Система управления производством
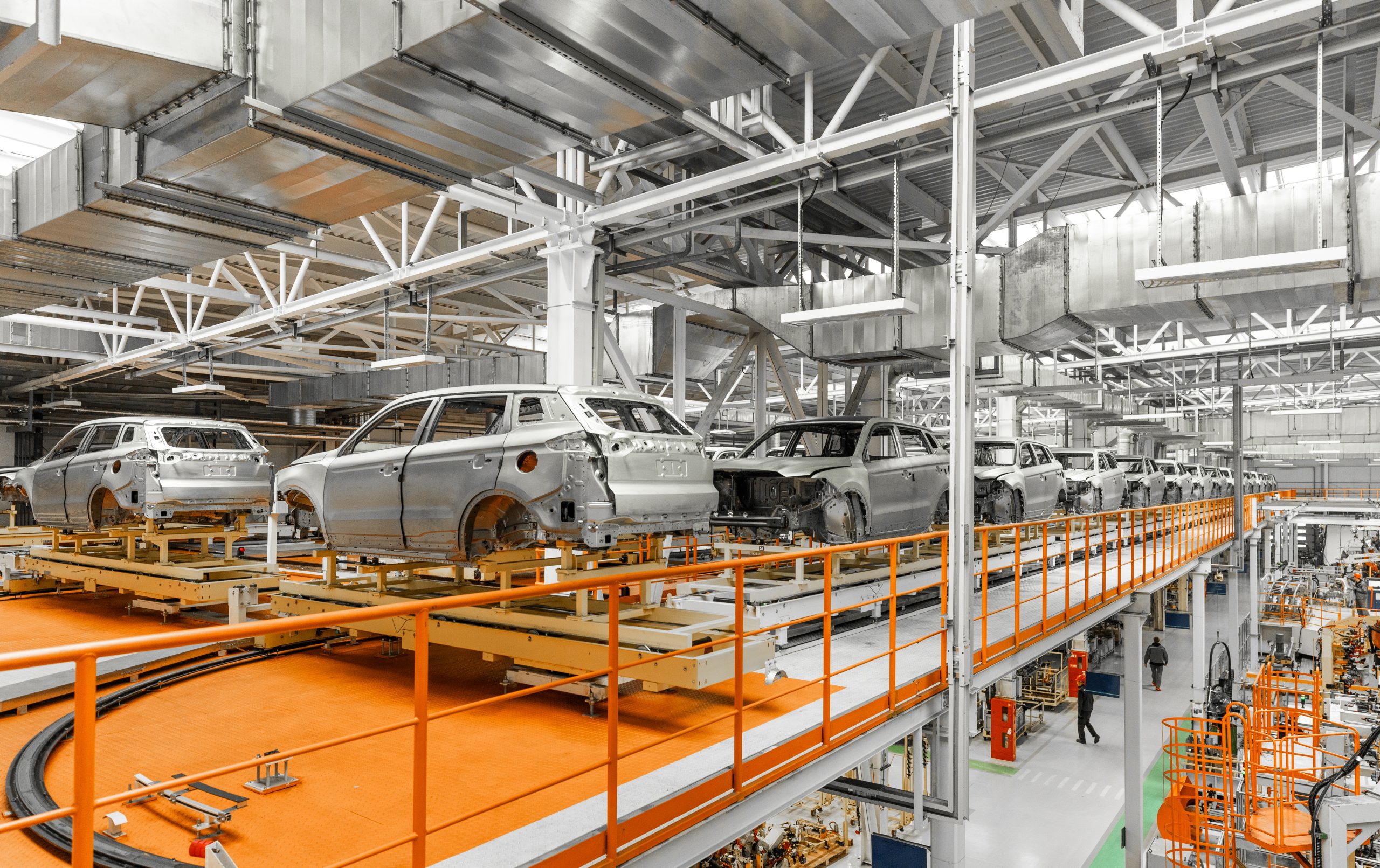
В чем состоит секрет успешного управления производством?
Система управления производством состоит из взаимосвязанных элементов, таких как технологии, производственные процессы, финансовые потоки, персонал и т.п. Во многих случаях модели производственного управления формируются, исходя из алгоритмов и особенностей используемых информационных технологий. Важно учитывать, что большинство применяемых систем материального планирования (MRP) были разработаны на основе подходов, принятых еще в 80-х годах ХХ века, не учитывают современных реалий и тех стремительных изменений, которые происходят в бизнесе.
