревал быстрее, чем его успевали реализовать, и только телефон помогал частично сглаживать углы. Теперь руководитель производства видит реальное состояние дел в цепи поставок в режиме реального времени и может безошибочно определить, что именно необходимо производить прямо сейчас для обеспечения потребности клиентов. Необходимость в недельном объемно-календарном планировании производства, как и во внешних «подсказках по телефону», полностью исчезла.
В-третьих, исчезла необходимость в анализе входящих заказов клиентов, теперь попадающих напрямую в учетную систему. И поскольку запаса достаточно для их удовлетворения, необходимость в «перестраховках» региональными менеджерами тоже отпала. Сами заказы клиентов, отчасти стали более стабильными, как и запасы у них, что также повлияло на общее увеличение уровня продаж.
Общий уровень запасов сырья не изменился при 40% росте потребности
Если посмотреть на график выше, не сложно заметить разницу между периодом «до» и текущими результатами компании. Не сложно представить, что для больших объемов производства необходимо больше сырья, но как показала практика, это не всегда так. На самом деле это первые результаты за счет первых шагов по систематизации данных и автоматизации управления запасами. Ключевой же результат по снижению запасов будет достигнут по результатам пересмотра договорных условий с поставщиками сырья в 2018 году, так как пока это ключевое ограничение эффективности в данном звене цепи.
Рост продаж и производства на 40%
Здесь отображен эффект синергии нескольких внутренних и внешних факторов разных элементов цепи поставок, над которыми работала вся проектная команда. Руководство компании приняло решение о расширении производственных мощностей в ближайшее полугодие, это создаст надежный фундамент для будущих, еще более впечатляющих результатов компании.
Более чем в 3 раза снизились колебания в объемах производства
После внедрения системы (правая стороны графика) диапазон колебаний снизился в 3 раза. Пропала необходимость планировать его на неделю вперед. Теперь производится только то, что необходимо прямо сейчас. Ранее необходимо было учесть сложности планирования объемов производства, определить точное время и необходимое количество выхода рабочих на смену, оптимизировать нагрузку оборудования и выполнения быстро меняющегося плана в следствии срочных звонков из отдела продаж. Результаты этих усилий видны в левой стороне графика, где время от времени объемы производства (синяя линия) существенно колеблются, что показывает очередность периодов сверх нагрузки и скрытого простоя. Излишним будет объяснять, что обе эти ситуации являются негативными для предприятия.
Результаты стали возможными благодаря сплоченной команде профессионалов, которая неустанно движется по намеченному курсу, учится и достигает поставленных целей. Благодарим команду проекта за плодотворную работу над общим результатом. Особая благодарность ТОР-менеджменту компании за активную позицию в вопросах внедрения, а также за открытость к изменениям и пересмотру принципов управления запасами, принятие решений, направленных на повышение эффективности работы компании.
Желаем компании «KORMOTECH» новых возможностей для развития и расширения бизнеса, достижения поставленных целей, успешных проектов и постоянного улучшения показателей деятельности. Как писал Joe Orlicky в первой книге о MRP, фактически ставшей новым стандартом в отрасли: «Самые выдающиеся результаты были достигнуты не теми, кто решил совершенствовать или автоматизировать существующие методики управления запасами, а теми, кто решил фундаментально пересмотреть логику работы их систем.»