Оптимизация ассортимента продукции предприятия
На первый взгляд, оптимизация ассортимента продукции производственного предприятия — не приоритетная задача, однако за ней скрываются возможности для увеличения прибыли.
Предлагаем вашему вниманию кейс международной производственной компании, которая оптимизировала управление ассортиментом продукции по Теории ограничений — ТОC.
Оптимизация ассортимента как главная цель Fleetguard Filters Pvt Ltd
Индийская компания
предоставляет мировые решения для обеспечения защиты от проблем с двигателем. Начиная от фильтрации воздуха, смазки, топлива, гидравлики и воды, и заканчивая химическими веществами. Компания занимается производством воздушных и масляных фильтров и реализует продукцию через розницу и дистрибьюторскую сеть.
— это надежный производитель фильтрующих продуктов в Индии, который внедряет инновационные решения для всех потребностей в фильтрации.
Цель: оптимизация ассортимента и увеличение прибыли в 7 раз за 4 года
Проанализировав ситуацию в компании, мы определили главную проблему.
Проблема: загрузка производства на 100%, но продажи низкие
Завод, имея широкий ассортимент товаров, сделал ставку на производстве продукции с наибольшей маржой. На первый взгляд, логика верна: произвести больше того, что генерирует больше денег. Однако, при размещении заказов на производство, не учитывался реальный спрос на товары. В итоге, продукция с высокой маржой, будучи невостребованной рынком, приносила убытки и замораживала оборотные средства. Товар насильно «сплавлялся» дистрибьюторам, которые требовали увеличения кредитного периода, мотивируя тем, что у них нет денег, поскольку предыдущая партия товара не продана. Отношения с дистрибьюторами испортились, они отказались от размещения своих заказов на заводе, и приступили к поиску альтернативных производителей. Прибыль снизилась у всех.
Решение: Динамическое управление буфером — инструмент ТОС
В поиске решения, были включены все
участники цепочки поставок
: поставщики, завод, склад и дистрибьюторы. Вместе с дистрибьюторами, которые предоставили данные о продажах, был проанализирован
ассортимент завода
и классифицирован по:
- графику производства (на склад, на заказ)
- востребованности (ходовые и неходовые)
Стало понятно, что ассортимент и количество производимой заводом продукции, не совпадали с фактическим спросом. Возникла задача оптимизации ассортимента продукции предприятия. Для того, чтобы сбалансировать выпуск товаров с тем, что необходимо потребителю, решили внедрить один из важнейших инструментов ТОC —
динамическое управление буфером.
Система буферов позволяет поддерживать запасы в каждой точке цепи поставок на оптимальном уровне, без излишков и недостач. Буфер запасов реагирует на изменение спроса, сравнивает его с уровнем остатков в точке хранения, рассчитывает необходимое количество пополнения запаса и сигнализирует предыдущему звену в цепи поставок о том, какой продукт и в каком количестве необходимо пополнить.
Условно, буфер запасов разделяется на три равные (по 33%) зоны:
зона риска, оптимальная зона и безопасная зона.
В натуральном выражении, количество запасов, соответствующее той или иной зоне, рассчитываются в каждом отдельном случае на основе спроса на конкретную товарную позицию в конкретной точке хранения.
Так, у каждого звена цепи появился свой
буфер (см. рис.), отражающий уровень существующих запасов в каждом пункте ассортимента и в каждом звене цепочки поставок.
Это изменило работу всей системы (смотрите ниже).

Рис. 1. Оптимизация ассортимента. Буфер запасов
Дистрибьюторы брали за основу ежедневные данные по продажам и размещали заказ на такое количество продукции, чтобы уровень запасов каждого товара на полке находился
в
желтой зоне буфера
. Заводской склад обрабатывал заказы и направлял их на завод с указанием очередности производства и количества товаров.
Такая
система приоритетов
строится на основе фактического спроса и показателей буферов, а также структурирует:
- Производство товаров
- Поставки сырья
- Отгрузки готовой продукции дистрибьютору
Буфер заводского склада показывал заводу, какую именно продукцию необходимо произвести и в какой очередности, а также сформировал
график отгрузок
дистрибьюторам: в первую очередь, производились и доставлялись товары, находящиеся в красной зоне.
Итоги оптимизации ассортимента продукции предприятия
Благодаря проведенной работе по оптимизации ассортимента продукции предприятия и внедрения динамического управления буферами, были достигнуты впечатляющие показатели наличия продукции на всех этапах цепочки поставок:
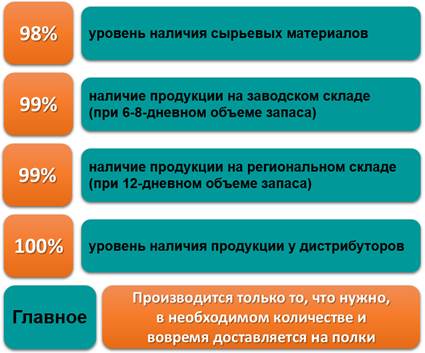
Рис.2 Показатели наличия продукции
Благодаря постоянному наличию востребованного ассортимента:
- Прибыль выросла у всех участников: начиная от завода, заканчивая дистрибьюторами.
- Увеличилась оборачиваемость, а денежные средства не замораживаются в ненужных товарах.
- Эффективно используются производственные мощности.
Смотрите видео:
«Как и зачем ABM Cloud управляет товарными запасами?»