Для современной экономической жизни характерны быстрые изменения трендов потребительских настроений, волатильность рынков и обострение конкуренции. В таких условиях совершенствование планирования ресурсов и выстраивание оптимальной структуры управления необходимы любой организации. Тем более, если речь идет о менеджменте в такой сложной сфере как производство.
Для своего развития предприятия должны иметь резервы для реагирования на возможный подъем спроса на товары и услуги. Одновременно следует считаться с постоянным увеличением стоимости ресурсов, понимая, что чрезмерные запасы становятся бременем.
Достижению таких целей компаний как динамичное развитие, гибкость, конкурентоспособность способствует внедрение методологии управления производством, ориентированной на фактический спрос.
В этом контексте интересно рассмотреть внедрение Demand Driven MRP в компании SATUERCA. С использованием подхода DDMRP удалось модернизировать систему управления производством на предприятии. Кейс был представлен на конференции по повышению эффективности управления в промышленности.
Система управления производством на предприятии: от поставщика до покупателя
Компания SATUERCA, основанная в 1967 году, занимается горизонтальной ковкой (детали в диапазоне от 50 г до 2 кг) и механической обработкой деталей. Готовые изделия поставляются, в основном, предприятиям автомобилестроения.
SATUERCA имеет два завода (общей площадью 15 тыс. кв. м.) в Испании и один — в Румынии. На производстве занято 135 человек. Компания обладает международными сертификатами ISO и OSHAS.
Среди клиентов:
Изготавливаемые детали:
Мощности предприятия позволяют производить горячую и полугорячую ковку стальных деталей в рамках полностью интегрированного производственного процесса — от сырья до готовых изделий.
Стадии производственного процесса компании:
- Горизонтальная ковка;
- Термообработка, включающая в себя отжиг, быстрое охлаждение и отпуск;
- Изотермический отжиг, Нормативизация;
- Дробеструйная обработка;
- Полный автоматический контроль (2D и 3D);
- Обработка поверхностей;
- Механическая обработка.
Технические характеристики выпускаемой продукции и потребляемого сырья:
- Ассортимент продукции предприятия состоит из 400 наименований готовых изделий
- Ковка проводится при температуре 1.200 ºC. Обрабатывается 100 — 150 деталей в минуту.
- Продолжительность полного технологического цикла: 5-10 дней.
- Сырьем является стальная круглая арматура диаметрами от 19 мм до 55 мм. Номенклатура сырья насчитывает 60 позиций, объем закупок составляет 23.000 т / год
Автоматизированная система управления производством
Основное назначение автоматизированной системы управления производством — обеспечить наличие всех необходимых ресурсов для выполнения производственной программы. В фокусе внимания АСУП – запасы, достаточное количество каждого из видов которых должно быть вовремя поставлено на определенную стадию технологического процесса.
При этом приоритетами является оптимизация уровня запасов, непрерывность и ритмичность выпуска товаров, надежность поставок и нивелирование негативного влияния колебаний спроса на производство. Такое программное решение состоит, как правило, из блоков автоматического расчета показателей наличия и необходимого пополнения материальных ресурсов, оперативного контроля, информационной поддержки менеджеров, комплексной аналитики.
Какие функции выполняет управление производством
Через MRP и АСУП осуществляются такие функции управления производством как организация, нормирование, планирование, координация, контроль и регулирование. При внедрении этих решений происходит регламентация взаимосвязей между всеми звеньями производственной цепи, разграничиваются зоны ответственности между участниками процессов.
Важной деталью является наличие алгоритмов реагирования на колебания спроса, задержки и простои, дефицит отдельных ресурсов. О потенциально критических ситуациях становится известно при контроле реальных показателей и сравнении их с расчетными нормативами. Поступающая информация становится основой решений по оперативному управлению, координации и регулированию.
Меры повышения эффективности планирования в управлении производством
Принятию решения о переходе к ориентированной на фактический спрос MRP предшествовали анализ всех элементов материально-технического обеспечения предприятия, определение основных проблем и узких мест на этом направлении. Подготовка также включала в себя исследование материальных и информационных потоков, оценку технического и экономического потенциала нововведений. Намечались пути совершенствования схем производственной кооперации с поставщиками.
Внедряя методологию DDMRP, компания преследовала следующие цели:
— устранить существенные расхождения между клиентскими прогнозами и реальными заказами;
— предотвратить задержки поставок сырья;
— прекратить возникновение постоянных вынужденных расходов консигнационных запасов.
Существовала объективная потребность в единой гибкой методологии, позволяющей менеджерам по планированию работать с полной и актуальной информацией по таким показателям как:
- Объем запасов;
- Поступление новых заказов на продукцию;
- Расчетные объемы закупки сырья;
- Контроль наличия сырья для выполнения принятых заказов;
- Выполняемые заказы.
Как выбрать систему автоматизации управления производством
Планирование поставок в компании вплоть до 2012 года проводилось вручную, основываясь на анализе, проводимом одним специалистом. В дальнейшем, для обработки информации по запасам использовался Excel.
С сентября 2013 года в компании применяется методология DDMRP с программным продуктом Intuiflow.
Современное промышленное предприятие представляет собой сложную систему, в которой возможна только автоматизированная обработка информации. Поэтому при реализации любой управленческой или производственной новинки необходимо применять соответствующую компьютерную технологию.
После внедрения Intuiflow становится элементом (подсистемой) общей информационной системы производственного предприятия. Среди функций этого автоматизированного решения задач MRP — обеспечение оперативной оценки и контроля ситуации с поставками ресурсов и логистикой.
Примеры успешного применения автоматизированной системы управления производством
Одно из требований экономической практики – постоянное совершенствование инструментов работы с информацией. Прежде всего, структура MRP должна предусматривать безопасное хранение и постоянное обновление данных. Также ключевым элементом этой подсистемы является обеспечение постоянного доступа менеджмента производства и специалистов по снабжению к актуальным данным. Важную роль играют и возможности систематизации и выборки показателей, группировка массивов данных для анализа и исследований, визуализация полученных результатов.
Методы управления производством
Каждое предприятие для решения производственных задач использует наработанное сочетание средств и методов, которые и составляют управленческий механизм. Концепция DDMRP, базируясь на лучших практиках производства и логистики, может успешно применяться для реализации таких управленческих функций как прогнозирование, планирование, организация, координация, контроль.
MRP, основанная на данных реального спроса, усиливает эффект привычных экономических (оптимизация затрат, контроль себестоимости продукции и т.п.) и организационно-распорядительных методов. В частности, стабильность производства достигается, в том числе, и за счет элементов нормирования (лимиты нижних и верхних пределов запасов, динамические буферы и т.п.) и заложенных в логику АСУ алгоритмов реагирования на колебания спроса, задержки поставок и другие подобные ситуации.
Внедрение спросоориентированной MRP в компании
Внедрение DDMRP проходило в такой последовательности:
- Стратегическое позиционирование запасов;
- Расчет уровней и формирование профилей буферов;
- Определение динамических буферов;
- Использование при планировании методов, предусматривающих ориентацию на спрос;
- Реализация всех перечисленных разработок.
По результатам анализа объема и периодичности колебаний спроса на изделия, сама концепция спроса была изменена следующим образом:
— спросом стали считаться только согласованные по количеству и дате поставки заказы;
— прогнозы и заказы без определенного временного горизонта перестали приниматься в расчет при планировании.
На момент внедрения DDMRP, всех потребителей продукции компании можно было разделить на такие типы:
Обобщенная характеристика клиентов:
КЛИЕНТ А
- Осуществлялся ежедневный прогноз с горизонтом в 3 месяца
- Ежедневный расход запасов на уровне реальных заказов, авансирование проводилось на уровне одного ежедневного расхода.
- Точность прогноза принималась как Довольно высокая
- Время выполнения заказа оценивалось в среднем в размере 10 дней
- Применялись буферы для Сырья и готовой продукции
КЛИЕНТ “B”
— Ковка и механическая обработка
- Поступали еженедельные прогнозы для последующих 6 месяцев
- Консигнационный запас фиксировался на уровне ежедневного расхода
- Точность прогноза принималась как низкая
- Время выполнения заказа равнялось приблизительно 20 дням
- Характерными были резкие, скачкообразные колебания заказов
КЛИЕНТ “C”
- Давался еженедельный прогноз на 9 месяцев
- Для запасов принимался во внимание еженедельный расход
- Достаточно достоверным считался прогноз только на первой неделе
- Продолжительность выполнения заказа составляла, в среднем, 15 дней
- Номенклатура поставок состояла из 150 позиций
КЛИЕНТ “D”
- Условия сотрудничества предусматривали достаточно времени для удовлетворения спроса с момента размещения заказа. Сырье заготавливалось и поставлялось под конкретный заказ.
Как отмечалось выше, на первом этапе перехода на DDMRP происходило Стратегическое позиционирование запасов.
Внедряемая модель предусматривала исследования на всех производственных стадиях: получение сырья, производство полуфабрикатов, выпуск готовой продукции. На этом этапе ставились цели:
- сокращения времени выполнения заказа;
- снижения объемов некорректной информации, возникающей из-за неточных прогнозов покупателей или задержек поставок сырья и материалов.
Второй этап заключался в расчете уровней и формировании профилей буферов.
Приведем примеры буфера. Путем расчетов ббыли установлены уровни пополнения деталей в Буфере:
- Красная зона — 5 рабочих дней
- Желтая зона — 5 рабочих дней
- Зеленая зона — в объеме Производственной партии (ежемесячно)
- Оповещения Intuiflow — 10 дней
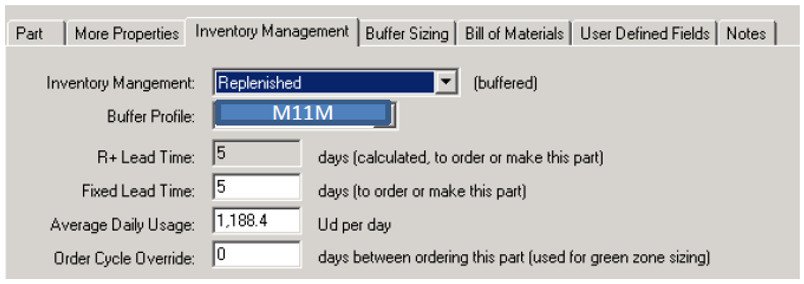
Уровни пополняемых деталей в Буфере
Третий этап состоял во внедрении динамических буферов.
Было введено правило, по которому менеджеры по планированию должны:
- получать информацию о любых внеплановых корректировках заказов и планов выпуска продукции, чтобы иметь возможность учесть такие изменения в параметрах буферов;
- периодически пересматривать режим применения буферов, осуществляя, в случае необходимости, их перенастройку.
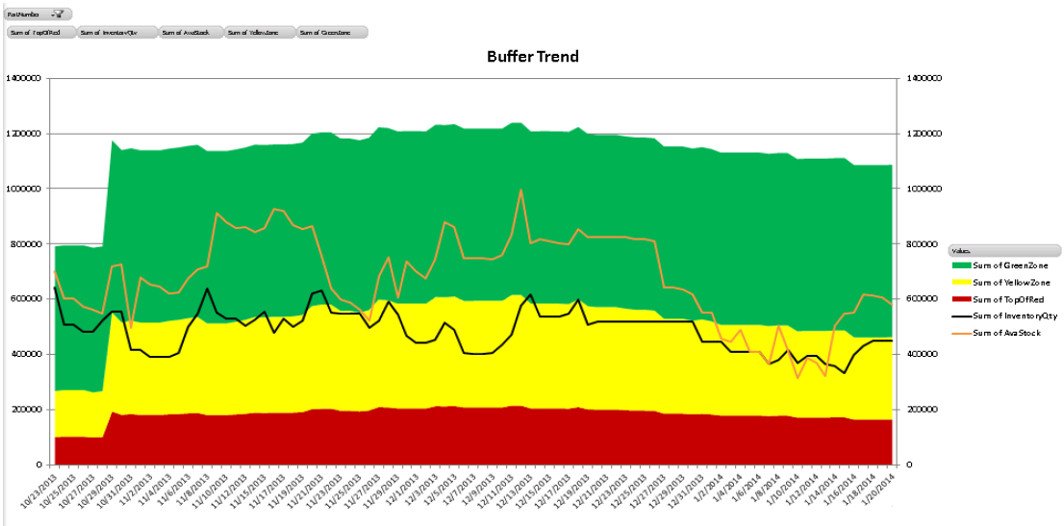
Динамические буферные корректировки
Затем, в рамках четвертого этапа, в практику управления производством продукции предприятия вводился принцип ориентации на спрос.
При реализации такого подхода специалисты по производственному планированию видят движение и остатки запасов сырья, имеют возможности оперативного реагирования путем подачи новых заказов на закупку. Также отслеживается ситуация по выполнению поступивших заказов на продукцию.
Благодаря правильно настроенному спросо-ориентированном планированию, менеджеры всегда вовремя получают информацию о:
- возможности размещения нового заказа на продукцию;
- потребности в подаче поставщикам заказов на сырье и материалы;
- результатах сопоставления ежедневной и еженедельной информации;
- необходимости быстрого реагирования на поступившие заказы.
Пятый этап – завершение обучения и аттестация персонала, подготовка документации, имплементация подхода DDMRP в бизнес-процессы, адаптация и настройка АСУП Intuiflow.
DDMRP -спросоориентированная система управления производством продукции
Для управления потоками необходимо выделение заказов, требующих внимания и контроля. SATUERCA использует около 60 позиций сырья, на момент старта пятого этапа проекта критически необходимо было контролировать поставку сырья по 6 наименований, а мониторинг по еще 7 наименованиям материалов был важен в ближайшей перспективе. Соответственно, в центре внимания оказались SKU, чей удельный вес в общем количестве составлял 18%.
Когда команда планирования видит актуальную картину наличия запасов на складах предприятия, то сразу выделяются заказы, которые необходимо внимательно отслеживать.
Для рациональной работы системы управления потоками по концепции DDMRP важно выполнять два необходимых условия – корректность и актуальность данных по запасам и товарам, а также своевременная обработка информации о спросе.
Результаты внедрения новой системы управления производством продукции
- Снизилось количество ситуаций, в которых необходимы корректировки производственных планов
- Улучшились показатели эффективности использования производственных мощностей
- Достигнут высокий уровень точности планирования производства на недельный период
- Подсистема планирования стала лучше реагировать на колебания спроса, что подтверждается сравнением ежедневных актуальных данных с еженедельной информацией.
- Полнее используется потенциал компании, при этом показатели уровня обслуживания поддерживаются на высоком уровне (98 + %)
- Количество запасов поддерживается на оптимальном уровне, что позволяет обеспечивать все производственные запросы.
Наиболее ярко преимущества новой системы управления запасами проявились для клиентов типа Б.
Так, ранее, для того, чтобы запустить кузнечно-прессовое производство, необходимо было иметь прогноз как минимум на следующие три недели. При этом через две недели, когда выкованные детали поступали в Mecanifran, необходим был новый прогноз, который должен был показать, требуются ли эти позиции для следующей технологической стадии.
Как следствие использования таких неточных прогнозов, запасы не контролировались в достаточной степени. Отсутствовали виды сырья и материалов, которые были необходимы, но, в то же время, детали, прошедшие ковку, могли уже и не понадобиться. Такие ситуации были постоянной проблемой для всех звеньев производственной цепи компании и ее партнеров.
Результатами внедрения методологии DDMRP и разработанного на ее принципах программного обеспечения Intuiflow стало:
- Повышение качества управления запасами, за счет использования буферов, по каждой стратегической позиции
- Сокращение времени выполнения заказа на поставку — на 50% (от 20 до 10 дней)
- Уменьшение объема запасов (3,700,000 деталей до 2,700,000 деталей — т.е. на 35% за три месяца)
- Снижение производственных и управленческих рисков — уменьшение количества форс-мажорных ситуаций, случаев искажения информации, неточных прогнозов
- Рациональное использование производственных мощностей – появилась возможность использовать только то, что действительно необходимо.
Признаки эффективного управления производственной деятельностью предприятия
Многие производственные предприятия переживают трудности, схожие с теми, с которыми ранее сталкивалась SATUERCA GROUP. Ведь совершенствование структуры управления запасами также же важно в промышленности, как и технические инновации.
В рассмотренном нами кейсе реализация MRP, основанной на данных о фактическом спросе, обеспечила более высокое качество управленческих решений, стабильность производства. Так сочетание передовых управленческих и информационных технологий, характерное для методологии DDMRP и программного обеспечения Intuiflow, позволяет лучше реализовать потенциал производственных компаний в разных отраслях промышленности.
Оригинал кейса Satuerca Group здесь http://demanddrivenworld.com/conference/